PE wax, also known as polymer wax or polyethylene wax, is used in powder coatings. It mainly improves coating hardness, wear resistance, adjusts gloss, and enhances extrusion efficiency. Compared to polypropylene, polytetrafluoroethylene(PTFE), and polyamide waxes, it offers better economic applicability.
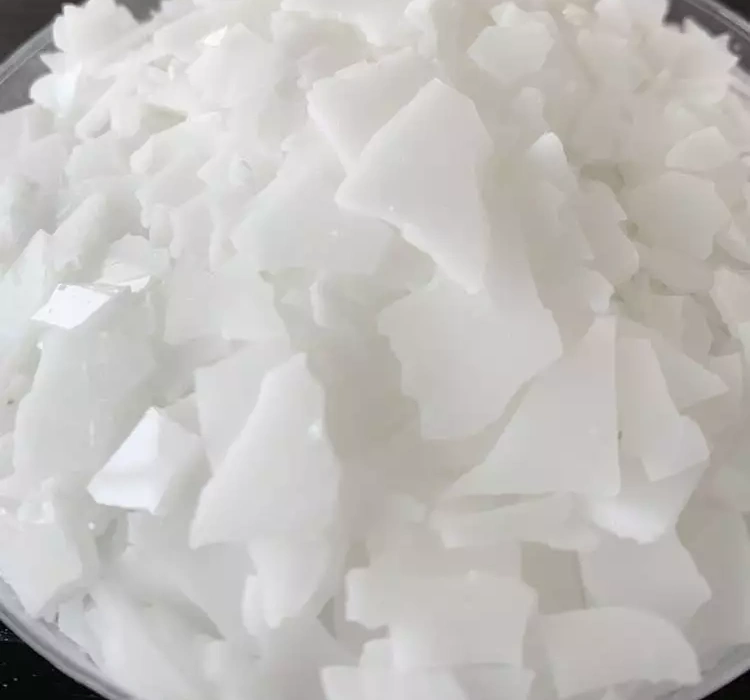
Click to view the latest industry report
Scratch resistance
During coating curing, wax powder particles float to the surface. They become contact points for surface friction, reducing damage to the coating. Therefore, wax powder slip and anti-friction properties are interrelated. However, wax with a low friction coefficient doesn’t always provide good wear resistance. Wax melting point and particle size are key factors affecting wear resistance. High melting point polyethylene wax is usually better than low melting point wax. Larger particle sizes generally perform better than smaller ones. However, large particle size wax tends to have more noticeable matting effects.
Improving hardness
Coating hardness is a key performance indicator of powder coatings, directly affecting the durability and wear resistance of the coated surface. By increasing the hardness, the coating becomes more resistant to scratches, abrasion, and mechanical stress. High melting point polyethylene wax is especially effective in improving this hardness, as it creates a more rigid and stable surface. Additionally, polypropylene, polytetrafluoroethylene, and modified polyethylene waxes contribute to further enhancing the coating’s mechanical properties. These waxes not only increase hardness but also help to improve the overall performance, ensuring longer-lasting, more robust coatings for various applications.
Improved Slipperiness
Low-melting point and high-melting point polyethylene waxes can significantly improve the smoothness of the coating by reducing surface roughness and enhancing the overall appearance. This is especially important in applications where a smooth, glossy finish is desired. When working with recycled powder systems or sand grain extrusion, adding flake polyethylene wax plays a crucial role in optimizing the production process. It helps in easier feeding of the material into the system, promoting better flowability and reducing blockages. Additionally, it increases production efficiency by facilitating smoother extrusion and reducing the wear and tear on the screws, ultimately extending the lifespan of the equipment and minimizing maintenance costs. This makes polyethylene wax a highly effective and cost-efficient additive in various manufacturing processes.
Anti-adhesion
When two surfaces are in close contact, especially under heat and pressure, the coating film is prone to sticking together. This can cause issues during processing, such as defects or equipment damage. By adding PE wax, the slip of the coating is significantly increased, reducing friction between the surfaces. Additionally, PE wax acts as an anti-adhesion agent, preventing the coating from sticking and ensuring smoother processing. This dual effect helps to maintain the integrity of the coating and improves overall efficiency, particularly in high-temperature or high-pressure applications where sticking is a common concern.
Rheology control
Adding 0.5-0.8% of a polyethylene and amide mixed wax to the powder coating formula can significantly improve the fluidity of the dry powder. This enhancement in flowability helps the powder move more smoothly during application, ensuring a more uniform and consistent coating layer. The improved fluidity also aids in stabilizing pigment dispersion, preventing pigments from settling or clumping, which can result in color inconsistencies. Additionally, this combination of waxes helps to reduce sagging, especially when applying coatings to vertical surfaces or complex geometries, ensuring a smoother and more controlled finish. Overall, the use of polyethylene and amide mixed wax helps to enhance the quality, performance, and aesthetic of the powder coating.
Gloss control and fullness improvement
When the amount added is small, polyethylene wax has little effect on the gloss of the coating. When the amount added is large, it can be used alone or with matting powder as a matting agent. Compared with silica products used alone, wax powder provides a fuller coating and is not easy to settle. This type of wax powder is better in fine powder form and can be evenly dispersed on the surface of the coating to control the gloss. It can also improve the density of the coating.
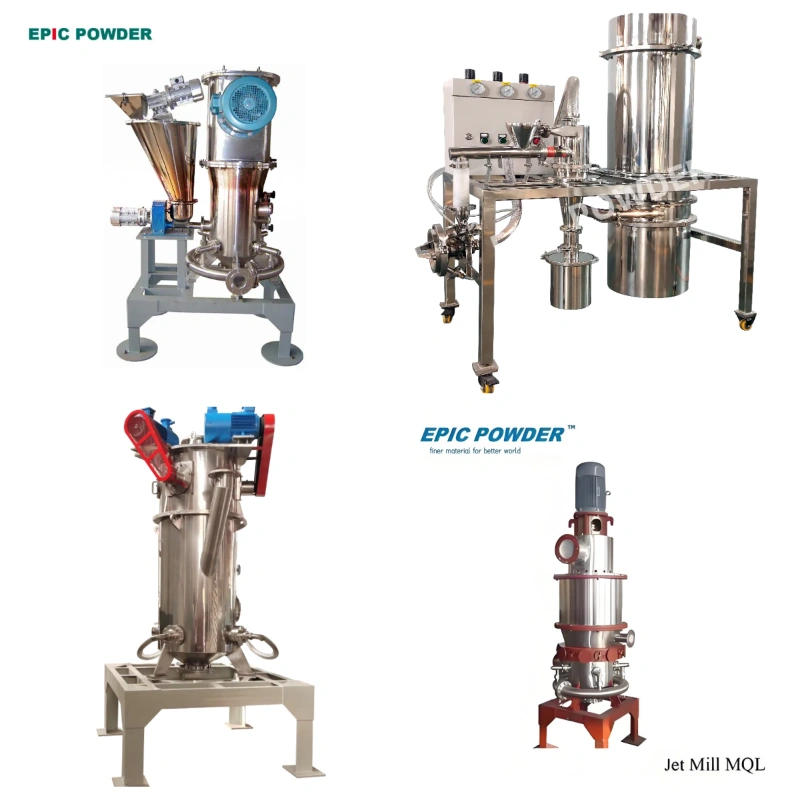
epic powder
Epic Powder, 20+ years of work experience in the ultrafine powder industry. Actively promote the future development of ultra-fine powder, focusing on crushing, grinding, classifying and modification process of ultra-fine powder. We have PE wax jet mill grinding projects in India, Uzbekistan, etc. and have received unanimous praise from customers. Contact us for a free consultation and customized solutions! Our expert team is dedicated to providing high-quality products and services to maximize the value of your powder processing. Epic Powder—Your Trusted Powder Processing Expert !