Physical properties of Ultramarine
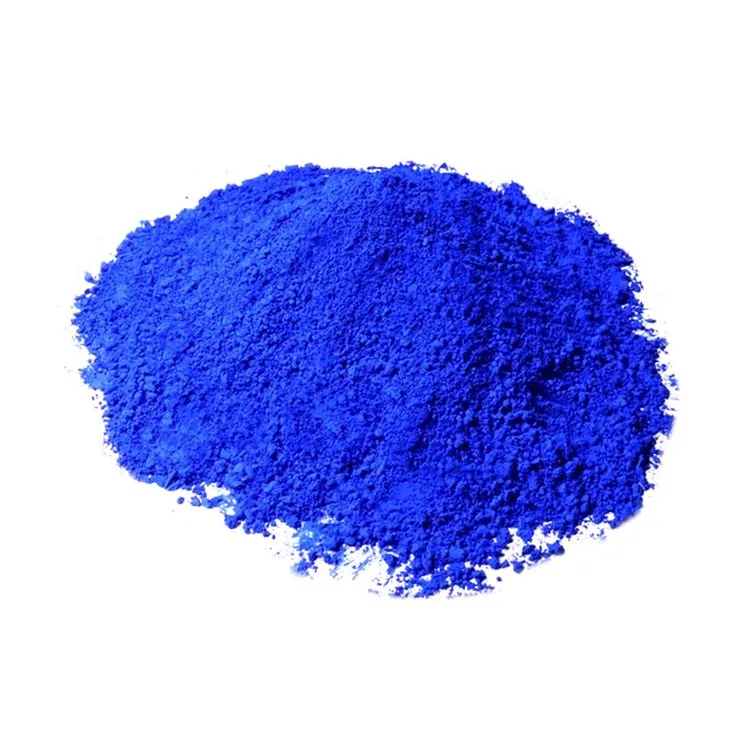
- Ultramarine blue pigment is an inorganic pigment with a mean particle size of 1.5-2.5 microns. The particle size distribution typically ranges from 0.1 to 30 microns. Like other inorganic pigments, ultramarine blue is prone to agglomeration. This agglomeration can affect the dispersion performance.
- The specific gravity of ultramarine blue is around 2.3. The particles are not pre-dispersed, and the oil absorption is between 35-45. This leads to high viscosity and poor flowability.
- Ultramarine blue is transparent and has high vividness.
- The standard moisture content of ultramarine blue is generally less than or equal to 0.6%.
- The mechanical, physical, and chemical properties of ultramarine blue pigment are very stable during processing and use.
- Ultramarine blue is not acid-resistant and is unsuitable for products exposed to acidic substances.
The dispersion process of ultramarine blue pigment
- Wetting: The interface between ultramarine blue pigment and water or air becomes the interface between the pigment and the coloring medium.
- Dispersion: External forces are applied to forcibly break the agglomerates of ultramarine blue pigment particles.
Discussion on the Dispersion of Ultramarine Blue in Universal Masterbatches
Universal masterbatches commonly use PE, PP, ABS, and other plastics as carriers.
The pigment content ranges from 10% to 40%. Universal masterbatches are mainly used in toys, household goods, and logistics packaging. Masterbatches are used for coloring plastic products, so two key properties are required: good dispersion and flowability. The product must not show defects such as color spots, flow marks, or weld lines due to the addition of masterbatch. Additionally, the masterbatch should not affect the product’s performance.
Initial wetting is the determining factor for the dispersion quality of ultramarine blue
The quality of ultramarine blue dispersion is determined by the initial wetting process
Initial wetting refers to the penetration of the wetting agent into small gaps in the ultramarine blue pigment agglomerates. This significantly reduces the aggregation force between pigment particles. The choice, speed, and time of the initial wetting agent are important.
In common universal masterbatches, low molecular weight wax is often used as the initial wetting agent. We recommend using polyethylene wax with a narrow molecular weight distribution and an acid value below 10.
Wetting is achieved through pre-dispersion, typically using a high-speed kneader, which is convenient and simple.
The amount of wetting agent depends on the pigment content in the masterbatch.
Generally, the higher the temperature during kneading, the greater the viscosity of the wetting agent and the better the dispersion. However, the final temperature in the kneader should not exceed 110°C (the melting point of polyethylene wax is between 90-105°C) to avoid lumping.
The kneading time depends on the kneader’s capacity, but it should not be less than 8 minutes.
The kneader speed should be set between 0.6 and 0.75 of the maximum speed.
Initial wetting agents are not limited to lubricants; dispersants and other additives can be included in the formula.
It is not recommended to add diffusion oils, as some on the market, such as silicone oil, have strong penetration and may cause color migration.
High-speed mixing of the wetting agent with the carrier
After pre-dispersion, the wetting agent and carrier should be uniformly mixed. It is recommended to use a high-speed kneader for mixing.
The choice of carrier depends on the type of plastic used in the final product and the amount to be added. Powders and pellets of PP, PE, ABS, EVA, etc., can be used.
The selection of carrier MI (Melt Index) is determined by the size of the final plastic parts. Choosing a carrier with a higher MI increases flowability, but it reduces the shear effect in the screw, which can lead to worse dispersion.
Screw extrusion granulation stabilizes the pigment dispersion effect
After the materials are kneaded in the formula, extrusion begins. It is best to use a twin-screw extruder with a slightly larger length-to-diameter ratio. This process is relatively simple, and the extrudate should have a smooth surface, without indentations, and uniform color. In this way, the ultramarine blue pigment is stabilized in the masterbatch and will not agglomerate again.
Here, we focus on initial wetting because it is the key, but in practice, it is often not controlled as a key process.
Comparison of Ultramarine Blue and Phthalocyanine Blue Pigments
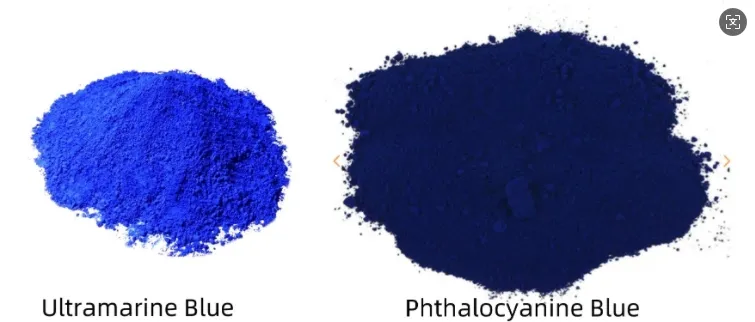
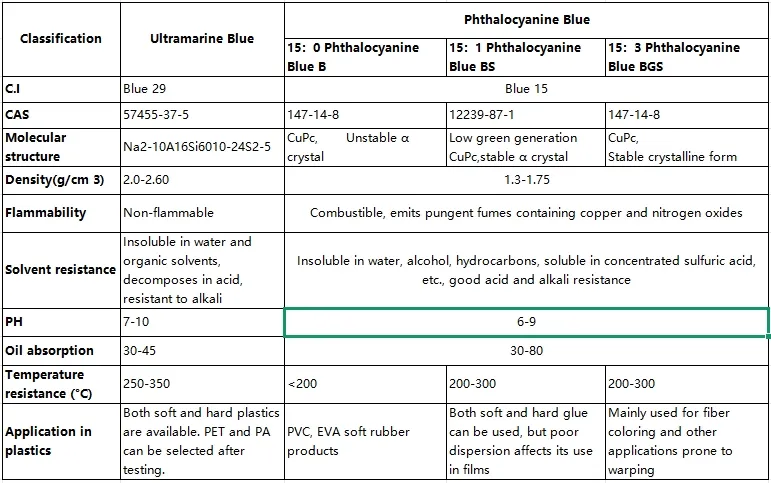

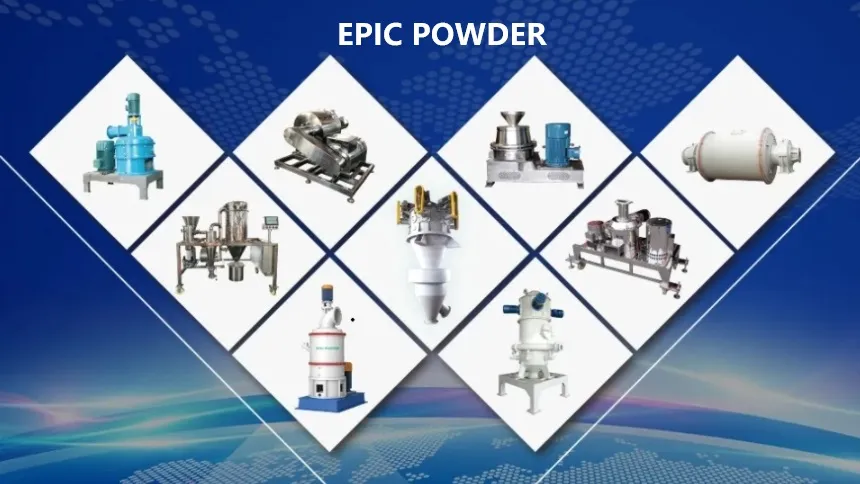