In the new energy battery field, lithium iron phosphate batteries are the focus due to their high safety, long cycle life, and environmental benefits. In the preparation and processing of lithium iron phosphate materials, the jet mill plays an irreplaceable role. It is crucial for improving material performance and meeting the growing demands of the battery industry.
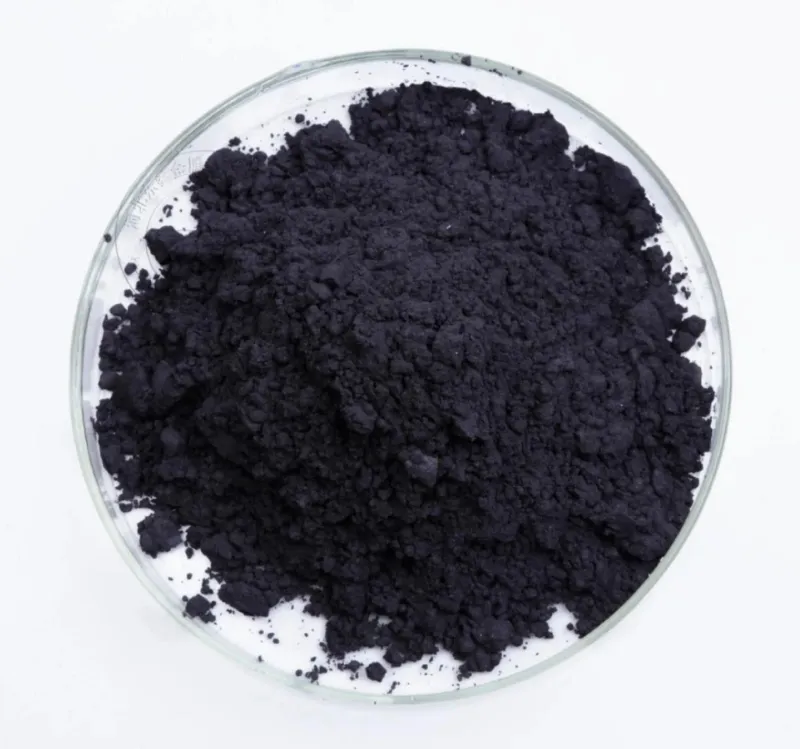
Characteristics and Current Applications of Lithium Iron Phosphate Materials
Lithium iron phosphate (LiFePO₄) is a compound with an olivine structure and stable crystal structure. Its theoretical capacity reaches 170 mAh/g, with a working voltage platform around 3.2V. During charge and discharge, Li⁺ can reversibly insert and extract from the lattice with minimal structural changes. This provides lithium iron phosphate batteries with excellent cycle stability. Additionally, lithium iron phosphate contains no rare or expensive metals like cobalt or nickel, with abundant raw material sources and relatively low cost. It also offers good thermal stability and safety, making it less prone to thermal runaway in high-temperature environments, significantly reducing the risk of battery fires and explosions.
Based on these advantages, lithium iron phosphate batteries are widely used in the new energy vehicle sector. Many automakers use them as a power source, driving the popularity of electric vehicles. In the energy storage field, whether for large-scale energy storage stations on the grid side or home-based distributed storage systems, lithium iron phosphate batteries efficiently store and flexibly manage electricity. This helps alleviate the peak-to-valley electricity difference and improve energy utilization efficiency.
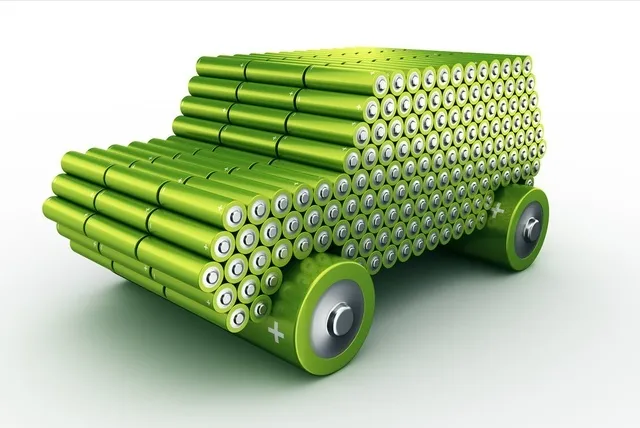
Working Principle of the Jet Mill
After the compressed air is filtered and dried, it is sprayed into the grinding chamber at high speed through the Laval nozzle. At the intersection of multiple high-pressure airflows, the materials are repeatedly collided, rubbed, and sheared to be crushed. The crushed materials rise with the suction of the fan. The airflow moves to the classification zone. Under the action of the strong centrifugal force generated by the high-speed rotating classification turbine, the coarse and fine materials are separated. The fine particles that meet the particle size requirements enter the cyclone separator and dust collector through the classification wheel for collection. And the coarse particles descend to the crushing zone and continue to be crushed.
Advantages of the Jet Mill
Compared to traditional mechanical grinding methods, the air classifier mill shows many significant advantages when processing lithium iron phosphate materials. First, the air classifier mill achieves ultra-fine grinding, processing lithium iron phosphate to micron or even nano-level particle sizes. This greatly increases the material’s specific surface area. For example, the specific surface area of lithium iron phosphate powders processed by jet mill can be increased to tens of square meters per gram. This enhances battery charge/discharge efficiency. Lithium-ion diffusion paths in electrode materials are shortened. Rate performance improves, enabling faster charging and discharging.
Second, the air classifier mill introduces almost no impurities during grinding. Its working principle mainly relies on the interaction between the airflow and the material. The equipment’s internal components use wear-resistant and corrosion-resistant materials, such as ceramic linings. These materials prevent metal impurities from contaminating the lithium iron phosphate due to equipment wear. This design ensures high material purity, which is vital for battery long-term stability and cycle life. Impurities in the material may cause side reactions inside the battery, reducing performance, which the air classifier mill helps solve.
Moreover, the air classifier mill offers excellent control over particle size distribution. By precisely adjusting airflow speed, classifier rotor speed, and other parameters, the particle size distribution range can be accurately controlled. In battery production, uniform particle size distribution ensures the consistency of electrode materials during slurry preparation, coating, and other subsequent processes. This improves battery consistency and stability, reducing performance losses caused by individual differences in the battery pack.
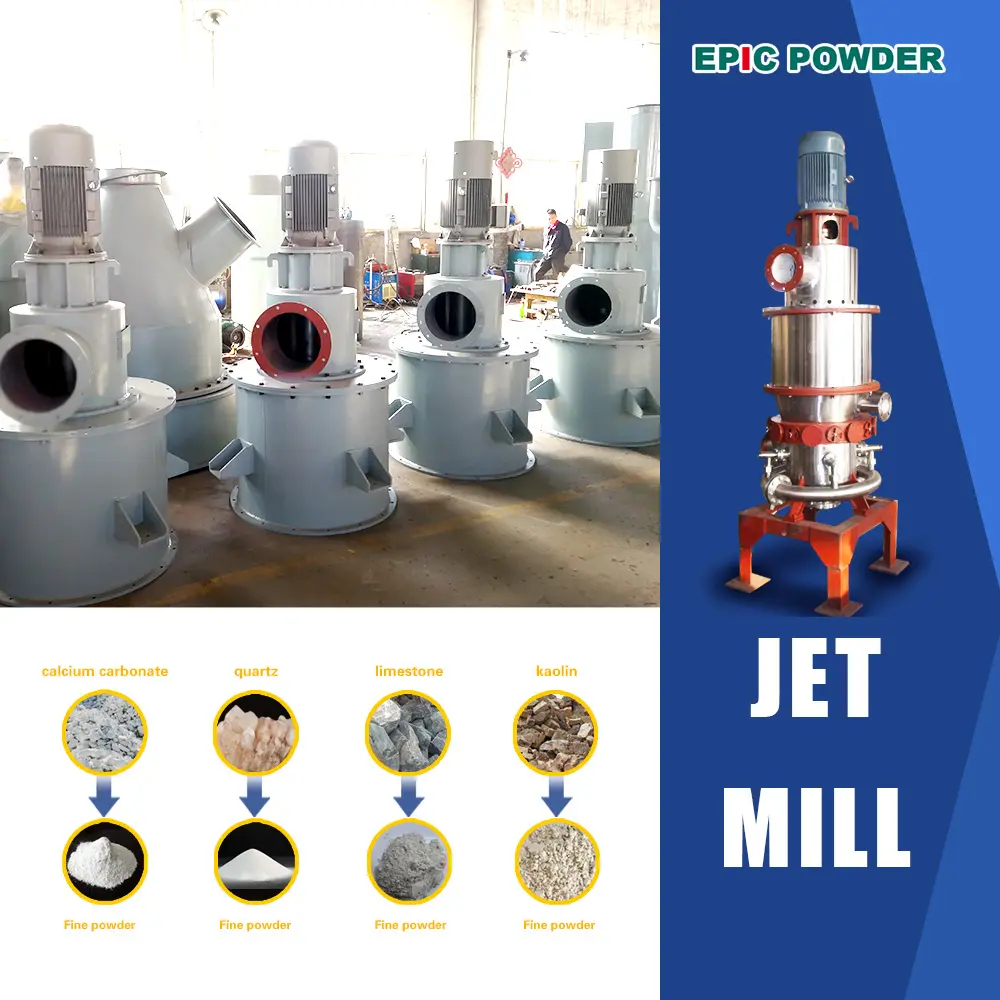
jet Mill Technology Development Trends: Creating a Closed-Loop Ecosystem for New Energy
With the continuous advancement of jet mill technology, it will play an increasingly important role in the new energy industry. By improving precision, energy efficiency, and environmental performance, air classifier mills can optimize battery material performance. They will also promote sustainable production processes, supporting the closed-loop ecosystem for green energy recycling. In the future, jet mills will integrate with intelligent control, customized solutions, and resource recovery technologies. Together, they will drive the green transformation and innovation in the new energy industry, contributing to the global energy structure optimization.