The impact of screening technology on powder production efficiency is mainly reflected in the following aspects:
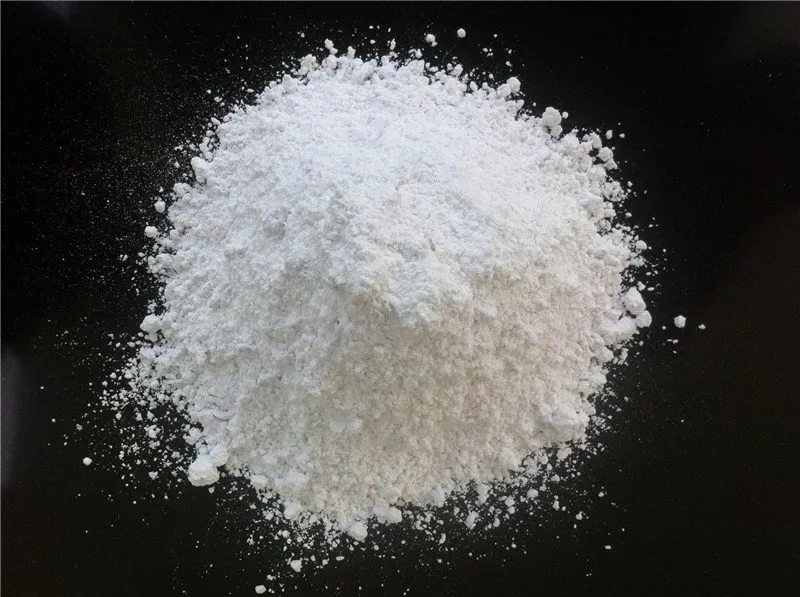
Optimization of sorting accuracy and efficiency
- Parameter matching: Through CAE simulation (e.g., EDEM), optimize screen aperture, vibration frequency, and amplitude to improve efficiency.
For example, adjusting vibration frequency reduces particle blockage, increasing screening efficiency by 15%-30%. - Air classification optimization: In food and pharmaceutical industries, optimizing cyclone separator nozzle angle or airflow speed improves accuracy. This reduces fine powder loss by 10%, lowers rework rate, and indirectly shortens production cycle.
Equipment performance and stability
- Anti-blockage design: Optimizing the screen structure (e.g., using a wavy screen surface) reduces material blockage. This extends continuous operating time by 20%-50%.
For example, in the coal industry, the desliming screen improves throughput by 18% through rearranging the screen hole pattern. - Improved wear resistance: By simulating screen wear (e.g., in the metallurgical industry for iron ore screening), using high-strength alloy materials can extend the screen’s lifespan by more than three times. This reduces downtime and the frequency of replacements.
Process Integration and Energy Control
- Multifunctional integration: Screening equipment simultaneously performs dewatering and desliming. This is beneficial in the building materials industry. It is particularly useful for sand and gravel aggregate production.This simplifies the process flow and saves 30% of operation time.
- Energy-efficient design: The vibrating screen uses a variable frequency motor to adjust the amplitude.This reduces energy consumption by 25%. The processing capacity remains the same.
Intelligence and Automation
- Real-time monitoring: Sensors monitor the screening status (e.g., screen damage, abnormal feeding). Timely alerts can reduce equipment downtime by 30%.
- Adaptive adjustment: The intelligent control system automatically adjusts vibration parameters based on material characteristics (e.g., agglomeration of ultrafine powder in the chemical industry). This reduces the efficiency fluctuation range from ±15% to ±5%.
conclusion
In summary, screening technology impacts processing speed, energy consumption, and equipment stability in powder production. This is achieved through precise parameter control, equipment performance improvements, and intelligent upgrades. It has become a core technological method for improving industry production efficiency.
EPIC Powder Equipment Supplier
20+ years of work experience in the ultrafine powder industry.
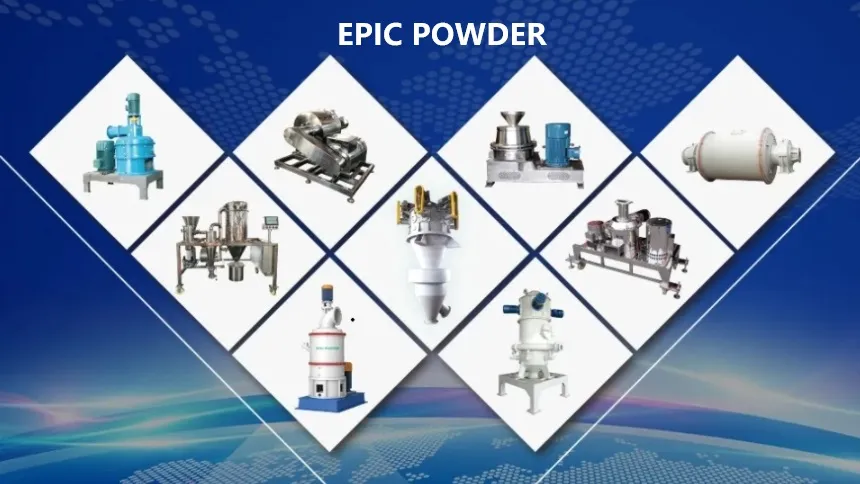