Surface modification is an essential technique to enhance the application performance of calcium carbonate. It improves its adaptability, expands market reach, and increases usage. Functionalization and specialization will dominate the future development of calcium carbonate. The market demand for various specialized surface-modified calcium carbonate products is expected to grow significantly.
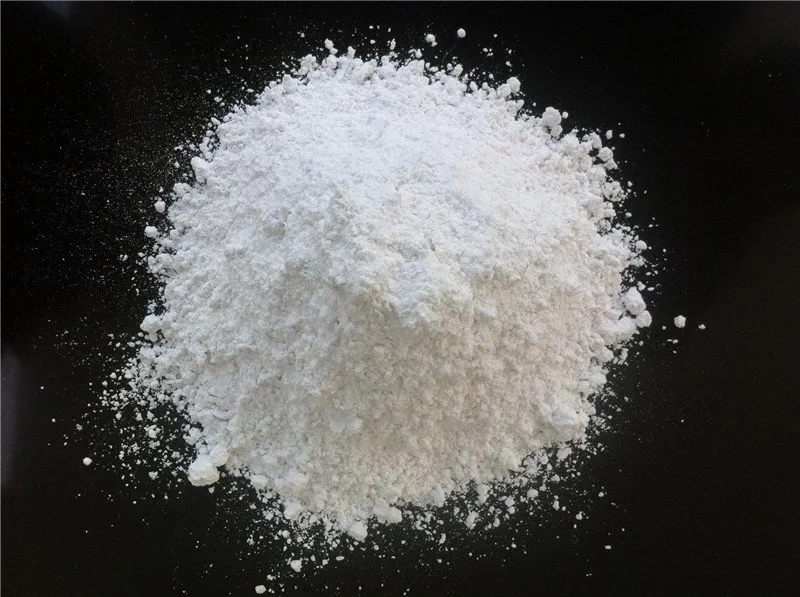
The 7 reasons for surface modification of calcium carbonate
Improve the dispersibility of calcium carbonate
Ultrafine processing is a crucial approach to enhance calcium carbonate quality. However, as the particle size decreases, surface energy increases, adsorption intensifies, and agglomeration becomes more severe.
Through surface modification, modifiers can directionally adsorb onto calcium carbonate surfaces, imparting charge characteristics. Due to repulsion between like charges, calcium carbonate particles resist agglomeration, achieving uniform dispersion within the matrix.
Improve the compatibility of calcium carbonate
Surface modification enhances the interfacial compatibility and affinity between calcium carbonate and organic matrices. This improves the mechanical properties of composite materials, such as rubber or plastics.
For example, calcium carbonate treated with titanate coupling agents has good compatibility with polymer molecules.
Titanate coupling agents can form molecular bridges between calcium carbonate molecules and polymer molecules.
This enhances the interaction between the organic polymer or resin and calcium carbonate. This significantly enhances the mechanical properties of thermoplastic composites, including impact strength, tensile strength, flexural strength, and elongation.
Reduce the oil absorption of calcium carbonate
Surface modification is an important method to reduce the oil absorption of powders. After surface modification, calcium carbonate particles are less aggregated, and their dispersion is improved. The voids between particles are reduced. At the same time ,the modification molecules cover the surface of the calcium carbonate. This coverage reduces the internal voids within the particles. Additionally, this coverage changes the surface properties of calcium carbonate, weakening its surface polarity.
The friction between particles decreases, and lubricity improves. As a result, the particles pack more tightly, increasing the bulk density and reducing the oil absorption value.
Expand the high-end application market for calcium carbonate
Calcium carbonate without surface modification has poor compatibility, is prone to agglomeration, and performs poorly in applications. As the usage increases, these drawbacks become more apparent.
Through surface modification, calcium carbonate exhibits good interfacial affinity. The oil absorption is reduced. It can be better applied in high-end fields such as plastics, coatings, rubber, papermaking, sealants, and breathable films.. This improves product quality while further reducing production costs for companies.
Endow calcium carbonate with more functional properties
Calcium carbonate without surface modification can only be used as a traditional filler, with its application areas and usage limited. However, through surface modification, calcium carbonate transforms into a multifunctional modifier. Calcium carbonate coated with silica can partially replace white carbon black and supplement its shortcomings in certain properties. Lightweight calcium carbonate coated with metals can enhance specific properties of rubber products. Calcium carbonate composite materials coated with titanium dioxide can, to some extent, replace titanium dioxide. Calcium carbonate treated with phosphates, aluminates, silicates, or barium salts can be used to prepare acid-resistant calcium carbonate.
Increase the added value of calcium carbonate products
Currently, there is an oversupply of regular calcium carbonate in China, and price competition for products is intense. After surface modification, the performance of calcium carbonate is significantly improved, resulting in a better user experience. And the product price naturally increases.
Align with the development trends of the calcium carbonate industry
The National Development and Reform Commission (NDRC) has listed ordinary-grade calcium carbonate as an outdated product in the Industrial Structure Adjustment Guidance Catalog (2024 Edition).
Efforts to phase out such products will intensify in the coming years.
This policy clarifies China’s strategic direction for the calcium carbonate industry:
- Eliminate low-end, fragmented production capacities.
- Encourage the development of precision-processed products like ultrafine and nanoscale calcium carbonate.
34 applications of modified calcium carbonate
After surface modification, calcium carbonate will be better used in the following fields.
Polyvinyl chloride (PVC)
Compared to regular calcium carbonate, the particles of modified calcium carbonate are evenly distributed in their native particle state without agglomeration. It has excellent compatibility and dispersibility with PVC resin. It is easy to plastify, does not stick to rollers, and has excellent processing performance. This improves processing efficiency. The product’s tensile strength and elongation at break are significantly increased, resulting in good physical and mechanical properties.
polypropylene (PP)
Surface modification of lightweight calcium carbonate with the coupling agent polytetrahydrofuran homopolymer ether (PTHF) can reduce the oil absorption of calcium carbonate to 22% and the contact angle to 68.6°. The modified calcium carbonate is filled into polypropylene. It disperses well in polypropylene. It can alleviate the decrease in tensile strength to some extent. The elongation at break of the composite material reaches 28.47% impact strength reaches 6.7 kJ/m²
The impact strength reaches 6.7 kJ/m²
High density polyethylene (HDPE)
Aluminate coupling agent is used for the mechanochemical modification of heavy calcium carbonate.
The aluminate coupling agent forms certain bonding interactions on the surface of the calcium carbonate particles.
After modification, the dispersion of the calcium carbonate particles is significantly improved.
As the amount of modified calcium carbonate increases in high-density polyethylene (HDPE).
The wear loss and friction work of the composite material decrease, and its anti-friction performance improves.
When the amount is 8 phr, the composite material exhibits the best mechanical properties. The tensile strength and impact strength increased by 4.46% and 24.57%, respectively.
Low density polyethylene (LDPE)
Stearic acid (1.5%) and DL-411 aluminate (0.5%) were used to modify the calcium carbonate.
The activation index of the modified calcium carbonate is 99.71%. The oil absorption value is 46.19 mL/100g. The final sedimentation volume is 2.3 mL/g. The viscosity of a mixture of 10g modified calcium carbonate and 100mL liquid paraffin is 4.4 Pa·s.
When the modified calcium carbonate is filled into low-density polyethylene (LDPE), and the content of modified calcium carbonate is 10%, the composite material exhibits good mechanical properties.
ABS plastic
After surface modification, nano-calcium carbonate shows improved dispersion in organic media, with its surface changing from hydrophilic to lipophilic. When used in ABS resin, it enhances the mechanical properties of the ABS resin, such as impact strength, tensile strength, surface hardness, bending strength, and thermal properties like heat distortion temperature.
Polyester (PBAT)
Surface modification of calcium carbonate is performed using a double-layer coupling agent coating method. The modified calcium carbonate can be filled up to 50%, and the composite material exhibits good overall mechanical properties. In the composite material, the modified calcium carbonate particles are completely impregnated and coated by the PBAT resin matrix, with no dissolution occurring. At the same time, the mutual flowability between the two is improved.
Radiation cross-linked EPDM
In-situ modification of calcium carbonate is carried out using a titanium ester coupling agent (105) with unsaturated functional groups. The dispersion of the modified calcium carbonate is improved. In radiation-crosslinked EPDM, the surface of the modified calcium carbonate reacts chemically with EPDM through oleic acid groups. This allowed calcium carbonate to participate in the crosslinking network of EPDM. As a result, the tensile strength, 100% elongation stress, and Shore A hardness of the composite material were improved. The calcium carbonate exhibited reinforcing properties in radiation-crosslinked EPDM.
Polylactic acid (PLA)
The calcium carbonate was surface-modified with a coupling agent. This increased the specific surface area of the calcium carbonate. As a result, the contact area with the matrix was enlarged.
When subjected to stress, more silver streaks and plastic deformation zones were generated.
This absorbed a large amount of energy, achieving the purpose of toughening and strengthening the material.
PVC coated fabric
Modified heavy calcium carbonate can improve the compatibility of the polyvinyl chloride paste resin system. At the same usage level as regular heavy calcium, it can achieve a relatively low viscosity.
It enhances the adhesion to polyester fabric, reducing the amount of adhesive needed. At the same time, it improves the tactile feel of the coating material. When the usage amount is increased by 40%, it has no adverse effect on the material’s processing performance, physical mechanical properties, or thermal welding performance.
Polyvinyl chloride (PVC) fire hose
Compared to regular calcium carbonate, the modified calcium carbonate particles are evenly distributed in their native particle form.
They do not agglomerate, and some exist in the form of nanoparticles.
When filled into PVC fire-fighting pipes, it not only improves the processing performance of the system, but also provides the product with better physical and mechanical properties, achieving a toughening and reinforcing effect.
PVC cable materials and flame retardant masterbatch
Heavy calcium carbonate is modified using aluminates, titanates, and stearic acid as coupling agents. This modified heavy calcium carbonate composite filler is then used to prepare PVC cable compounds and flame-retardant masterbatches, exhibiting excellent performance. The use of composite modifiers will become one of the key trends in the surface modification of heavy calcium carbonate.
Polyetheretherketone
The carbon calcium whiskers are modified with sulfonated hyperbranched polyarylether ketone.
This improves the dispersion of the calcium carbonate whiskers in the matrix.
It enhances the interaction between the two phases.
It also reduces the melt viscosity of the composite material within the processing temperature range.
At the same time, the resulting composite material shows improved Young’s modulus, bending modulus, and toughness.
plastic film
Calcium carbonate has a wide range of applications in films. After surface treatment, calcium carbonate typically combines with the base resin through surface adsorption, physical entanglement, van der Waals forces, and other mechanisms. This results in a more uniform dispersion and improved film properties.
Food plastic packaging
Nano-calcium carbonate, as an ultra-fine filler in plastics, has special effects in modifying product performance. Studies have shown that nano-food packaging materials possess barrier, antibacterial, and preservation properties. These properties have been applied in packaging for beer, beverages, fruits, vegetables, dairy products, and other foods. To achieve a good dispersion and small particle size of the filler, it is necessary to weaken or reduce the nanomaterial’s surface energy. Currently, mechanical dispersion methods are commonly used, or dispersants and drying treatments are applied.
Breathable membrane
The breathable film is made by blending about 50% of special calcium carbonate with a PE or PP carrier.
It is then extruded into a film and oriented at a certain stretch ratio.
It is widely used in medical adhesive films, surgical garments, medical gloves, sanitary napkins, baby diapers, disposable bed sheets, cling films, composite films, and cooked food packaging bags.
The surface-modified calcium carbonate exhibits better-than-expected hydrophobic properties, excellent dispersibility, and thermal stability.
These characteristics make it suitable for breathable film production.
Room temperature vulcanizing (RTV) one-component silicone rubber sealant
Surface modification of ultrafine calcium carbonate is performed using a silane coupling agent. The modified calcium carbonate shows a good reinforcing effect in sealants, with a tensile strength of 0.57 MPa and a maximum strength elongation of 159.60%.
Polyurethane sealant
Calcium carbonate modified by copolymerizing methyl methacrylate (MMA) with silane coupling agent KH570 has a water contact angle of 60° and a sedimentation value of 1.36 ml/g. The modified calcium carbonate shows good dispersion in polyurethane and demonstrates thixotropic behavior when mixed with polyurethane. Additionally, it improves the mechanical properties of polyurethane better than unmodified calcium carbonate.
Silicone Sealant
Nano calcium carbonate can partially replace white carbon black as a filler for silicone rubber. It is a primary production material for silicone rubber. Nano calcium carbonate acts as both a filler and an enhancer for silicone rubber. It can significantly reduce the cost of the products and improve their processing performance. It greatly increases the tensile strength, tear strength, and other mechanical properties of the rubber. By controlling the crystal form, particle size, and surface treatment of nano calcium carbonate, the products can achieve excellent thixotropic performance and anti-sag properties.
Rubber Products
Surface-modified active calcium carbonate has a reinforcing effect in rubber. Its reinforcing performance is comparable to that of white carbon black. It is commonly used as a reinforcing agent for white, light-colored, and colored rubber products. It can be used in the production of tire buffer layer rubber, inner tubes, bicycle tires, conveyor belt cover rubber, hoses, rubber tape products, and rubber shoes. It is also suitable for natural rubber, SBS, and latex. The reinforcing effect in SBS is significant, and its coloring performance is also good.
Natural Rubber Vulcanized Rubber
Phloroglucinol and hexamethylenetetramine are used to modify calcium carbonate. The modified calcium carbonate natural rubber vulcanizate shows significant improvement in mechanical properties compared to the unmodified calcium carbonate natural rubber vulcanizate. The tensile strength at break of the natural rubber vulcanizate increased by 130% compared to unmodified calcium carbonate. The tensile strength increased by 101%, and the tear strength increased by 70%.
Styrene-Butadiene Rubber (SBR)
Calcium carbonate modified with carboxylated polybutadiene (CPB) as a reinforcing agent in SBR significantly improves the vulcanized rubber properties. Compared to unmodified calcium carbonate, the tensile strength increases by 60%, the 300% elongation stress increases by 70%, and the tear strength improves by 30%.
Semi-steel Radial Tire Inner Liner
Adding 40 parts of modified calcium carbonate to the inner liner of semi-steel radial tires enhances the air tightness of the rubber compound. It has minimal effect on its flexural resistance and processing performance. According to factory test results, the air-impermeable layer with 40 parts of modified calcium carbonate shows a 30% improvement in air-tightness compared to a standard air-impermeable layer. At the same time, the cost is reduced by 3.65 yuan/kg, and the tire’s high-speed and durability performance remain unaffected.
Paper Filler
Starch-coated modified calcium carbonate is used as a filler in papermaking. The modified calcium carbonate has strong shear resistance and a high retention rate. This results in higher paper strength performance. The decrease in strength performance is significantly slowed down.
Reconstituted Tobacco
Sodium hexametaphosphate and citric acid (in a 1:1 ratio) were used to modify calcium carbonate.
The modified calcium carbonate added to reconstituted tobacco has an ash content 8.25% higher than commercial calcium carbonate. The conventional smoke indicators and sensory evaluation results are better than those of commercial calcium carbonate
Powder Coating
Modified calcium carbonate acts as a framework in powder coatings. It increases the film thickness and improves the abrasion resistance and durability of the coating. Generally, modified calcium carbonate is cheaper than other inorganic fillers. Therefore, it can reduce the cost of powder coatings. At the same time, it improves the powder pickup rate and spray coverage.
Latex Paint
Modified nano-calcium carbonate is used to prepare latex paint containing 43% PVC. The paint with modified nano-calcium carbonate exhibits excellent surface smoothness, density, and significantly improved resistance to staining, scrubbing, and aging. Among the modifiers, stearic acid and sodium sulfonate-modified nano-calcium carbonate have a significant impact on tensile strength, while stearic acid and titanate-modified nano-calcium carbonate greatly enhance the resistance to staining and scrubbing.
Electrophoretic Coating
Calcium carbonate is modified with hydrated fluorosilicate. After modification, the surface of calcium carbonate is covered with an amorphous mixture of silica and calcium fluoride. This forms a dense thin film. It significantly enhances the acid resistance of calcium carbonate. It can be used in weak acid anodic electrophoretic coatings.
PVC Automotive Chassis Anti-stone Chip Primer
After modification with fatty acids or fatty acid salts, calcium carbonate with particle sizes of 40–80 nm shows excellent thixotropic properties. It is used in PVC automotive chassis anti-stone impact primers. This results in good thixotropy and yield stress.
Inks
Ink made with modified calcium carbonate has good body and viscosity. It has excellent printing performance and dries quickly without side effects. Due to its small particle size, it shows superior dispersion, transparency, gloss, and opacity in ink products. It also has excellent ink absorption and drying properties. As a result, the printed products are fine and have complete dots. Especially with the widespread use of resin binders in ink, modified calcium carbonate, with its excellent stability, has almost replaced other fillers.
Toothpaste
Guangdong Lafa Personal Care Products Co., Ltd. uses silica to coat micron-sized spherical calcium carbonate particles. This surface modification of calcium carbonate as a toothpaste abrasive improves its compatibility with fluoride. With the same wear value, the modified calcium carbonate added to the toothpaste shows significantly improved compatibility with fluoride.
Personal Care Products
Adding active nanoscale calcium carbonate to cosmetics makes the product finer and smoother. As an additive, it is used in setting powders to reduce shine, improve skin adhesion, and provide moderate oil absorption and anti-sweat properties. Used in smoothing powders, it is non-irritating to the skin, provides even color, and offers some coverage.
Artificial Granite
Surface-modified calcium carbonate, with a low oil absorption value, is an important raw material for artificial stone production.
Composite Conductive Powder
Surface-modified calcium carbonate enhances acid resistance in acidic environments. The calcium carbonate is then compounded with polyaniline to prepare a composite conductive powder. This not only imparts good conductivity to calcium carbonate but also improves the processing and molding challenges of pure polyaniline. It has broad application prospects.
Lubricating Oil
Adding modified active nanoscale calcium carbonate during the digestion process reduces the negative impact of surfactants on lubricating oils. It enhances the dispersion stability of nanoscale calcium carbonate in lubricating oils, improving their anti-wear and friction-reducing properties.