The “Ultrafine Revolution” of Cosmetic Ingredients: Why Jet Milling is Essential
In the cosmetics industry, the fineness of raw material powders directly determines the texture and efficacy of the final product. Traditional grinding methods, such as ball milling and roller pressing, often struggle to avoid metal contamination and high-temperature oxidation. In contrast, jet milling, with its contact-free pulverization, low-temperature processing, and ultra-high purity, has become a core technology in the preparation of high-end cosmetic ingredients. For example:
- Foundation Products: Jet mill reduces titanium dioxide (TiO₂) and mica to D90<5 μm, enhancing coverage and skin adhesion.
- Sunscreen: Nano-scale zinc oxide (ZnO) particles (D50<100 nm) processed by jet mill provide transparent, non-whitening UV protection.
- Eyeshadow/Blush: Controlled particle size (10-50 μm) of pearlescent pigments (e.g., calcium sodium borosilicate) directly impacts color saturation and luster.
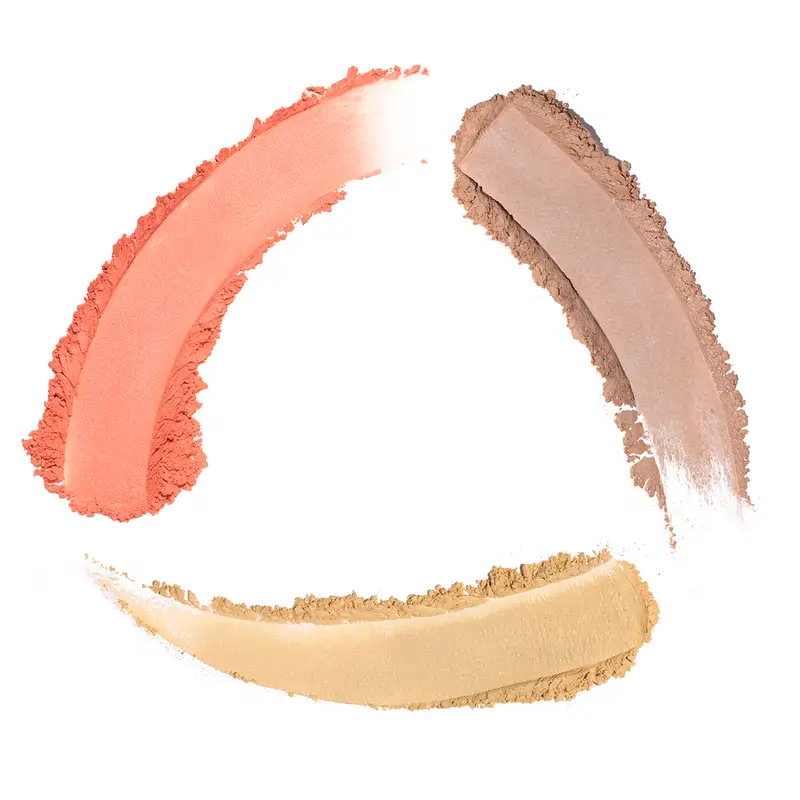
How Does Jet Milling Reshape Cosmetic Ingredient Processing?
Core Principle: Contamination-Free “Self-Collision Pulverization”
Jet mill uses supersonic airflow (300-500 m/s) to drive particle collisions for pulverization. It avoids contact with metal components. For example, ceramic-lined jet mills (e.g., Al₂O₃ or SiC) ensure zero iron and nickel contamination. This meets the EU EC 1223/2009 regulation’s strict heavy metal residue requirements for cosmetic ingredients.
Low-temperature processing: Protect active ingredients
Many active ingredients in cosmetics (such as vitamin C and peptides) are temperature-sensitive. The adiabatic expansion effect of jet milling keeps the grinding chamber temperature below 40°C, preventing thermal degradation.
Experimental data shows that compared to ball milling (which reaches 80°C), jet milling retains over 30% more astaxanthin activity.
Precise Particle Size Control: From “Flour” to “Nano”
By adjusting the classifier wheel speed (1000-15000 rpm) and airflow pressure (0.5-1.2 MPa), jet mill achieves precise classification.
It can range from micron (1-50 μm) to submicron (0.1-1 μm) levels. For example:
- Loose Powder Products: Talc powder with D50=8 μm creates an “airy” makeup effect.
- Nano Emulsion: Hyaluronic acid, pulverized by jet milling to 200 nm, enhances permeability by 50%.
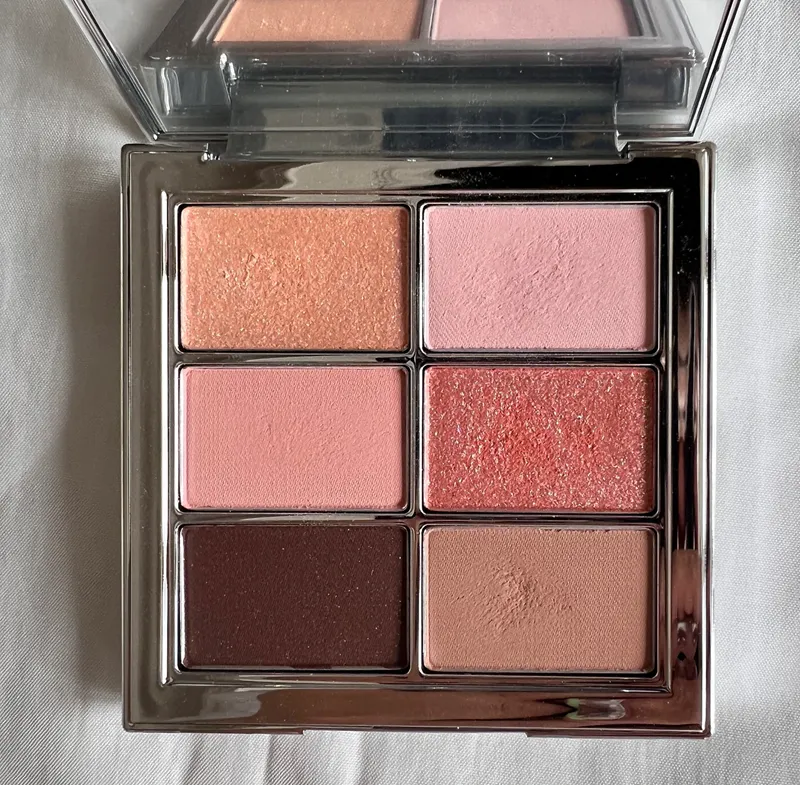
Industry Application Case: Jet Milling-Driven “Makeup Effect Enhancement
Case 1: The Birth of Ultrafine Pearl Powder
A Japanese brand used nitrogen-protected jet milling to process pearl powder, reducing the particle size from 20 μm to 1.2 μm.
It preserved the natural structure of pearl protein.
The finished foundation liquid saw a 40% increase in luster, with no “powdery” sensation from traditional methods
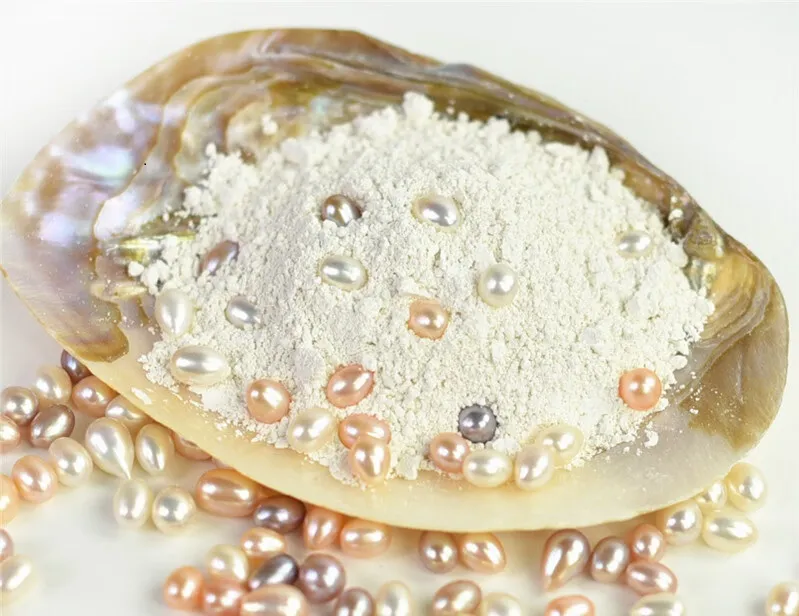
Case 2: “Active Preservation” of Plant Extracts
A French organic brand used low-temperature jet milling to pulverize rose petal extract, preventing flavonoid degradation.
The final serum’s antioxidant performance improved by 25% compared to traditional methods, with no preservatives added.
Case 3: Breakthrough in Sunscreen Transparency
An American brand used nano jet milling to refine zinc oxide particles to 80 nm.
The sunscreen achieved an SPF of 50+, eliminating the “white cast” and revolutionizing the user experience of mineral sunscreens.
Conclusion: jet Mill – the Invisible Promoter of Beauty Technology
From “heavy powdery feel” to “bare-skin makeup effect,” and from “physical sunscreen” to “transparent protection,” jet milling technology is driving the cosmetics industry towards safer, more efficient, and sustainable evolution.
In the future, as demand for “technology-based skincare” grows, jet milling may become a key technological barrier for beauty brands’ differentiation.
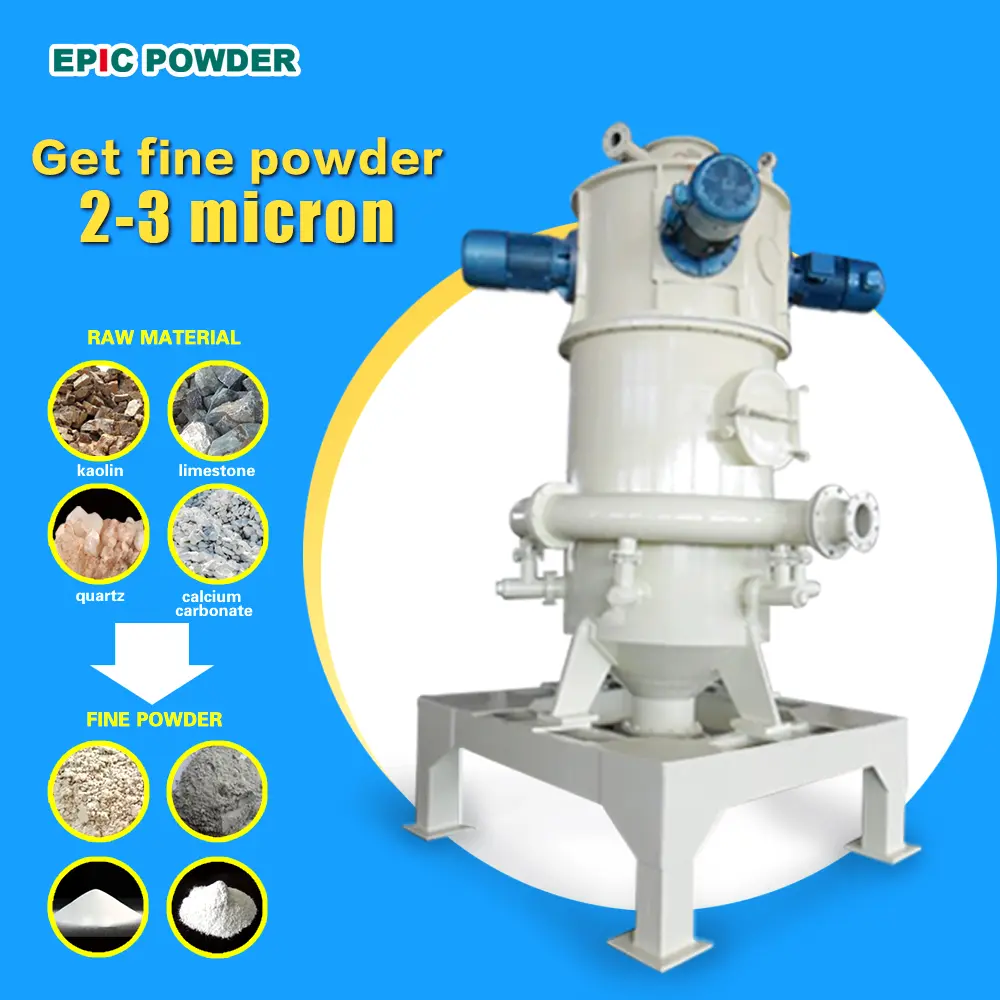