Silica powder is made from crystalline quartz and fused quartz through grinding, precision classification, and impurity removal. Spherical silica refers to silica powder in a spherical form. Spherical silica powder has high heat resistance, insulation, and filling capacity, with low expansion, dielectric constant, and friction coefficient. It is also acid and alkali resistant.Silica powder is widely used in IC packaging, IC substrates, aerospace, and construction materials.

Two major applications of spherical silicon powder
Copper Clad Laminate
With the rapid development of the electronics industry, copper-clad laminate (CCL), as a fundamental material for electronic circuits, faces increasing performance requirements. In high-frequency, high-speed, and high-reliability electronic products, the heat resistance of CCL is a key factor affecting its lifespan and reliability. It directly impacts the reliability and stability of electronic products.
Silica powder has good filling properties, electrical insulation, and thermal stability. Adding it to CCL can improve substrate heat resistance. Silica shape significantly affects the filling capacity. Compared to angular silica, spherical silica has higher packing density and uniform stress distribution. It enhances system flowability. Compared to other silica types, spherical silica has better filling, thermal expansion, and wear resistance.
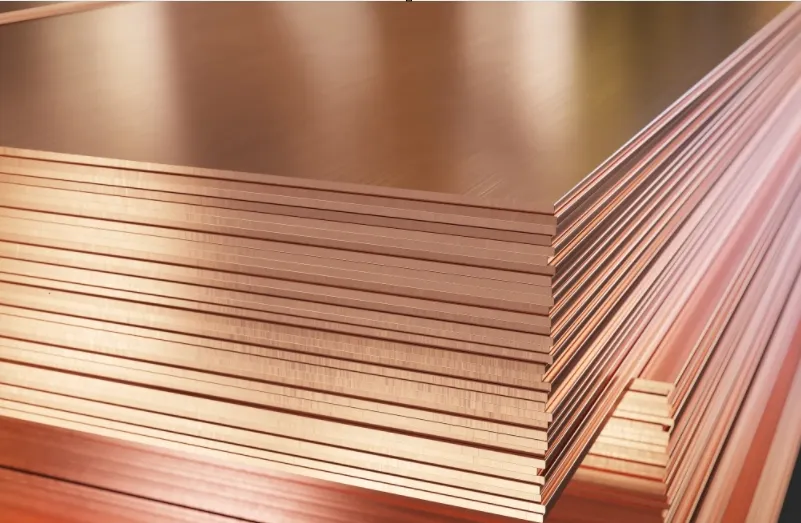
Epoxy Molding Compound (EMC)
Epoxy molding compound (EMC) is a key material for chip packaging in electronic products, closely aligned with the integrated circuit industry. Since pure epoxy resin has a highly cross-linked structure, it has the disadvantages of being brittle, poor heat resistance, and poor impact toughness. Therefore, it is necessary to add fillers with heat resistance and strong curing effect. Silica powder is one of the commonly used fillers. Typical EMC consists of fillers (mainly silica powder, 60%–90%), epoxy resin (below 18%), curing agents (below 9%), and additives (around 3%).
Spherical silica powder has the following characteristics:
First, its SiO₂ content exceeds 99.9%, ensuring stability during use and enhancing the reliability of epoxy molding compounds (EMC).
Second, its sphericity is typically above 0.93, with an overall spheroidization rate exceeding 90%. This reduces the impact on EMC viscosity and improves flowability.
Third, it has high thermal conductivity, a low coefficient of linear thermal expansion, and excellent dielectric properties, making it crucial for EMC quality.
Beyond CCLs and EMC, spherical silica powder enhances ceramic carriers for auto/diesel exhaust systems by improving molding rates and stability. In wind turbine adhesives and construction sealants, it optimizes viscosity, thixotropy, sag resistance, and bonding strength. Submicron spherical silica reduces resin/paint viscosity, enhances flow, minimizes burrs, and serves in semiconductor resins, carbon additives, and silicone rubber.
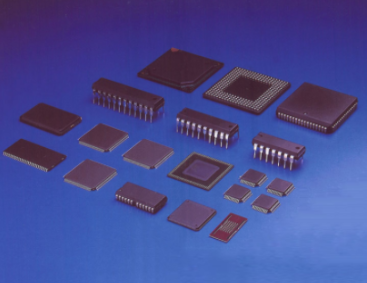
Three major processes of spherical silicon powder
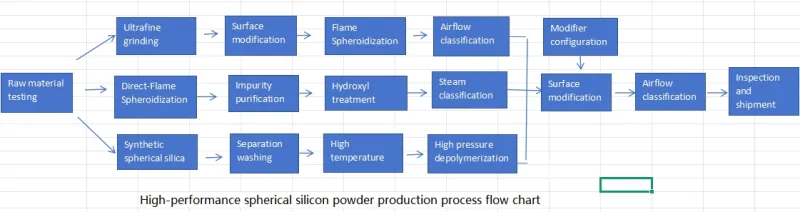
In practical applications, due to the differences in preparation methods, the basic properties of spherical silica powders can vary significantly. Currently, there are three main technological paths for large-scale production of spherical silica powders. These include flame fusion spherical silica powder, direct combustion/VMC method spherical silica powder, and chemical synthesis spherical silica powder.
flame fusion
Crushed, sieved, and purified angular silica powder is used as the raw material. The angular silica powder is crushed by an air jet mill and pretreated through multiple stages. After preprocessing, it is sieved to the appropriate particle size.
Acetylene, natural gas, and other gases are used as heat sources for the molten powder. The flame is clean and pollution-free. Angular silica powder with the appropriate particle size is melted instantly at high temperature using a high-temperature flame fusion method. It is then rapidly cooled and spheroidized to form high-purity, uniform-sized spherical silica powder.
Currently, the mainstream method for producing spherical silica powder in China is flame fusion.
Direct combustion/VMC method
Flame fusion spherical silica is derived from the melting and spheroidization of natural mineral powders. This results in certain limitations in purity and particle size distribution. A few foreign companies use the VMC method, where metal silicon powder reacts directly with oxygen. This method produces silica microspheres with higher purity, smaller particle size, and a relatively controllable size distribution.
Chemical synthesis
Chemical synthesis methods include gas-phase, precipitation, hydrothermal synthesis, and sol-gel methods. Due to limitations in both synthesis pathways and downstream processing technology, only a few companies in the industry can stably ensure particle dispersion, spheroidization rate, and surface smoothness at a high level.
conclusion
High-performance spherical silica powder was once dominated by Japanese companies. Currently, Japanese companies still lead the global high-end spherical silica powder market. There are fewer domestic companies with advanced technology and well-established product lines. At the same time, EPIC Powder is also making efforts, continuously researching and developing. EPIC Powder has overcome technical challenges and developed its unique spherical silica powder preparation route. This has enhanced the competitiveness of domestic spherical silica powder products.
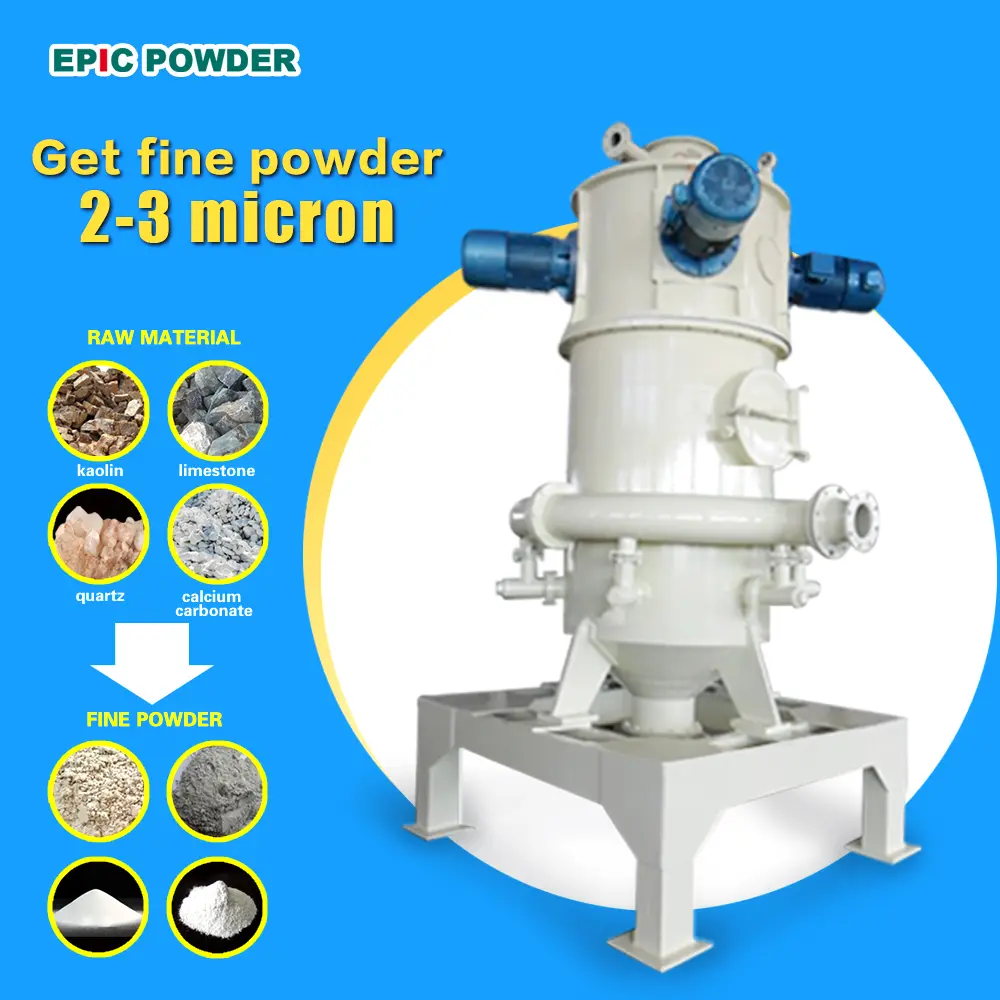