Spherical powder shows excellent morphology, particle size distribution, and flowability. It is widely used in high-end industries. The use of high-performance spherical powders significantly enhances the precision and efficiency of additive manufacturing processes. With rapid industrial and technological development, various industries demand higher performance from powder materials. Powders must have low impurity levels and fine particle sizes. They also require narrow particle size distribution and specific shapes. Spherical powder offers ideal morphology, size control, and flow properties. Thus, it finds broad application in advanced sectors.
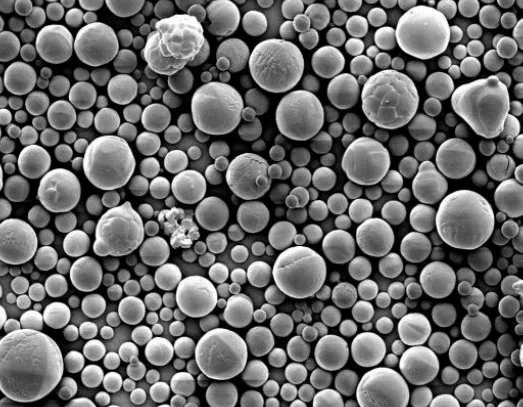
Spherical powder has clear advantages over irregular powder. Its surface is smooth and with fewer defects. It reduces mold wear during processing and forming. Spherical powder has a narrow particle size distribution. The particle sizes are more uniform and consistent. It also shows excellent flowability and packing density. In powder metallurgy, it improves the compact’s density. During sintering, shrinkage is more uniform and controlled. Grain size regulation becomes easier and more effective.
Spherical graphite
Spherical natural graphite is made by shaping natural graphite particles. The goal is to form spherical or near-spherical graphite. Natural graphite is low-cost and widely available. It also has suitable charge-discharge characteristics. Thus, it plays a key role in anode materials. However, natural graphite has low reversible capacity. Its cycling stability is also relatively poor. These drawbacks limit its use in lithium batteries. Studies show spherical graphite improves electrochemical performance.
It reduces surface area and increases tap density. This leads to higher first Coulombic efficiency. Also, it offers better reversible capacity and stability. Spherical natural graphite is widely used in Li-ion anodes.
Spherical silica powder
Spherical silicon micropowder has good shape, high chemical purity, and low radioactive element content. Its application greatly reduces the coefficient of thermal expansion and improves thermal stability of molding compounds. Therefore, it is widely used in integrated circuit production. Spherical silicon micropowder is mainly prepared by methods such as high-temperature plasma melting, high-temperature spraying, gas combustion flame, vapor phase, and precipitation methods. At present, domestic spherical silicon micropowders still lag behind international products in terms of high purity, ultrafineness, and high spheroidization rate.
Spherical refractory metal powder
Refractory metals have melting points above 1650°C and sufficient reserves. Key examples include tungsten, titanium, and molybdenum. They are widely used in aerospace and 3D printing. Other fields include thermal spray coatings and biomedicine.
Spherical metal powders outperform traditional metal powders. They offer high sphericity, flowability, and bulk density. Such powders are increasingly used in materials science. High-performance spherical metal powders remain a limiting factor.
Traditional methods yield low spheroidization and high agglomeration. They are also prone to oxidation. Radio-frequency plasma processing improves powder properties significantly. It enhances flowability, tap density, and spheroidization rate. Improving ultrafine refractory powder performance is essential. Reducing pollution and cost during production is critical. Scaling plasma technology for industry is the future direction.
Spherical metal oxide powder
Spherical Magnesium Oxide:
Magnesium oxide’s performance depends on particle size and shape. Among them, spherical particles have regular morphology and uniformity. They offer large surface area and excellent sphericity. These properties enhance adsorption, thermal conductivity, and catalytic performance. In thermal materials, spherical MgO improves packing density. Its composites with PVC show higher thermal conductivity.
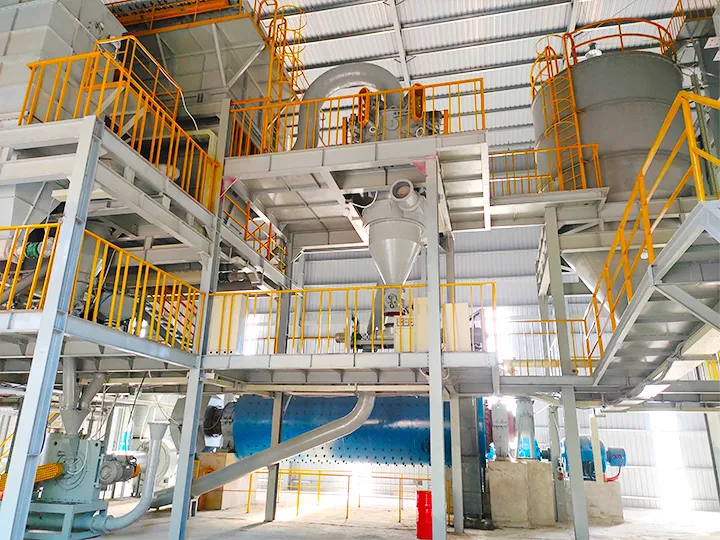
Spherical Alumina:
Alumina is a high-performance industrial material. Many methods are used to create various morphologies: Ball mill, plasma, hydrolysis, sol-gel, precipitation, and hydrothermal methods. Shapes include rod, ribbon, tube, flake, plate, sphere, fiber, spindle, and starfruit-like. Spherical alumina has excellent flowability and surface area. It also provides high bulk density and uniform dispersion. It shows corrosion, high-temperature, acid-alkali, wear, and oxidation resistance. Spherical alumina is widely used in electronics, chemicals, and defense industries.
conclusion
As a core element of materials science and modern manufacturing, spherical powders are reshaping industries like energy and aerospace. With high flowability, uniform bulk density, and controllable surface activity, they offer unique advantages.
As preparation technology advances and interdisciplinary integration deepens, spherical powders drive high-performance material development. They act as an important engine for precision manufacturing and sustainable development. In the future, spherical powder innovation will be demand-driven and technology-based. It will continuously unleash disruptive potential, injecting limitless possibilities into global high-end manufacturing.
epic powder
Epic Powder, 20+ years of work experience in the ultrafine powder industry. Actively promote the future development of ultra-fine powder, focusing on crushing,grinding,classifying and modification process of ultra-fine powder. Contact us for a free consultation and customized solutions! Our expert team is dedicated to providing high-quality products and services to maximize the value of your powder processing. Epic Powder—Your Trusted Powder Processing Expert !