Currently, many materials can be used for lithium-ion battery anodes. However, only graphite materials have achieved mass production and commercialization.
Graphite anode materials include natural and artificial graphite. Key technical indicators include particle size, surface area, and density.
Other factors include capacity, efficiency, cycling, rate performance, and expansion. These indicators are interconnected, forming a tightly linked system.
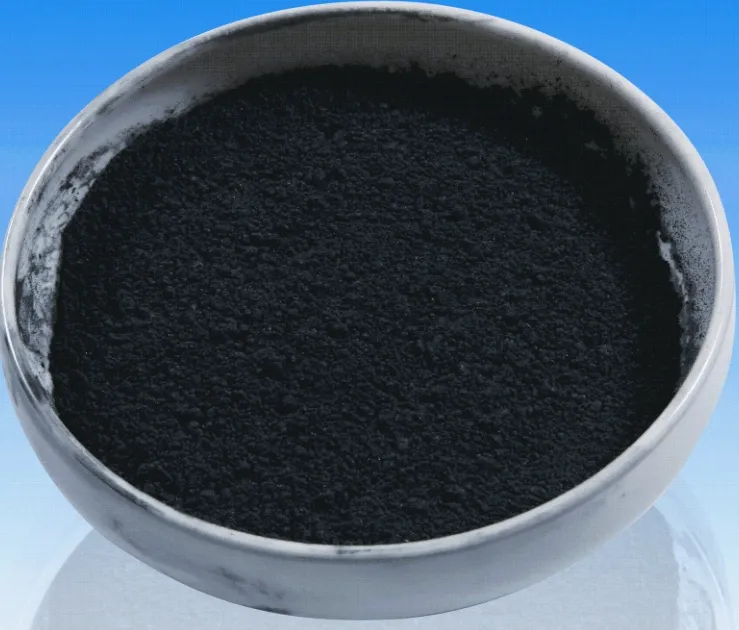
Particle size distribution
Currently, many materials can be used for lithium-ion battery anodes. However, only graphite materials have achieved mass production and commercialization. Graphite anode materials include natural and artificial graphite. Key technical indicators include particle size, surface area, and density. Other factors include capacity, efficiency, cycling, rate performance, and expansion. These indicators are interconnected, forming a tightly linked system.
The particle size of graphite anode materials affects their electrochemical performance. Particle size directly impacts tap density and specific surface area. Tap density influences the volumetric energy density of the material.
With the same volume filling, larger particle size and wider distribution reduce slurry viscosity. Lower viscosity improves solid content and eases coating. A wider particle size distribution allows small particles to fill gaps between large ones. This increases electrode compaction density and enhances volumetric energy density. The width of particle size distribution is judged by (D90-D10)/D50. A higher value indicates a wider distribution; a lower value indicates a narrower one. Smaller particles improve rate performance and cycle life but reduce initial efficiency and compaction density, and vice versa.
The particle size of anode materials is mainly determined by the preparation method. GB/T 24533-2019 defines graphite anode material grades. The table below shows the particle size distribution range for different graphite anode materials.
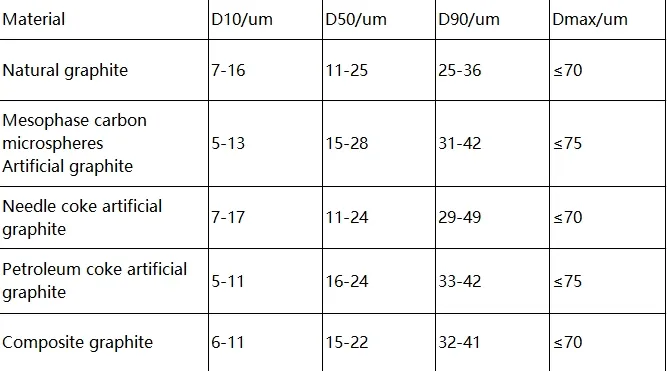
Specific surface area
The specific surface area is the total area per unit mass of material. Smaller particles with higher surface area provide more lithium-ion pathways, improving rate performance. However, larger contact areas with the electrolyte increase SEI formation, reducing first-cycle efficiency. Larger particles have higher compaction density. For graphite anode materials, a specific surface area below 3 m²/g is ideal.
Tap density
Tap density is the mass per unit volume of powder after vibration-induced compaction. It is a key indicator of active materials. Since lithium-ion battery volume is limited, higher tap density means more active material per unit volume. This leads to higher volumetric capacity.
Compacted density
The compact density refers to the density of the electrode after roll pressing, made of active materials and binders.
Compact density = areal density / (thickness of the electrode after rolling – copper foil thickness).
Compact density is closely related to the specific capacity, efficiency, internal resistance, and cycling performance of the battery. The higher the compact density, the more active material per unit volume, resulting in higher capacity. However, increasing compact density reduces porosity, leading to poorer electrolyte absorption, lower wettability, and increased internal resistance. This makes lithium-ion insertion and extraction more difficult, which can hinder capacity improvement.
Factors affecting compact density: particle size, distribution, and morphology.
True density
True density refers to the weight of solid material per unit volume in an absolutely dense state (excluding internal voids). Since true density is measured in a compacted state, it will be higher than bulk density.
Typically, true density > compact density > bulk density. The following diagram outlines the density requirements for graphite anode materials in standards.
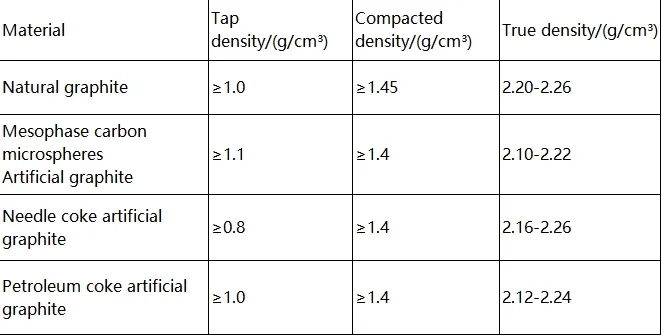
First charge and discharge specific capacity
During the first charge of a lithium-ion battery, the graphite anode material’s surface gradually lowers in potential as lithium ions embed. When the voltage drops to around 0.8V, solvent molecules in the electrolyte are reduced on the anode surface. This produces a large amount of organic or inorganic products, which deposit on the anode surface, forming a dense passivation film, the SEI film.
The reaction stops only when the anode surface is fully covered by the SEI film, preventing solvent molecules from embedding. Forming the SEI film consumes some lithium ions, which cannot be released during discharge. This reduces the first discharge capacity. In the second charge-discharge cycle, the 0.8V voltage plateau disappears. The half-cell cycle test of the graphite anode material is shown in the figure below.
First coulombic efficiency
An important indicator of the performance of an anode material is its first charge-discharge efficiency, also known as the first Coulombic efficiency. During charging and discharging, some lithium ions extracted from the cathode and embedded in the anode cannot return to the cathode to participate in the charge-discharge cycle, leading to a first Coulombic efficiency of less than 100%.
The reasons for these lithium ions not returning to the cathode are:
- Some irreversible lithium embedding.
- The formation of an SEI film on the anode surface, which is a key factor affecting Coulombic efficiency.
Since the SEI film mostly forms on the surface of the electrode material, the specific surface area of the electrode material directly affects the formation area of the SEI film. The larger the specific surface area, the greater the contact area with the electrolyte, leading to a larger SEI film formation area. It is generally believed that forming a stable SEI film benefits the charge-discharge process, while an unstable SEI film is detrimental to the reaction.
It continuously consumes the electrolyte, thickens the SEI film, and increases the internal resistance.
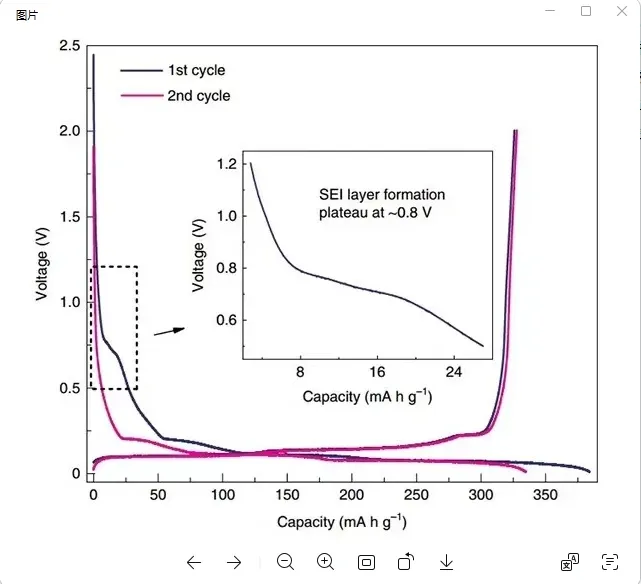
Cycle performance
Battery cycling performance refers to the number of charge-discharge cycles a battery undergoes until its capacity drops to a specified value under a certain charge-discharge protocol. Regarding cycling performance, the SEI film will hinder the diffusion of lithium ions. As the number of cycles increases, the SEI film continuously sheds, peels, and deposits on the anode surface, causing the internal resistance of the anode to gradually increase, leading to heat accumulation and capacity loss.
Rate performance
The diffusion of lithium ions in graphite anode materials is highly directional, meaning it can only insert perpendicular to the C-axis of the graphite crystal. The insertion process is shown in the diagram below. Small particles and high surface area anode materials have better rate performance. Additionally, the surface resistance of the electrode (due to the SEI film) and the electrode conductivity also affect the rate performance. Similar to cycle life and expansion, isotropic anodes have more lithium-ion transport channels, solving the problem of fewer entry points and slower diffusion rates in anisotropic structures, which is beneficial for high-current charge and discharge.
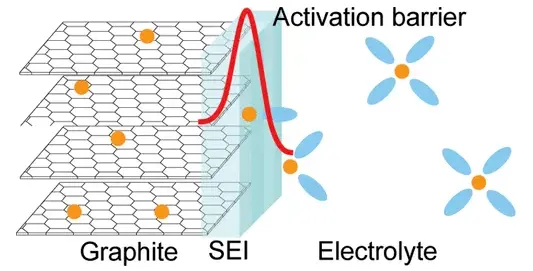
Expansion performance
Expansion and cycle life are positively correlated. After the anode expands:
It causes deformation of the core, leading to microcracks in the anode particles. The SEI film breaks and reorganizes, consuming electrolyte and degrading cycle performance.
It puts pressure on the separator, especially at the sharp edges of the electrode tabs, which can lead to micro-short circuits or micro lithium metal precipitation as charge and discharge cycles progress.
Regarding expansion itself, during the lithiation of graphite, lithium ions insert into the interlayer spacing of graphite, causing the interlayer to expand and the volume to increase. This expansion is partially irreversible. The degree of expansion is related to the anode’s orientation, which can be calculated using XRD data by the formula: Orientation = I004/I110. Anisotropic graphite materials tend to undergo lattice expansion in the same direction (the C-axis direction of the graphite crystal) during lithiation, which results in significant volume expansion of the battery.
Conclusion
By using superfine grinding, the particle size of the anode material is controlled. This optimizes the specific surface area and pore structure. It improves the tapping/packing density, providing core material solutions for high-energy-density lithium batteries.These materials offer high conductivity and structural stability.
Epic Powder, 20+ years of work experience in the ultrafine powder industry. Actively promote the future development of ultra-fine powder, focusing on crushing,grinding,classifying and modification process of ultra-fine powder. There are various kinds of mills, such as air jet mill, Air Classifying Mill, pin mill and ball mill etc. Contact us for a free consultation and customized solutions! Our expert team is dedicated to providing high-quality products and services to maximize the value of your powder processing. Epic Powder—Your Trusted Powder Processing Expert!
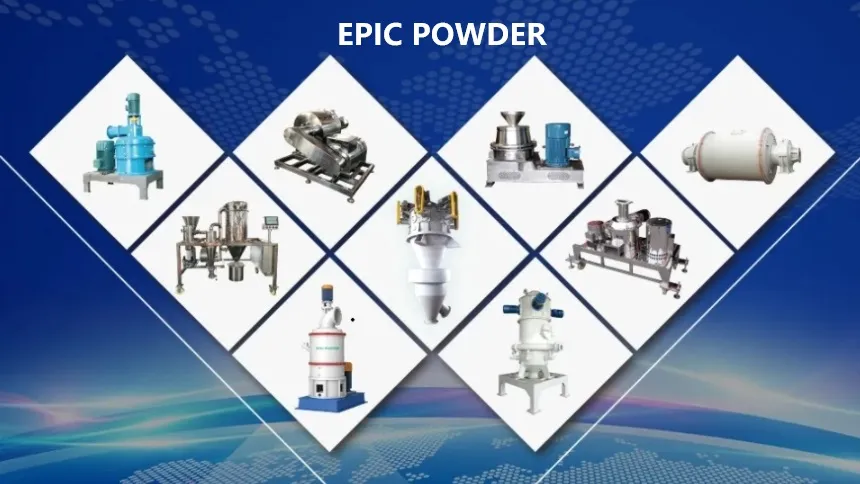