Due to the hydrophilic nature of quartz powder surfaces, it is difficult to compatibilize with organic polymers. Therefore, quartz powder surface modification is needed to change its properties from hydrophilic to hydrophobic. This improves the wettability of the quartz powder particles, making it easier for them to disperse in organic compounds.
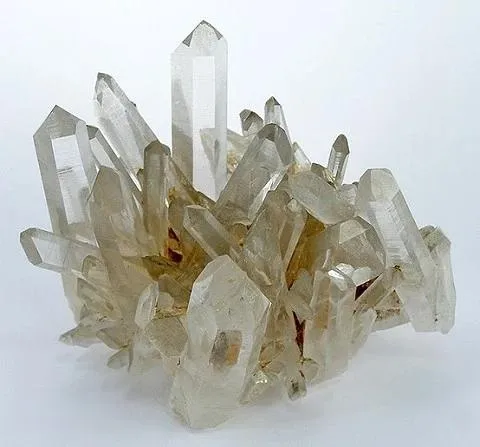
Principle of Quartz Surface Modification
Generally, the finer the quartz powder particles, the larger the specific surface area and the more surface-active hydroxyl groups, making it more reactive. After modification, the effect is improved. Silicate minerals like quartz, when mechanically crushed, generate free radicals or ions on the newly formed surface. Under external conditions, groups like Si-OH, Si-O-Si, and Si-OH···H are formed on the surface. These groups can easily bond with foreign functional groups, achieving the modification goal and providing a foundation for surface modification. In the modification process, factors such as temperature, choice and amount of modifier, treatment method, and modification process are the main factors affecting the modification effect.
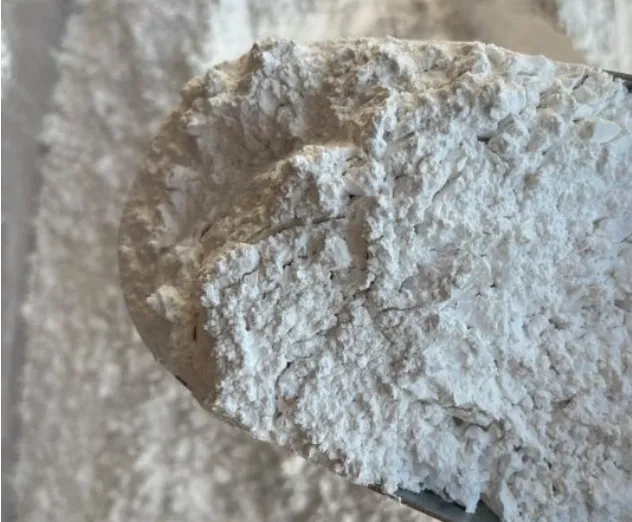
Modification method
There are many methods for organic surface modification of quartz powder, but relying solely on physical adsorption onto the surface of quartz powder results in poor modification effects. It can easily detach during processes such as stirring and washing, and cannot significantly improve product performance in application.
High-energy modification has high costs, is technically complex, and is difficult to achieve in industrial production.
Mechanical chemical modification involves mechanically grinding the powder to create temporary active sites on the surface, reducing the activation energy for surface modification.
Chemical coating modification is the most commonly used method for surface modification of quartz powder. This includes coupling agent modification and polymer grafting. The bonding mechanism involves forming covalent bonds with the surface of the quartz powder. In coupling agent modification, the hydrolysis of the coupling agent generates silanol groups.
These groups undergo dehydration condensation with the silica hydroxyl groups on the quartz powder surface to form covalent bonds. This method is cost-effective, provides high modification effects, and the modified product maintains stable performance for a longer time.
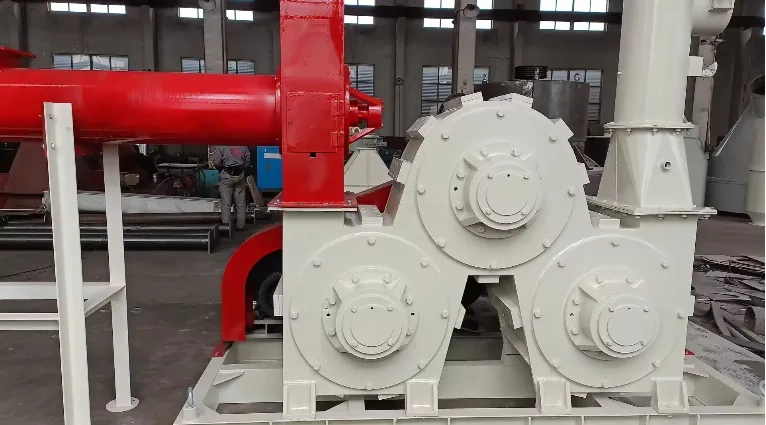
Modification process
In industrial production, mechanical dry modification is mostly used. The modifier is sprayed in during grinding, which shortens the industrial process. This method generates temporary active sites and high temperatures, facilitating surface modification. The product does not need dehydration and drying. However, the modification effect is significantly worse compared to wet methods. The modification is difficult to achieve uniformly, and localized high temperatures may damage the modifier.
Control over the process is also challenging. After dry modification, the quartz powder is considered a coarse product in industrial applications. It is widely used in plastics, building materials, and rubber industries. Wet modification involves soaking, heating, stirring, and dehydrating the quartz powder with reagents. It is more complex than dry methods but offers better modification effects. It is generally used in high-end industries like films and coatings.
The mechanochemical and chemical coating composite modification process involves adding modifiers during grinding. The process combines fine grinding and superfine grinding. As the quartz sand particle size decreases, surface modification occurs. This composite modification process is simple. Some modifiers also assist grinding, improving crushing efficiency. However, temperature control is difficult. The particles are continuously crushed, generating new surfaces. The modifier coating may not be uniform. Additionally, high temperatures generated by the equipment may decompose modifiers or damage their molecular structure.
The drying and chemical coating composite modification process involves adding modifiers during the wet powder drying process. This is a composite process where dehydration and surface modification occur simultaneously. The drying process operates at a high temperature (above 200°C).
Modifier
The main modifiers for quartz powder modification include silane coupling agents, aluminate coupling agents, and titanate coupling agents. Fatty acids and some cationic surfactants (such as hexadecyltrimethylammonium bromide) are commonly used for surface modification in industry. These modifiers are low-cost and simple to apply, but the modification effect is generally average, resulting in coarse-grade products. Silane coupling agents provide the best surface modification effect for quartz powder but are more expensive. Aluminate and titanate coupling agents are lower in cost and easier to apply, but their modification effect is not as good as that of silane coupling agents.
Surface modification of quartz powder with modified polysiloxane can effectively alter its surface properties. This reduces resin usage in artificial quartz stone processing. As a result, the production cost of artificial quartz stone slabs is significantly lowered.
Using mechanical ball milling increases the contact and collision opportunities between modified polysiloxane and quartz powder. This promotes the modification reaction and achieves excellent results.
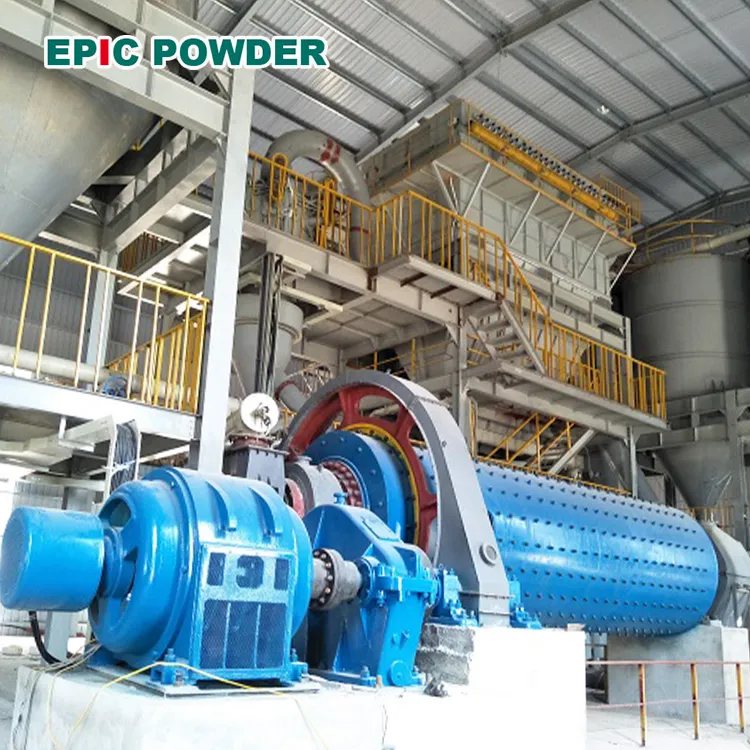
Considering oil absorption value, viscosity, penetration time, and economic cost factors, the optimal dosage of modified polysiloxane is 3.5‰.
Conclusion
Currently, the demand for modified quartz powder is shifting towards ultrafine particle sizes. Nano quartz powder has a three-dimensional network structure. This gives it unique properties, making it irreplaceable in many applications. It has a promising development outlook. With continuous updates in production equipment, high-end modification technologies will become industrialized. This will greatly expand its application range.
epic powder
Epic Powder, 20+ years of work experience in the ultrafine powder industry. Actively promote the future development of ultra-fine powder, focusing on crushing,grinding,classifying and modification process of ultra-fine powder. Contact us for a free consultation and customized solutions! Our expert team is dedicated to providing high-quality products and services to maximize the value of your powder processing. Epic Powder—Your Trusted Powder Processing Expert !