Carbon black is an amorphous black powder composed of carbon. It is mainly produced by incomplete combustion or thermal cracking of organic matter (such as natural gas, heavy oil, coal tar, etc.) under insufficient air conditions. Its particles are extremely fine, and the particle size is usually between 5 nanometers and 500 nanometers. It has a large specific surface area (10-3000 m²/g) and a unique chain or grape-like aggregate structure. Carbon black is widely used in rubber, plastics, inks, coatings and other industrial fields because of its high carbons content (more than 95%) and a small amount of oxygen, hydrogen, sulfur and other elements.
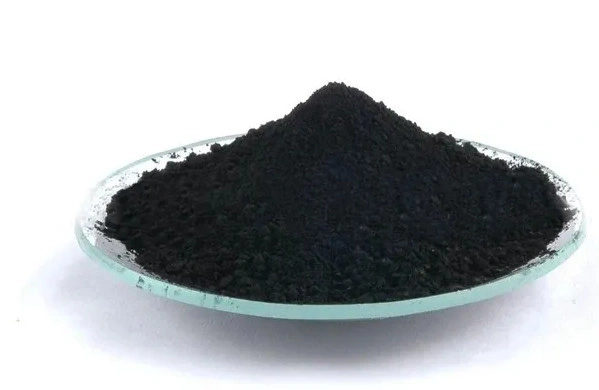
Basic properties of carbon black
The main properties of carbon blacks are particle size, structure and surface properties. They have an important influence on the processing properties and reinforcement effect of rubber.
Particle size
Carbon blacks particle size refers to the size of primary particles. The average particle size of carbon blacks for rubber is usually between 11 and 500 nanometers. The smaller the particle size, the larger the specific surface area, the larger the contact area between carbon black and rubber, and the more active points. Thereby enhancing its chemical bonding and physical adsorption capacity and improving the reinforcement effect. The particle size is affected by the manufacturing process. For example, in the oil furnace method, the higher the atomization degree, the higher the furnace temperature, the larger the air-oil ratio, and the faster the air flow speed, the smaller the carbon blacks particles.
Structurality
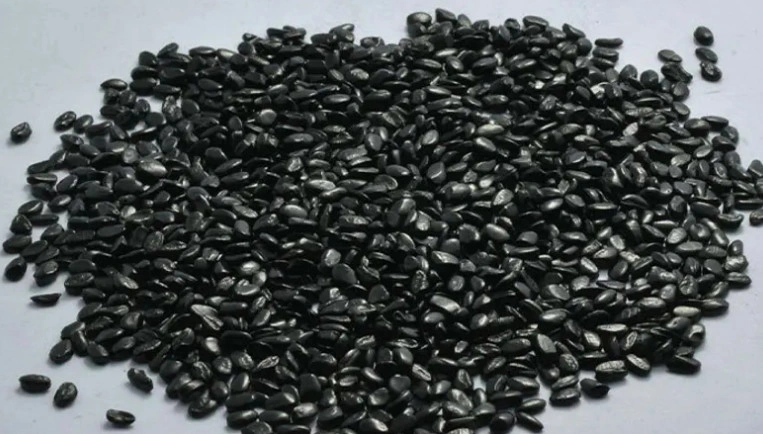
The structurality of carbon black refers to the complexity of the primary structure, that is, the spatial aggregate formed by chemical bonds between primary particles. The primary structure is stable and is the smallest dispersed unit in rubber. Multiple primary structures are further aggregated to form secondary structures through van der Waals forces, but are easily destroyed by shear forces during processing. The more complex the structure, the more branches, and the larger the internal voids, the stronger its absorption and retention effect on rubber and the better the reinforcement performance.
surface properties
The surface properties of carbon black include surface roughness and chemical properties. Nanoscale micropores often exist on the surface of particles, which will reduce the effective contact area and affect the reinforcement effect. Generally speaking, the surface of channel carbon black is the roughest, while the surface of furnace and thermal cracking carbon black is smoother. The roughness can be measured by electron microscopy or nitrogen adsorption.
The surface chemical properties of carbon black mainly come from its oxygen-containing functional groups (such as carboxyl, hydroxyl, phenolic, quinone, lactone) and free radicals. These structures give it a certain chemical activity and enhance its bonding ability with rubber. The stronger the chemical activity, the more obvious the reinforcement effect of carbon blacks. The elemental composition of carbon black is mainly carbon (90%-99%), containing a small amount of oxygen, hydrogen, sulfur and ash, and has aromatic structural characteristics.
Five characteristics of carbon black
Reinforcement effect: It can improve the tensile strength, wear resistance and aging resistance of rubber. Carbon black accounts for 20%-70% in tires;
Coloring performance: It has high blackness and strong weather resistance. It is the core black pigment of ink and coating;
Ultraviolet shielding: It absorbs ultraviolet radiation and is used in plastics and coatings to extend product life;
Conductivity and thermal conductivity: The conductivity of acetylene carbon black is close to that of graphite. The thermal conductivity of rubber containing carbon black is significantly improved;
Environmental adsorption: The high specific surface area enables it to play an adsorption role in waste gas purification and water treatment
Diversified application areas of carbon black
- Rubber industry (core application)
Tire manufacturing: improve wear resistance, reduce rolling resistance, high-performance tires have higher carbon blacks content.
Sealing materials: enhance high temperature resistance and anti-aging performance, used in aerospace and mechanical fields. - Plastics and coatings
Plastic modification: coloring, antistatic, UV protection, often added in the form of masterbatch.
Coating enhancement: improve blackness, chemical corrosion resistance and adhesion.
- Ink and electronics
Printing ink: pigment carbon black determines ink blackness and printing quality.
Electronic products: used for screen anti-reflection layer and battery conductive agent.
- Environmental protection and energy
Adsorbent: treat organic waste gas and heavy metal wastewater.
Battery technology: as an electrode conductive material to improve cycle life.
- Special fields
Silicone products: enhance fiber tensile strength and sealing material durability.
Military and aerospace: sealing and conductive components resistant to extreme environments
conclusion
Carbon blacks play a vital role in various industries due to its excellent reinforcing, coloring, and conductive properties. Its particle size, structure, and surface characteristics directly impact product performance, making it an essential additive in rubber, plastics, coatings, and beyond.
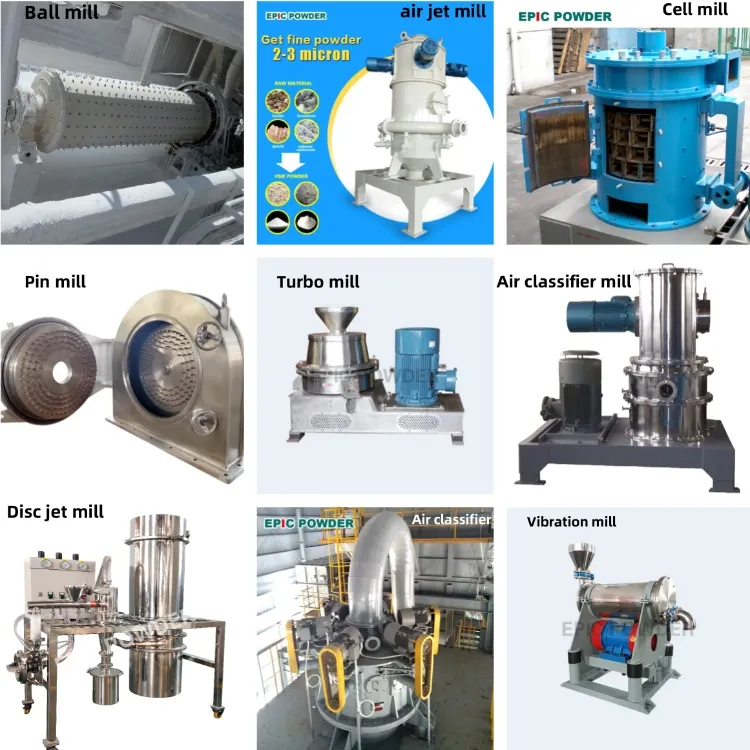
Epic Powder
Epic Powder, 20+ years of work experience in the ultrafine powder industry. Actively promote the future development of ultra-fine powder, focusing on crushing, grinding, classifying and modification process of ultra-fine powder. Contact us for a free consultation and customized solutions! Our expert team is dedicated to providing high-quality products and services to maximize the value of your powder processing. Epic Powder—Your Trusted Powder Processing Expert !