Silicon nitride ceramics have high hardness and mechanical strength. They are resistant to high temperatures and have excellent thermal stability. Their dielectric constant and dielectric loss are low. They are highly wear-resistant and corrosion-resistant. These properties make them excellent multifunctional ceramics. High-purity silicon powder is one of the main raw materials for producing silicon nitride ceramics. Its purity and particle size have a key impact on ceramic performance.
High purity reduces the negative effects of impurities. Proper particle size distribution improves reactivity and ceramic density.
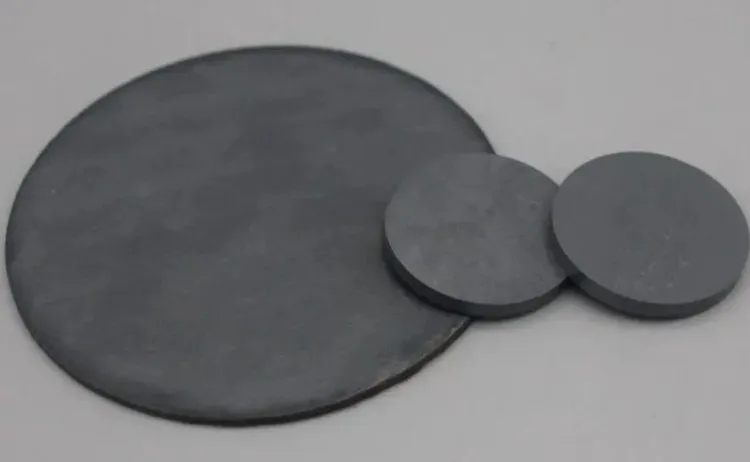
Preparation process
Silicon Powder Nitridation: In a nitrogen atmosphere, high-purity silicon powder is placed in a high-temperature furnace to react with nitrogen gas, forming silicon nitride. The reaction is: 3Si + 2N₂ = Si₃N₄.
Impurities like Fe, O, and Ca in the silicon powder are typically controlled below 2%. The reaction temperature is around 1400°C. At 1200–1300°C, more α-Si₃N₄ is formed, but the product tends to be coarse. Crushing and grinding are usually required to produce qualified ultrafine silicon nitride powder. To avoid contamination, silicon nitride ceramic parts can replace metal components in processing equipment.
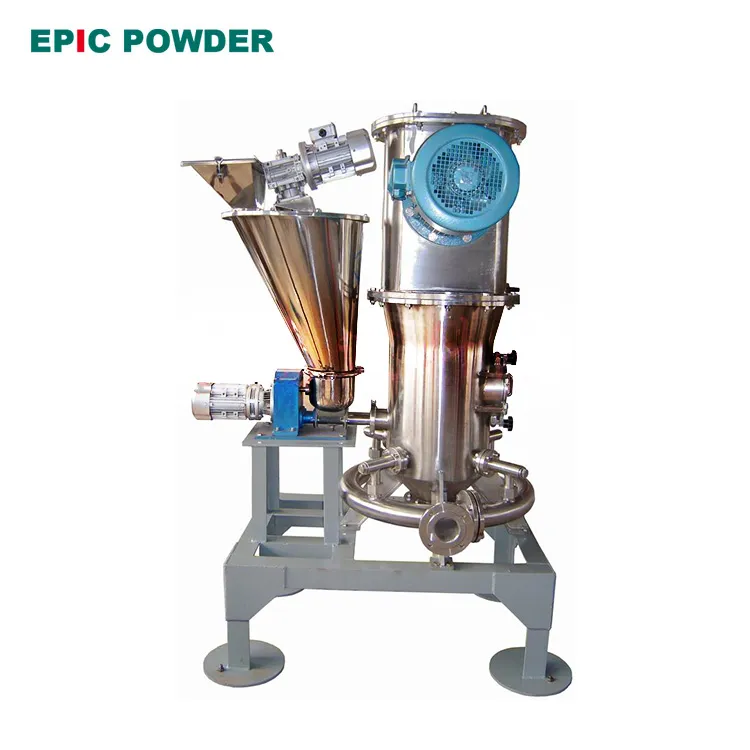
Forming: Silicon nitride ceramics can be formed by various methods, such as tape casting. First, a dispersant is added to the ceramic powder and milled to wet the particles and prevent agglomeration.
Then, binders and plasticizers are added and milled again to obtain a stable and uniform slurry. The slurry is then vacuum-defoamed to achieve proper viscosity. Filtering and aging improve slurry stability. Finally, the slurry is cast into flat green tapes using a tape caster and dried to form thick film green bodies.
Sintering: Silicon nitride ceramics are usually densified by liquid-phase sintering. Common methods include gas pressure sintering (GPS). In GPS, the green body is sintered under 5–12 MPa of nitrogen at 1800–2100°C. High nitrogen pressure prevents silicon nitride decomposition at high temperatures. It allows higher sintering temperatures and promotes densification. This also enables the use of sintering aids that form high-refractoriness grain boundary phases, improving high-temperature performance.
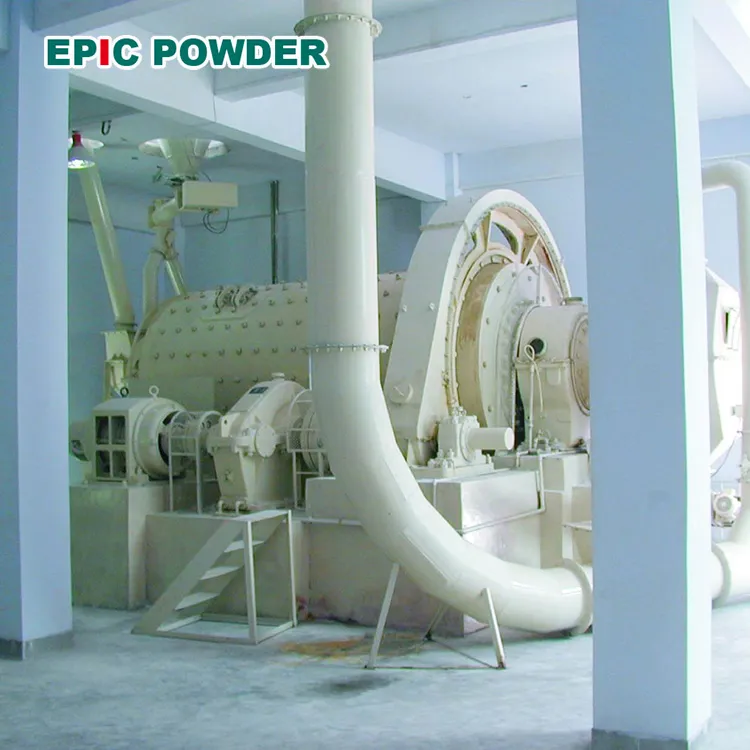
Performance characteristics of silicon carbide ceramics
Silicon carbide ceramics feature high hardness and excellent wear resistance. They offer high thermal conductivity and can withstand high temperatures and oxidation. With good chemical stability, they are widely used in high-temperature structural parts, wear-resistant materials, and heat exchangers.
The role of high purity silicon powder
A mixture of high-purity silicon powder and carbon powder is used as the raw material. Silicon provides the silicon source and reacts with carbon to form silicon carbide. The purity and particle size affect the phase composition, microstructure, and properties of the final SiC ceramics.
Preparation process
Raw Material Mixing: High-purity silicon powder and carbon powder are mixed in a specific ratio. Ball milling or similar methods are used to ensure uniform mixing. This promotes close contact between silicon and carbon powders, creating good conditions for the subsequent reaction.
Reaction Synthesis: The mixed raw materials are placed in a high-temperature furnace for reaction, typically at 1600–2000°C. At high temperatures, silicon reacts with carbon to form silicon carbide. Precise control of temperature and holding time is essential to ensure complete reaction and achieve the desired SiC phase composition and microstructure.
Forming and Sintering: The reacted silicon carbide is crushed and shaped using methods like dry pressing or isostatic pressing. High-temperature sintering follows, such as pressureless sintering or hot pressing. Sintering enhances the density and properties of SiC ceramics to meet application requirements.
conclusion
In conclusion, the use of high-purity silicon powder in the preparation of silicon nitride ceramics plays a crucial role in achieving superior material properties. The high purity minimizes the impact of impurities, while the controlled particle size distribution ensures better reactivity and densification during sintering. This leads to the production of high-performance silicon nitride ceramics with excellent mechanical strength, thermal stability, and wear resistance, making them suitable for a wide range of industrial applications.
Epic powder
Epic Powder, 20+ years of work experience in the ultrafine powder industry. Actively promote the future development of ultra-fine powder, focusing on crushing,grinding,classifying and modification process of ultra-fine powder. Contact us for a free consultation and customized solutions! Our expert team is dedicated to providing high-quality products and services to maximize the value of your powder processing. Epic Powder—Your Trusted Powder Processing Expert !