In many industries using natural quartz as raw material, reducing particle size and increasing silicon content are key processes. The quartz sand powder, with an average particle size in the micron (10^-6m) range, is called silicon powder. It is also known as silica powder or quartz powder.
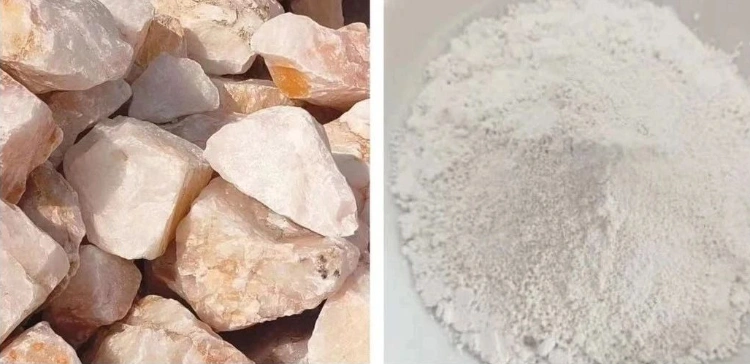
Silicon micropowder is a non-toxic, odorless, and non-polluting inorganic non-metallic material. It is made from natural quartz through sorting, crushing, washing, purification, drying, iron removal, grinding, and classification. With excellent properties such as good temperature resistance, acid-alkali corrosion resistance, high thermal conductivity, and high insulation, it is widely used in chemicals, plastics, coatings, high-grade paints, rubber, electronics, electrical appliances, integrated circuits (ICs), and defense industries.

Core indicators of silicon powder
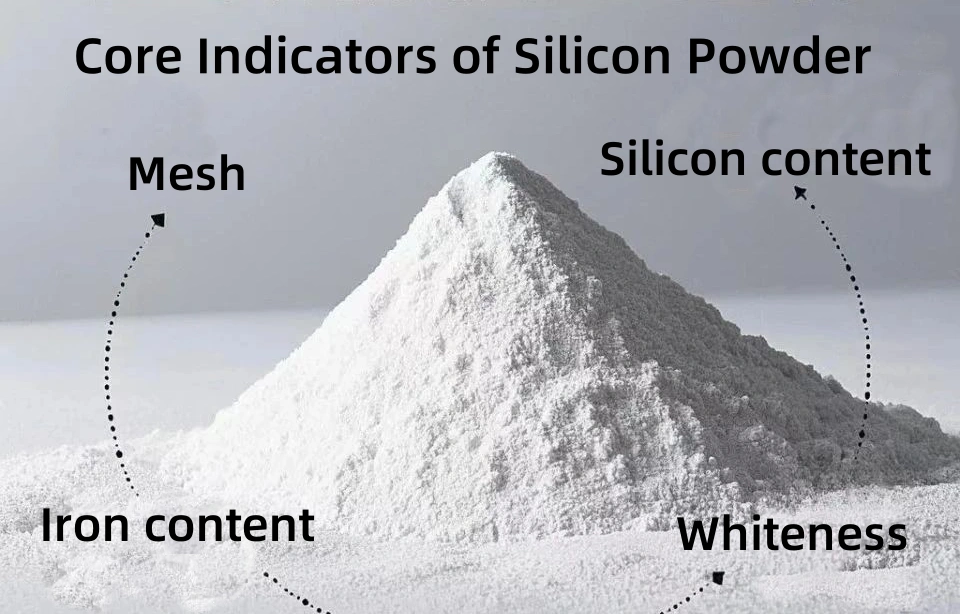
Mesh
Mesh size is commonly used in the industry to describe the average particle size of silicon powder. The particle size range of silicon micropowder is wide, with common sizes ranging from 300 mesh to 3000 mesh. This corresponds to particle sizes from approximately 50 microns to 5 microns. The finer the particle size, the higher the mesh number. The mesh size of silicon micropowder acts as an “invisible lever” for its application performance. By precisely controlling the particle size distribution, multiple goals such as enhancement, toughening, and functionalization can be achieved in various fields.
- In plastics and rubber industries, coarse powders replace part of the resin, reducing raw material costs. They improve compressive strength and dimensional stability in PP, PE, and other plastics.
Fine powders are used in PVC profiles and rubber seals to reduce surface roughness. - In ceramics and refractory materials, coarse powders enhance thermal shock resistance and mechanical strength. Fine powders promote low-temperature sintering of glazes, reducing pores and cracks.
- In adhesives and sealants, medium and fine powders control rheological properties, preventing sagging. Fine particles fill voids, improving adhesive layer density and shear strength.
- In coatings and inks, fine powders reduce surface roughness, improving gloss and smoothness. They also fill micropores, enhancing wear and scratch resistance.
- In electronic packaging and copper-clad laminates, ultra-fine powders reduce dielectric constant and improve thermal stability. Precise control ensures matched thermal expansion coefficients, reducing stress cracking.
- In pharmaceuticals and cosmetics, ultra-fine powders provide a silky feel in sunscreens, avoiding whitening. High specific surface area adsorbs sebum or active ingredients for skincare and ointment carriers.
Silicon content
Silicon content in silicon powder refers to the mass percentage of silicon dioxide. In industries using natural quartz, the silicon content, or purity, is a key indicator of silicon products. Depending on the application, silicon content is classified into three grades: industrial-grade silicon micropowder, high-purity silicon micropowder, and electronic-grade silicon micropowder.
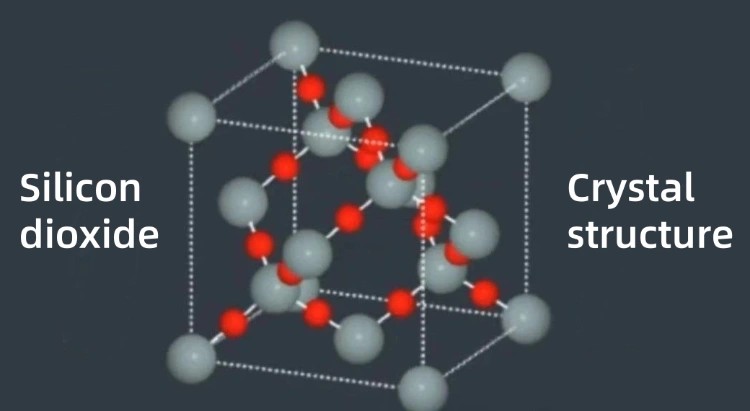
- Industrial-grade silicon powder is cost-effective, with strong process adaptability, meeting performance needs in most industrial scenarios. It is the “invisible pillar” of traditional manufacturing industries.
- High-purity silicon powder has strong chemical stability, diverse functions, and high added value, making it the “invisible engine” of high-end manufacturing industries.
- Electronic-grade silicon micropowder is the top category, dominating advanced fields like semiconductors, optical communication, and renewable energy. It excels in electrical insulation, thermal stability, and functional precision.
Iron content
Iron content refers to the proportion of Fe2O3 in silicon powder. Due to the metallic and magnetic properties of iron, it can affect the performance of silicon micropowder products.
Therefore, iron content is a core indicator affecting the performance of silicon powder.
- In electronic packaging, high-purity silicon powder improves insulation and thermal stability of packaging materials. However, excessive iron content can reduce insulation performance, affecting product stability and reliability.
- Although low-iron silicon micropowder dominates, high-iron content can play a unique role in certain scenarios. For example, silicon powder with iron oxide is used in electromagnetic shielding coatings to absorb high-frequency electromagnetic waves, such as in 5G base station rooms.
whiteness
The whiteness of silicon powder is an important indicator of its color purity and impurity content. The higher the whiteness value, the closer the material is to pure white and the less impurities it has.
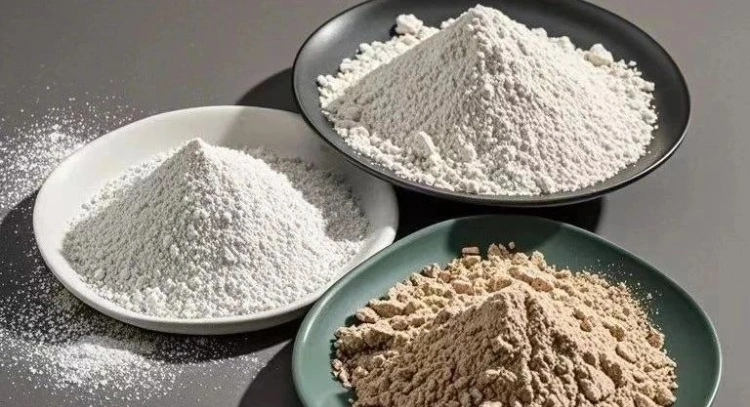
- In the coatings and paints industry, high-white silicon micropowder reduces titanium dioxide usage, lowering costs. It also fills micropores, enhancing coverage and uniform whiteness of the coating. Additionally, low impurities reduce UV-induced yellowing, extending the coating’s lifespan.
- In white or light-colored plastic and rubber products (such as refrigerator and air conditioner housings), high-white silicon micropowder prevents color variation caused by impurities, improving product appearance. In transparent or semi-transparent materials, high-purity silicon micropowder reduces light scattering, maintaining transparency.
- In electronic packaging materials, whiteness indirectly reflects purity. Low-impurity silicon micropowder reduces dielectric loss and improves the reliability of integrated circuit packaging. Moreover, high-white substrates provide strong contrast with dark markings, enhancing the clarity of electronic component labels.
- In ceramic glazes, adding high-white silicon micropowder enhances gloss and whiteness, reducing post-firing spot defects.
- As a glass raw material, low iron content (high whiteness) reduces discoloration in glass, improving light transmission.
- In cosmetics and pharmaceuticals, high-white silicon micropowder has low impurities and low irritation when used as an adsorbent or thickener in skincare products. It also provides a delicate visual texture.
- In coated paper, adding high-white silicon micropowder enhances paper whiteness, making printed colors more vibrant.
conclusion
The “silicon content” and “mesh size” of silicon powder are its “dual cores” for application performance. “Silicon content” defines chemical stability and functional limits, determining whether it can enter high-end fields. “Mesh size” controls physical form and interface effects, influencing processing adaptability and performance. The coordinated design of both can meet a wide range of demands, from industrial filling to cutting-edge technology. In the future, through process innovation and interdisciplinary integration, silicon micropowder will open up high-value applications in fields such as new energy and biomedicine.
Epic powder
Epic Powder, 20+ years of work experience in the ultrafine powder industry. Actively promote the future development of ultra-fine powder, focusing on crushing,grinding,classifying and modification process of ultra-fine powder. Contact us for a free consultation and customized solutions! Our expert team is dedicated to providing high-quality products and services to maximize the value of your powder processing. Epic Powder—Your Trusted Powder Processing Expert !