The specific surface area of powder materials significantly impacts their performance and applications. First, the larger the specific surface area, the more active sites are available on the material’s surface. This significantly enhances its adsorption ability, catalytic activity, and reactivity with other substances. These properties make powder materials widely applicable in fields such as high-performance catalysts, efficient adsorbents, and advanced dehydration agents. Different powder materials exhibit substantial variations in specific surface area. For example, highly porous materials like molecular sieves and activated carbon can achieve specific surface areas ranging from hundreds to thousands of square meters per gram (m²/g). In contrast, materials with low porosity or non-porous structures generally show much smaller specific surface areas.
The factors influencing the specific surface area of powdered materials are diverse. They play a key role in both the preparation and application processes.
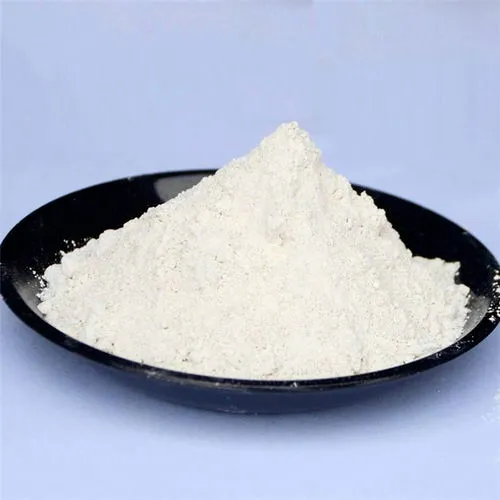
Particle size
Particle size is a direct factor affecting the specific surface area of powdered materials. For the same mass, smaller particles have a larger specific surface area. This is because smaller particles have more surface atoms or molecules, significantly increasing the total surface area. Therefore, by optimizing the preparation process, such as controlling reaction conditions and selecting suitable raw materials and additives, particle size can be effectively controlled, thus influencing the specific surface area.
Particle refinement: Specific steps in the processing, such as mechanical grinding and ultrasonic dispersion, reduce particle size. This significantly increases the material’s specific surface area. This is because the specific surface area is inversely proportional to particle size—smaller particles result in a larger specific surface area.
Agglomeration control: During preparation and processing, particles tend to agglomerate, forming larger clusters. This reduces the specific surface area of the material. By optimizing the process, such as adjusting dispersant type and dosage, controlling pH, and using suitable drying and thermal treatments, agglomeration can be effectively controlled. This helps maintain or increase the specific surface area of the material.
Particle shape
Particle shape has a significant impact on the specific surface area of powdered materials. Among all geometries, spherical particles have the smallest surface-to-volume ratio. Particles with complex shapes (such as plate-like or needle-like) have a larger specific surface area. This is because particles with complex shapes expose more surface area for the same volume. Therefore, during preparation, precise control of reaction conditions and additive type and dosage can control particle shape. This, in turn, alters the specific surface area of the powdered material.
Porosity
Porosity is the ratio of the pore volume to the total volume in powdered materials. The higher the porosity, the more pores are present in the material, and these pores increase the surface area. Therefore, powdered materials with high porosity typically have a larger specific surface area. The regulation of porosity can be achieved by adjusting certain parameters in the preparation process, such as reaction temperature, time, and pressure. Methods in the processing, such as sol-gel and templating, can introduce or control the pore structure in the material. The presence of pore structures increases the internal surface area, greatly enhancing the specific surface area of the powdered material.
By adjusting parameters in the processing, such as precursor solution concentration, gelation conditions, and the type and amount of template agents, the size, shape, and distribution of pores can be precisely controlled. This allows effective regulation of the specific surface area of the powdered material.
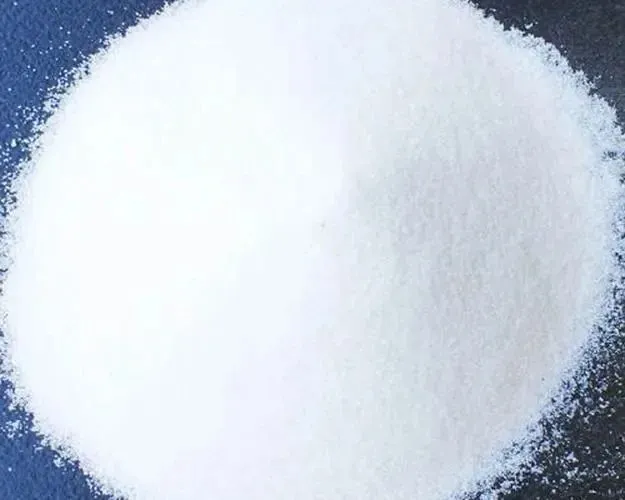
Preparation method
The preparation method is one of the key factors influencing the specific surface area of powder materials. Different preparation methods can result in differences in properties such as particle size, shape, and porosity, which in turn affect the specific surface area. For example, the sol-gel method can produce powders with high specific surface area, uniform particle size, and fine texture. Co-precipitation, on the other hand, can optimize the specific surface area by controlling the precipitation conditions. Therefore, when selecting a preparation method, it is important to choose the appropriate process based on the specific requirements of the application.
Sol-gel method
The method forms a solid precursor through sol aggregation and gelation, followed by heat treatment to obtain powdered material. Its impact on specific surface area is the ability to produce high-specific surface area powders with uniform, fine particle size. By controlling sol concentration, gelation conditions, and heat treatment temperature, the specific surface area of the material can be regulated.
Co-precipitation method
Components in the solution precipitate together in stoichiometric ratios to form a precursor. The precursor is then processed through calcination to obtain powdered material. This method can produce powders with good dispersion and high specific surface area. By controlling precipitation conditions (such as pH, temperature, stirring speed) and calcination parameters, the specific surface area can be optimized.
Mechanical ball milling method
The characteristic of this method is the use of mechanical force to grind raw powder into finer particles. The impact on specific surface area is that ball milling reduces particle size. However, it often causes irregular particle shapes and increased surface defects, affecting precise control of the specific surface area. By optimizing milling parameters (such as milling time, media, and ball-to-material ratio), the specific surface area of the material can be improved to some extent.
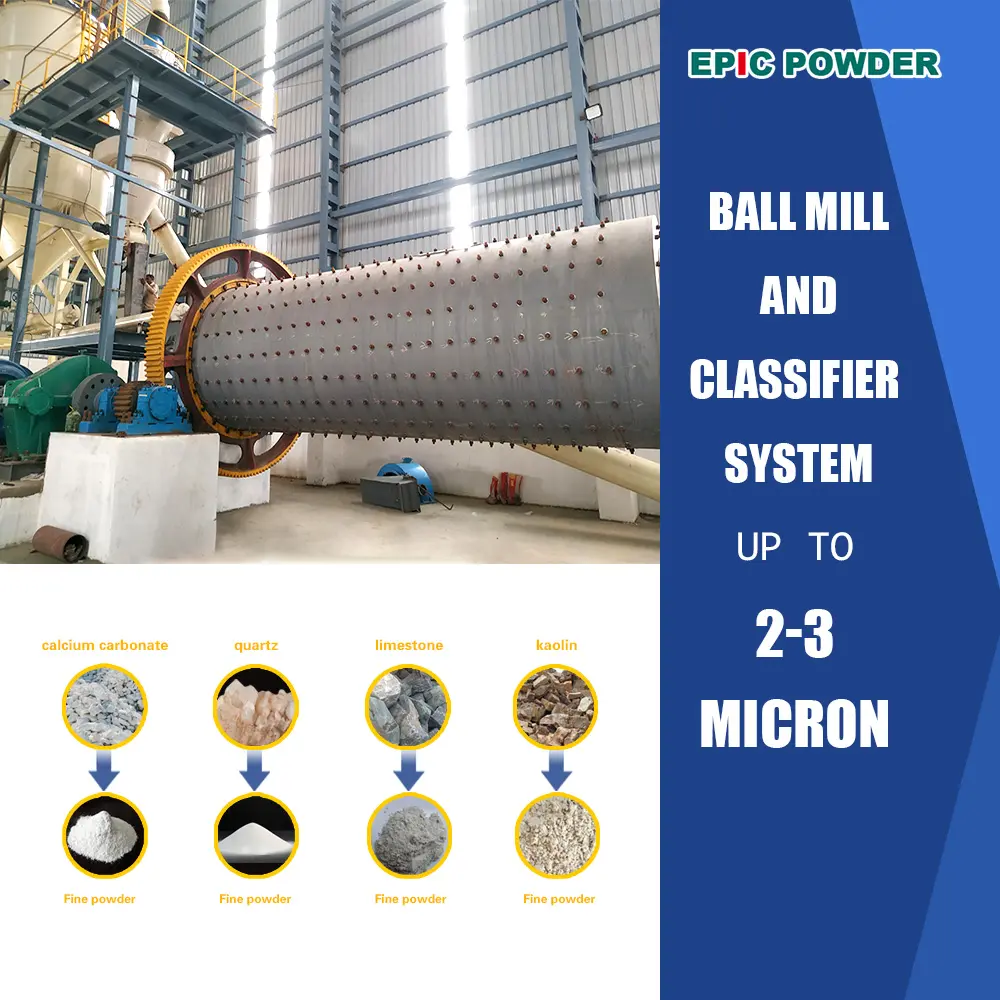
Chemical vapor deposition (CVD) method
The method involves depositing gaseous precursors onto a substrate through chemical reactions at high temperatures to form powdered material. Its impact on the specific surface area is that it can produce powders with high purity and high specific surface area. By controlling deposition temperature, gas flow, reaction time, and other parameters, the specific surface area of the powdered material can be precisely controlled.
Spray pyrolysis method
This method sprays metal salt solutions or sols into a high-temperature pyrolysis furnace. The solvent quickly evaporates and undergoes pyrolysis, forming powdered material. It can produce powders with high sphericity and narrow particle size distribution. It is suitable for preparing high-specific surface area powders with uniform particle size distribution.
Treatment process
Heat treatment, surface modification, and other processing techniques also affect the specific surface area of powder materials. Heat treatment can alter properties such as crystallinity, phase composition, and particle size, thereby influencing the specific surface area. Surface modification can control the specific surface area and surface properties by introducing functional groups or coating layers onto the surface of the material. Environmental factors and operating conditions in the processing also impact the specific surface area. For example, factors like ambient temperature, humidity, and atmosphere can affect the preparation process and final performance of the material. Additionally, parameters such as stirring speed, drying methods, and gas flow during the operation may also influence the specific surface area of the material.