Compared with other lithium battery cathode materials, lithium iron phosphate has become a research hotspot in recent years due to its abundant raw material sources, low cost, high capacity, and good safety. The performance of LiFePO₄ cathode material depends to some extent on the material’s shape, particle size, and atomic arrangement. Therefore, the preparation process is particularly important.
There are four production process routes for lithium iron phosphate cathode material (LFP): hydrothermal method process route, ferrous oxalate process route, iron oxide process route, and ferric phosphate process route. Among them, the iron phosphate route has become the mainstream process for producing lithium iron phosphate due to its lower cost and better cost-performance ratio.
Iron phosphate
Iron phosphate, also known as ferric phosphates, has the chemical formula FePO4 and a molecular weight of 150.82. Its density is 3.2 g/cm³, and the melting point is approximately 600°C. The iron in iron phosphate is trivalent, mostly in the form of a dihydrate (FePO4·2H2O). It naturally occurs as the mineral vivianite. Iron phosphate is a white or pale yellow powder with high chemical and thermal stability. It is widely used in batteries, ceramics, and catalysts.
Schematic diagram of the structural formula of iron phosphates and lithium iron phosphates.
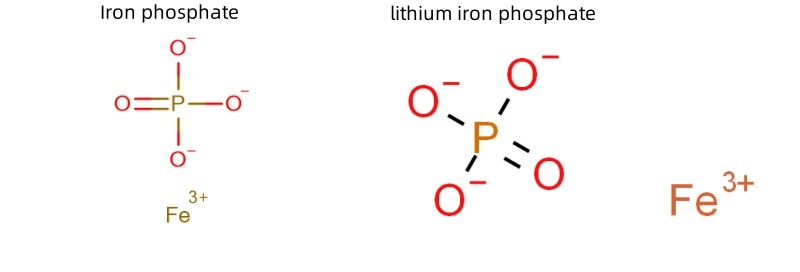
Since iron phosphate has a similar chemical structure to lithium iron phosphate, FePO4 is used as a precursor. It participates in the preparation of lithium iron phosphate for lithium battery cathodes. The chemical composition, structure, morphology, and particle size of iron phosphate precursors largely determine the performance of lithium iron phosphate cathodes. Therefore, the preparation process of high-quality iron phosphate is crucial.
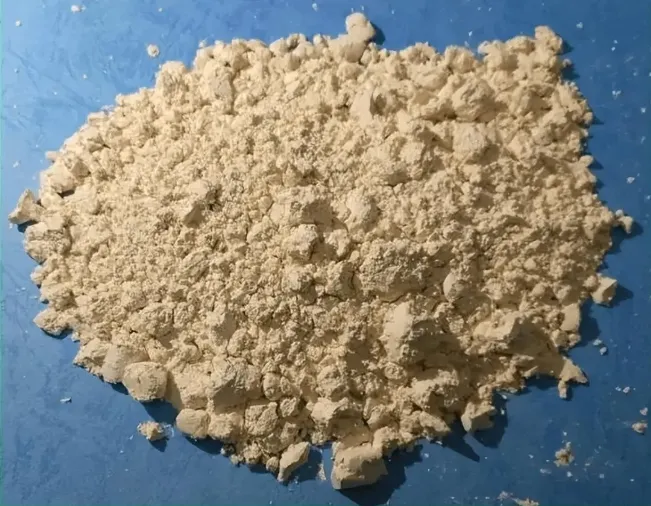
Preparation process of iron phosphate
The main synthesis methods of iron phosphates include precipitation, hydrothermal, sol-gel, air oxidation, and controlled crystallization. Among them, the precipitation method has advantages such as low equipment requirements and lower costs. By controlling reaction conditions, ideal iron phosphate for batteries can be obtained. It is easy to scale up for industrial production, making precipitation the main method for producing battery-grade iron phosphate.
There are two main methods for industrial production of iron phosphates:
(1) Using purified phosphoric acid (via thermal or wet methods) to react with ferrous sulfate to produce iron phosphates.
(2) Reacting phosphates with ferrous sulfate to produce iron phosphate.
Common phosphates include monoammonium phosphate (MAP) and diammonium phosphate (DAP), with monoammonium phosphate being the mainstream.
These methods are categorized as the “iron block + phosphoric acid + ferrous sulfate + monoammonium phosphate” process.
In addition, the iron sulfate route for preparing iron phosphates requires ammonia water or sodium hydroxide to adjust the pH. Depending on the pH adjuster used, it can be classified into the sodium method and ammonium method.
The ammonium method refers to reacting ferrous sulfate solution with monoammonium phosphate, followed by precipitation and filtration. Excess acid is neutralized with ammonia water to obtain iron phosphates. The sodium method involves acidifying ferrous sulfate with phosphoric acid, reacting it with hydrogen peroxide. Iron dihydrogen phosphate is then formed, and the pH is adjusted with sodium hydroxide to produce iron phosphate.
Process flow of ammonium ferric phosphate
Preparation of monoammonium phosphate solution
Monoammonium phosphate and pure water are added to a dissolution tank to dissolve into a solution with 7% phosphorus content. During the dissolution process, 20% ammonia water is added to adjust the pH, keeping it between 3 and 5. The solution is then passed through a precision filter, and the filtrate is pumped into a storage tank for later use. The entire process is carried out in a closed transport system. The salt-containing wastewater from washing the filter residue is sent to the plant’s wastewater treatment station for processing.
Ferrous iron dissolution and impurity removal process
Ferrous sulfate is manually added to the dissolution tank along with pure water for dissolution, while steam is introduced for direct heating. The temperature is maintained between 40–50°C. The dissolved solution is pumped into a decontamination barrel, where iron powder is added to remove the trivalent iron ions formed by oxidation. To ensure that ferrous sulfate does not undergo oxidation, an excess amount of iron powder is added during this process.
During the raw material dissolution process, ferrous sulfate dissolution residues are produced, mainly consisting of titanium, aluminum, manganese, and other metal compounds.
The impurity-containing ferrous solution is filtered through a plate-and-frame filter press. The filtrate (containing 20% ferrous sulfate) is then transferred to a clarification tank for further purification and clarification, ready for use.
Oxidation synthesis process
First, the prepared 7% monoammonium phosphate solution (calculated by P content) is stored in a tank.
27.5% hydrogen peroxide and pure water are pumped into the high-level tank to prepare the phosphate solution.
Next, the refined 20% ferrous sulfate solution is transferred from the tank area to the oxidation synthesis reactor.
Pure water is added to prepare a 12% ferrous sulfate solution. The phosphate solution in the high-level tank is added to the oxidation synthesis reactor via a metering tank. The reaction occurs at room temperature and pressure with stirring, and the pH is controlled between 2~3.
Primary filter press washing process
After the reaction, the generated tetrahydrate iron phosphate slurry enters the plate-and-frame filter press for primary filtration. The filtrate produced from the filtration process enters the synthetic mother liquor tank. The filtered tetrahydrate iron phosphate slurry is washed with pure water, and after washing, it is filtered again in the plate-and-frame filter press. The resulting filter cake (containing about 70% water) is the tetrahydrate iron phosphate, and the synthetic wash water enters the synthetic wash water tank. The filter cake moves on to the next process. The synthetic mother liquor and synthetic wash water are treated at the plant’s wastewater treatment station and then reused.
Secondary filter press washing process
The converted dihydrate iron phosphate slurry is pumped into the plate-and-frame filter press for filtration. The filtrate produced during filtration enters the mother liquor tank. The dihydrate iron phosphate filter cake is washed with pure water, then filtered again in the plate-and-frame filter press. The secondary wash water generated during filtration enters the conversion wash water tank. The resulting filter cake (containing about 60% water) enters the flash drying process. The filtrate and secondary wash water are treated at the plant’s wastewater treatment station and then reused.
Drying and pulverizing process
The ambient air is filtered by an air filter before entering the blower. It then passes through a preheater and is heated to 140°C (heated by the rotary kiln jacket and drying exhaust gas). Next, the air is heated with natural gas to 500°C and enters the drying chamber through the inlet of the rotary flash dryer. The wet dihydrate iron phosphate filter cake, separated from the solid-liquid mixture, is evenly fed into the rotary flash dryer by a feed screw. Under the combined effect of the stirrer and hot air, the wet material is quickly dispersed and dried.
The dried material is crushed by a mill to obtain iron phosphate products. The iron phosphate product is then conveyed through a pipeline to a bulk bag packaging machine for packaging. After packaging, the product is stored in the finished goods warehouse, awaiting entry into the lithium iron phosphate production line. The dust generated during crushing and packaging is collected and directed to the rotary kiln bag filter for treatment. It is then drawn by the exhaust fan to the flash drying stage, where it undergoes water film dust removal and is released through the exhaust pipe.
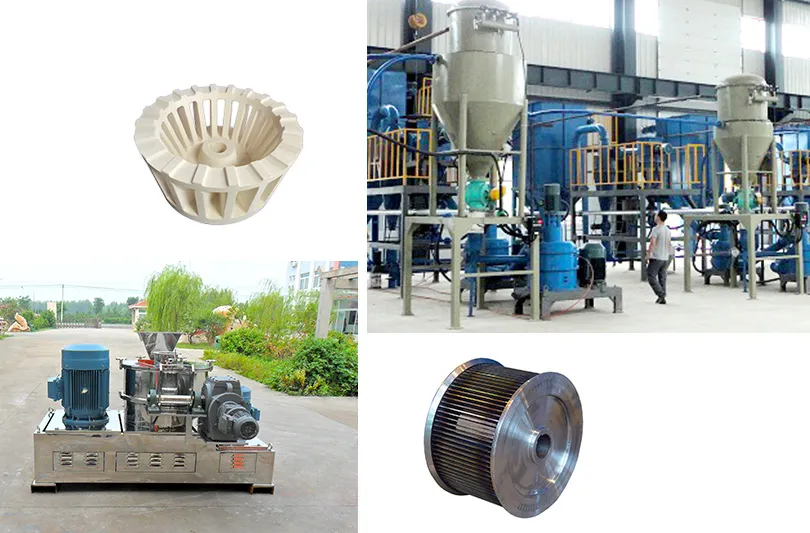
Mother liquor washing water treatment
The synthetic mother liquor is filtered and undergoes high-pressure reverse osmosis. The fresh water is combined with the conversion wash water, while the concentrated water is mechanically evaporated to produce ammonium sulfate and monoammonium phosphate as by-products.
The synthetic wash water is filtered and undergoes reverse osmosis. The fresh water is combined with the synthetic wash water for treatment and reuse. The concentrated water is combined with the synthetic mother liquor for treatment. One-third of the aged mother liquor returns to the phosphoric acid-ammonium mixing section for reuse of phosphoric acid. Two-thirds of the aged mother liquor and conversion wash water are filtered and undergo secondary reverse osmosis, with the fresh water used as wash water for reuse. The concentrated water is combined with the conversion mother liquor for treatment.
epic powder
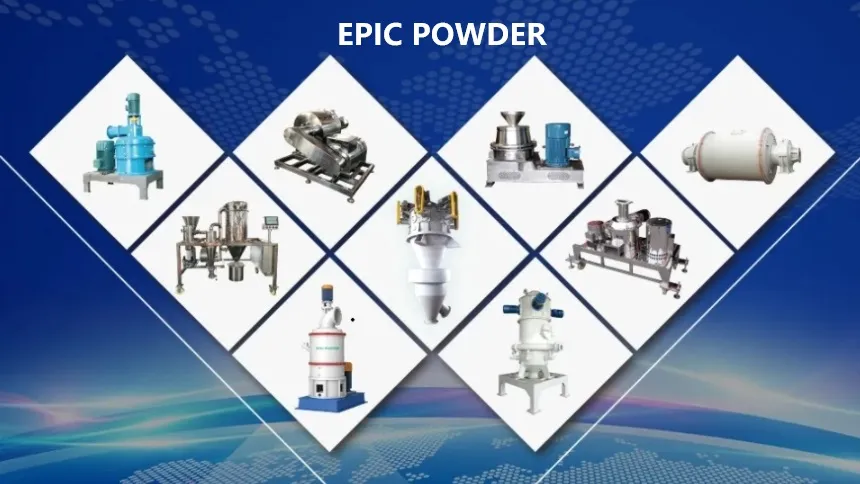
Epic Powder, 20+ years of work experience in the ultrafine powder industry. Actively promote the future development of ultra-fine powder, focusing on crushing,grinding,classifying and modification process of ultra-fine powder. Contact us for a free consultation and customized solutions! Our expert team is dedicated to providing high-quality products and services to maximize the value of your powder processing. Epic Powder—Your Trusted Powder Processing Expert !