With the development of science and technology, the powder industry will become one of the most important material industries of the 21st century. Powder particle size, distribution, microscopic morphology, and purity are key indicators of powder materials. These factors also affect powder preparation and the process and performance of the final product. By optimizing the particle size of raw alumina ceramic powders, the aim is to prepare ceramic materials with excellent overall performance.
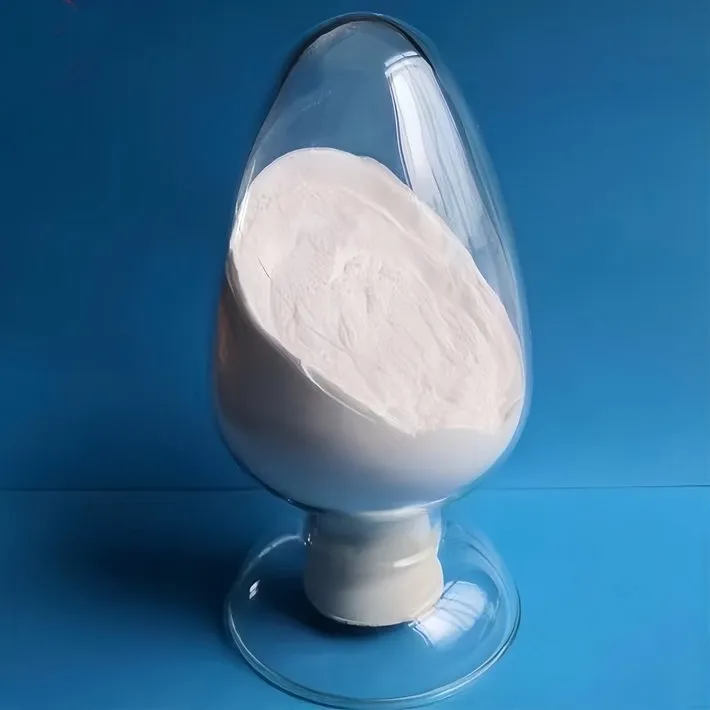
Properties of Alumina Ceramic Powders
High Hardness and Wear Resistance
Alumina is one of the hardest ceramic materials, with a Mohs hardness rating of 9. This property makes alumina ceramics highly resistant to wear and abrasion, making them ideal for use in harsh environments, such as grinding, cutting, and machining applications.
High Thermal Stability
Alumina ceramics have a high melting point (approximately 2050°C), which gives them excellent thermal stability. This makes alumina suitable for high-temperature applications, such as in furnace linings, kilns, and heat exchangers.
Chemical Resistance
Alumina is highly resistant to corrosion and chemical degradation. It does not react with most acids and alkalis, making it ideal for use in chemically aggressive environments, such as in the pharmaceutical, chemical, and petrochemical industries.
Electrical Insulation
Alumina is an excellent electrical insulator due to its high dielectric strength. It is widely used in electrical and electronic components, providing insulation in various devices.
Biocompatibility
Alumina is also biocompatible, which means it is not harmful to living tissue. This property has made it a popular material in medical implants, such as artificial joints and dental materials.
Manufacturing of Alumina Ceramic Powders
The production of alumina ceramic powders involves several processes. These include the extraction of aluminum from bauxite ore. After that, refining and calcining are done to obtain alumina powder. The purity and particle size of the alumina powder are critical factors. These factors affect the final properties of the ceramic material. The powder is typically produced by grinding raw materials in ball mills. Sieving is then done to ensure uniform particle size distribution.
The properties of the powder can be tailored by adjusting processing parameters. These parameters include calcination temperature, particle size, and milling technique. The parameters influence the density, porosity, and mechanical properties. These factors affect the final alumina ceramic products.
Applications of Alumina Ceramic Powders
Electronics and Electrical Components
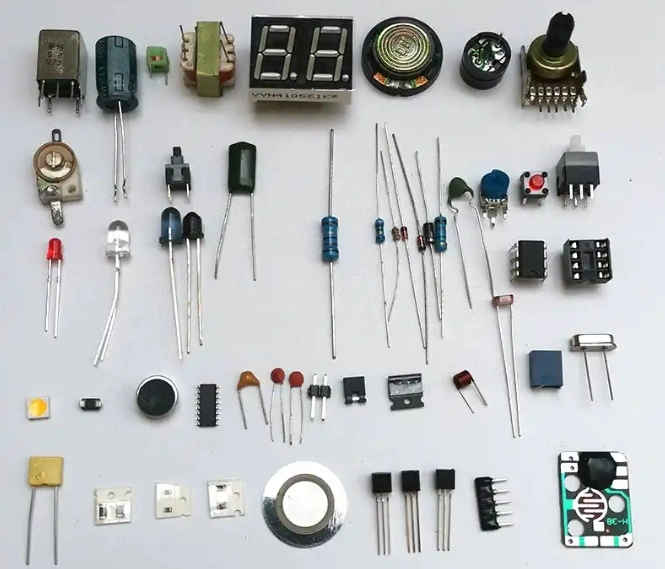
Due to its excellent electrical insulating properties, alumina is widely used in the electronics industry. It is used in the production of substrates for electronic devices, insulators for circuit boards, and protective coatings for semiconductors. Alumina ceramic powders are also utilized in the manufacturing of capacitors, resistors, and sensors.
Cutting Tools and Abrasives
Alumina ceramics are extensively used in the production of cutting tools, abrasives, and wear-resistant parts. Its hardness and wear resistance make it ideal for applications such as grinding wheels, sandpapers, and metal cutting tools. Additionally, alumina is used in the production of components for the automotive and aerospace industries, where durability and performance are paramount.
Medical Applications
In the medical field, alumina ceramic powders are used in the production of artificial joints, dental implants, and other biocompatible components. Its biocompatibility, wear resistance, and strength make it an ideal material for long-term implants. Alumina is commonly used in hip and knee replacements, as well as dental crowns, where durability and low friction are important.
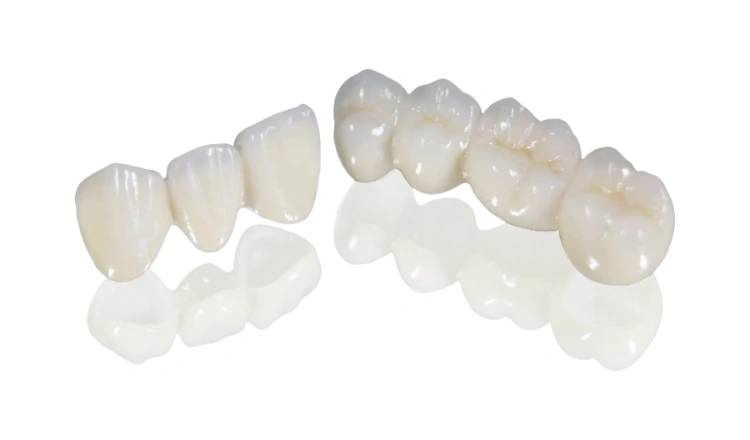
Structural Ceramics
Alumina is commonly used in structural ceramics, such as bearings, seals, and valves, due to its mechanical strength and resistance to wear and corrosion. It is often used in environments that require high-performance materials, such as in the chemical processing and power generation industries.
Aerospace and Automotive Industries
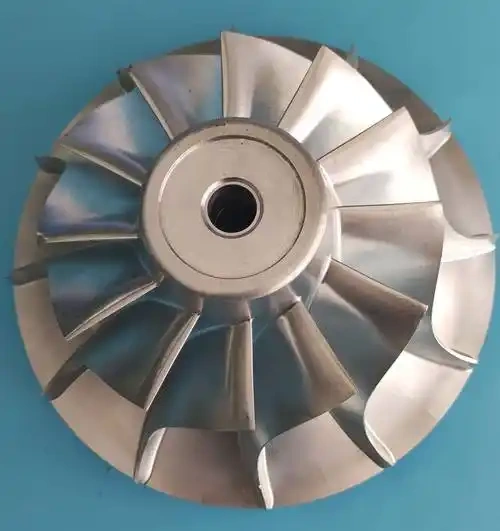
Alumina ceramics are used in high-performance aerospace and automotive applications, such as heat shields, wear-resistant coatings, and engine components. Their ability to withstand high temperatures and mechanical stress makes them valuable in these industries, where materials are exposed to extreme conditions.
Ceramic Armor
Due to its high hardness and fracture toughness, alumina is also used in ballistic armor. Alumina ceramic plates are commonly used in personal body armor, military vehicles, and protective shields for high-risk operations, offering effective protection against projectiles and shrapnel.
Conclusion
Alumina ceramic powders are an essential material with a wide range of applications. These applications span across various industries, including electronics, manufacturing, medical, and aerospace. Their exceptional properties include high hardness, chemical resistance, and electrical insulation. These properties make them versatile and valuable for many high-performance applications. As manufacturing technologies continue to evolve, alumina ceramics will play a more significant role. They will drive innovations in material science and technology.
epic powder
Epic Powder, 20+ years of work experience in the ultrafine powder industry. Actively promote the future development of ultra-fine powder, focusing on crushing,grinding,classifying and modification process of ultra-fine powder. Contact us for a free consultation and customized solutions! Our expert team is dedicated to providing high-quality products and services to maximize the value of your powder processing. Epic Powder—Your Trusted Powder Processing Expert !