In the lithium-ion battery field, silicon-based anode materials are called the “hope of next-generation high-energy-density batteries” due to their 4200mAh/g capacity.
However, severe volume expansion during charge and discharge (over 300%) acts like a “curse.” This causes electrode pulverization and rapid capacity loss, severely hindering commercialization. To break this deadlock, scientists focus on vapor-deposited silicon-carbon anode technology. The core carrier material, porous carbon, plays a key role in this breakthrough.
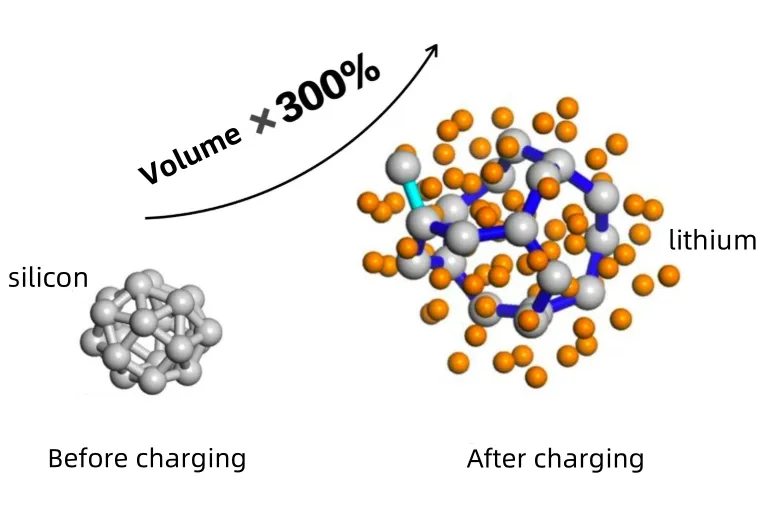
Porous carbon: Why is it the “golden partner” of silicon-carbon anode?
“Flexible space” resolves the expansion crisis
Silicon’s volume expansion is like gas trapped in a sealed container. Without buffer space, structural collapse is inevitable. The 3D interconnected pores of porous carbon act as a “flexible refuge” for silicon particles. These pores provide physical space for silicon expansion and disperse stress through elastic deformation. This significantly reduces the risk of particle fracture. Studies show that when the porosity of porous carbon exceeds 70%, the cycle life of the silicon anode can increase by more than three times.
Conductive “highway” breaks the transmission bottleneck
Silicon has extremely poor conductivity (only 1×10⁻³ S/cm). In contrast, porous carbon has a conductivity of 100–1000 S/cm. By vapor deposition, silicon is uniformly coated on the its surface. The carbon framework acts as an “electronic highway,” enabling fast electron transport between the active material and the current collector. Experimental data shows that the charge transfer resistance of porous carbon-based silicon anodes can be reduced by 90% compared to pure silicon.
Ion transport “green channel” improves rate performance
The hierarchical pore structure of porous carbon (micropores + mesopores + macropores) forms a graded permeation network.
Micropores (<2 nm) provide a high surface area for lithium-ion adsorption.
Mesopores (2–50 nm) serve as the main ion diffusion channels.
Macropores (>50 nm) act as electrolyte reservoirs.
This “three-pore synergy” allows the electrode to retain 80% capacity even at a high 10C rate.
“Nanocage” effect inhibits runaway growth of SEI film
Silicon surface cracking repeatedly forms a solid electrolyte interphase (SEI) film, causing continuous active lithium loss. Porous carbon physically confines silicon particles within its pores, creating a “nanocage” structure. This design strictly limits SEI film growth to the carbon framework surface. A Tsinghua University study found that this approach increases the initial efficiency of silicon anodes from 65% to 89%.
Six “hard core indicators”
Pore structure
- Specific surface area: ≥1500 m²/g (providing sufficient silicon loading sites)
- Porosity: >80% (ensuring expansion buffer space)
- Pore size distribution: micropores: mesopores: macropores ≈ 1:4:5 (taking into account both ion transport and mechanical strength)
Conductive properties
Graphitized porous carbon must have a conductivity >500 S/cm and form a continuous sp²-hybridized carbon network. Graphitized porous carbon must have a conductivity >500 S/cm and form a continuous sp²-hybridized carbon network. There is a research team used laser-induced graphitization to increase porous carbons conductivity to 1200 S/cm. This enabled the silicon anode to retain 92% capacity at a current of 5A/g.
Mechanical strength
The compression modulus must exceed 10 MPa to withstand the GPa-level stress from silicon expansion.
Inspired by biomimicry, a research team developed a honeycomb-like porous carbons structure. Its compressive strength reaches 25 MPa, maintaining over 95% structural integrity after 500 cycles.
Surface Chemistry
- Functional group regulation: Introducing oxygen-containing groups (-COOH, -OH) can enhance the silicon-carbon interface bonding. However, the content must be controlled below 5% to avoid side reactions.
- Doping modification: Nitrogen doping (3-5 at%) improves lithium-ion transport kinetics at the interface. Phosphorus doping enhances structural stability.
Thermal stability
The structure must remain stable below 300°C (with a weight loss <1%) to prevent battery thermal runaway. Using silicon carbide coating technology increases the initial decomposition temperature of porous carbon from 420°C to 580°C.
cost
Under the premise of ensuring performance, the cost of porous carbon must be controlled within a reasonable range to enable large-scale commercial applications.
Porous carbon preparation: four major technical routes
- Template method: a precisely controlled “nano-architect”
- Hard template: Using SiO₂ nanospheres as templates, carbonized and etched with HF, uniform pore-sized (±2 nm) porous carbon can be prepared. However, it poses an environmental pollution risk.
- Soft template: Using amphiphilic block copolymers like F127, self-assembly forms ordered mesopores, making it more suitable for large-scale production.
2. Activation method: a simple and crude “hole-making master”
- KOH activation method: At 800°C, KOH reacts with carbon (6KOH + 2C → 2K + 3H₂ + 2K₂CO₃) to produce super-porous carbon with a specific surface area >3000 m²/g, but it can cause an excess of micropores.
- CO₂ physical activation: More environmentally friendly, but the specific surface area is usually <1000 m²/g.
3. Biomass Derivative Method: A Green and Sustainable “Gift from Nature”
- Biomass such as coconut shells and bamboo undergo pre-carbonization (300-500°C) and activation (KOH, 700°C) to obtain porous carbon with a high mesopore ratio (>60%).
4. 3D printing technology: the “factory of the future” for customized structures
- Direct writing (DIW) 3D printing combined with freeze drying can be used to prepare porous carbon with a gradient pore structure. It maintains excellent performance when the silicon loading is greater than 5 mg/cm² and is regarded as the next generation mainstream technology.
Industrial breakthrough: a critical leap from laboratory to mass production
Currently, porous carbon-based silicon-carbon anodes have entered the industrialization sprint phase:
- Tesla’s 4680 battery uses porous carbon-coated silicon oxide anodes, achieving a monomer energy density exceeding 300 Wh/kg.
- CATL’s “Qilin Battery” uses multi-stage pore carbon design, extending the silicon anode’s cycle life beyond 1200 cycles.
Challenges and opportunities coexist: Balancing high specific surface area with low tapped density (currently <0.3 g/cm³) and developing dry electrode processes are still technological hurdles to overcome.
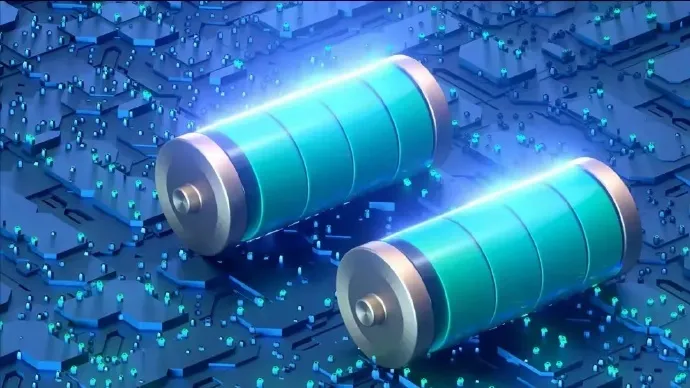
Conclusion: Porous Carbon – Opening the “Golden Era” of Silicon-Based Anodes
From the innovative sparks in the laboratory to the rapid industrialization, porous carbon, with its unique structural advantages, is rewriting the commercialization story of silicon-based anodes.
With continuous advancements in preparation technologies and cost reduction, the market for porous carbon-based silicon-carbon anodes is expected to surpass $5 billion by 2025.
This “material revolution” led by porous carbon may be the key to unlocking the era of high-energy-density batteries.
epic powder
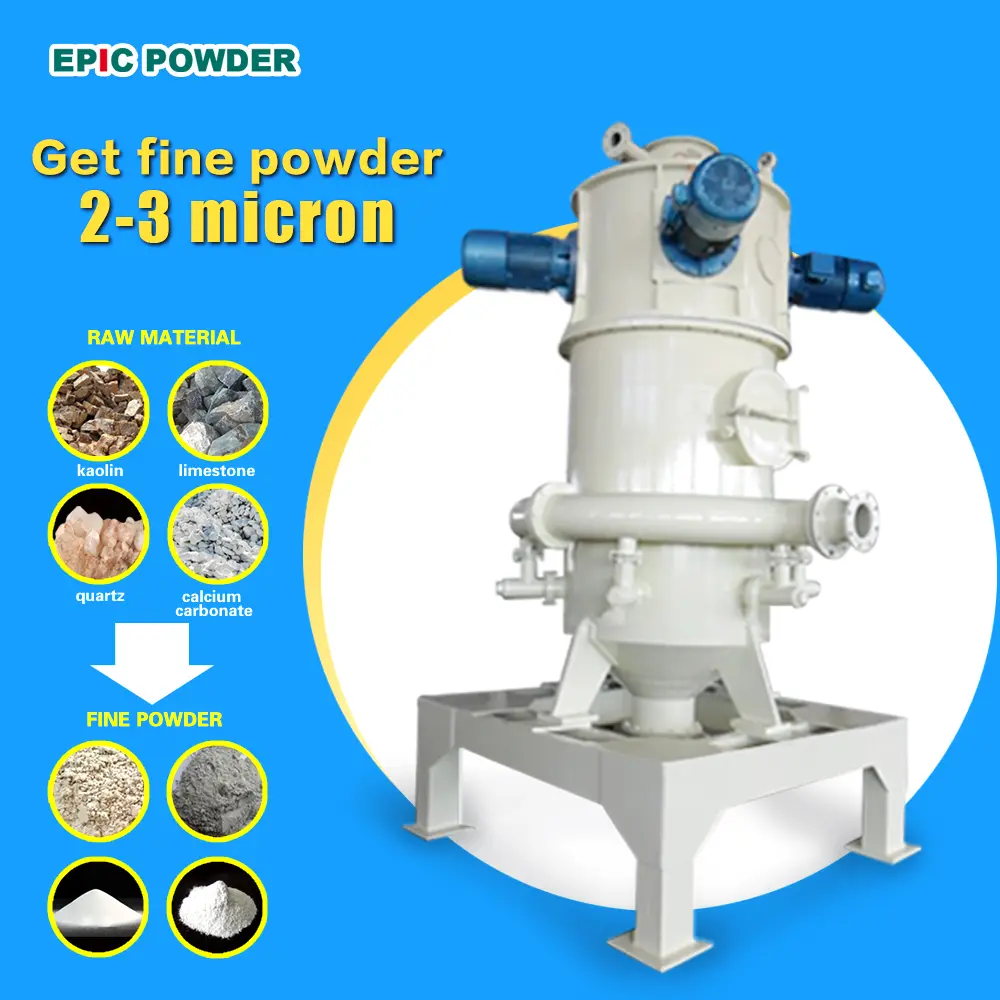
The preparation of porous carbon is inseparable from ultrafine grinding. Epic Powder, 20+ years of work experience in the ultrafine powder industry. Actively promote the future development of ultra-fine powder, focusing on crushing,grinding,classifying and modification process of ultra-fine powder. Contact us for a free consultation and customized solutions! Our expert team is dedicated to providing high-quality products and services to maximize the value of your powder processing. Epic Powder—Your Trusted Powder Processing Expert!