Inorganic powders mainly include silicates, carbonates, sulfates, oxides, and hydroxides. They are widely used in advanced, environmental, and traditional industries. These new materials have fine and well-distributed particle sizes. Another key feature is surface modification based on application. Surface treatment improves the powder’s performance in use. It enhances dispersion and compatibility with other components. It also affects adsorption, catalysis, electrical and optical properties. Rheological behavior can also be improved through modification. Powder surface modification equipment precisely adjusts surface properties to enhance performance and value. Core technologies enable nanoscale coating, chemical bonding, or physical adsorption. These significantly improve powder dispersion, stability, and functional compatibility.
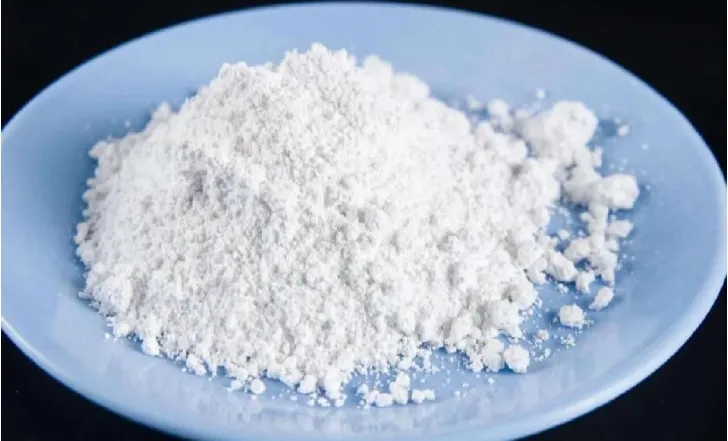
Selection of Powder Surface Modification Equipment
Powder surface treatment includes methods, processes, agents, and equipment. When process and agent formula are fixed, surface modification equipment becomes a key factor. It directly affects the final surface treatment result.
The performance of surface modification equipment is not determined by its speed or the complexity of its structure. The following basic process characteristics should be noted:
- Dispersibility of powder and surface modifier;
- Opportunity for contact or interaction between powder and surface modifier;
- Modification temperature and residence time;
- Energy consumption and abrasion per unit product;
- Dust pollution;
- Operation status of equipment
No matter what kind of surface modification equipment is used, it must be based on the surface modification mechanism and surface modification process to meet the technical requirements of ultrafine powder surface modification. The surface modification equipment should be heated under high-speed dynamic conditions, and be able to keep warm and remove volatile gases. At the same time, the surface modifier can be added in stages and has a grading function to solve the agglomeration problem of surface modification, thereby ensuring the quality of the product.
Powder surface modification equipment
With modern industry advancing, powder performance demands are rising. To gain market share, companies invest more in research. Various powder modification devices have emerged. Modification processes have shifted from batch to continuous. Three-roller coating machine are now available. Dry-only methods evolved into dry-wet combined processes. Examples include ultrafine grinding and surface modification systems. Also, continuous drying and surface treatment integration systems. These integrated systems enable shared data during modification. They improve production efficiency and boost economic benefits.
three-roller coating machine
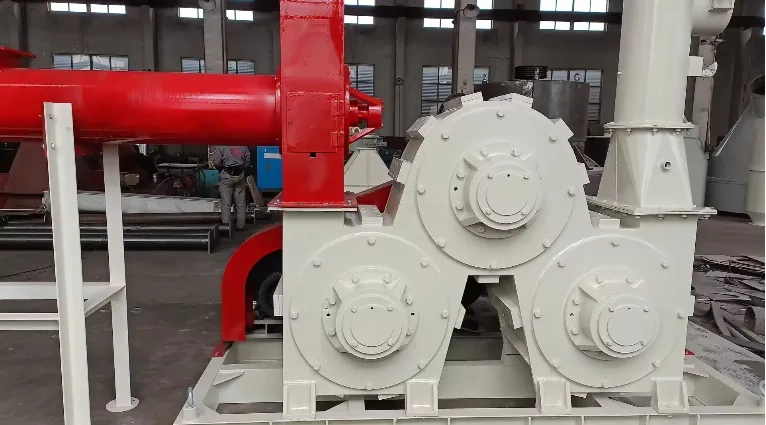
This continuous powder surface coating system is designed on the base of German know how with Chinese equipment, and can be used for coating of various powders like calcium carbonate (GCC, PCC), kaolin, talc, mica, graphite, barium sulfate, white carbon black, magnesium hydrate, zinc oxide, aluminum oxide, and is suitable for a variety of solid/liquid coating agents, like aluminate coupling agent, titanate coupling agent, silane coupling agent and stearic acid.
Coating machine consists of three units of mixing rooms. High-speed rotation creates great vortex flow inside these special-shaped rooms. Powder and coating agent are mixed in the high-speed gas-solid vortex flows. Coating machine with both surface coating and particle dispersing functions is suitable for various powders with different fineness, and has a unique coating effect for the materials with small apparent specific gravity and high volume to weight ratio. Automatic temperature control system ensures stable high temperature for coating agent melting into liquid and mixing with uncoated powder. Heating and cooling of powder and coating agent are completed in one machine, which does not need independent cooling system.
High utilization ratio of coating agent, high powder-coated rate, high activation grade, low energy consumption, and very few agglomerates in final coated product. The whole system is operated under negative pressure, no dust emission, and low labor intensity.
Honeycomb mill coating machine
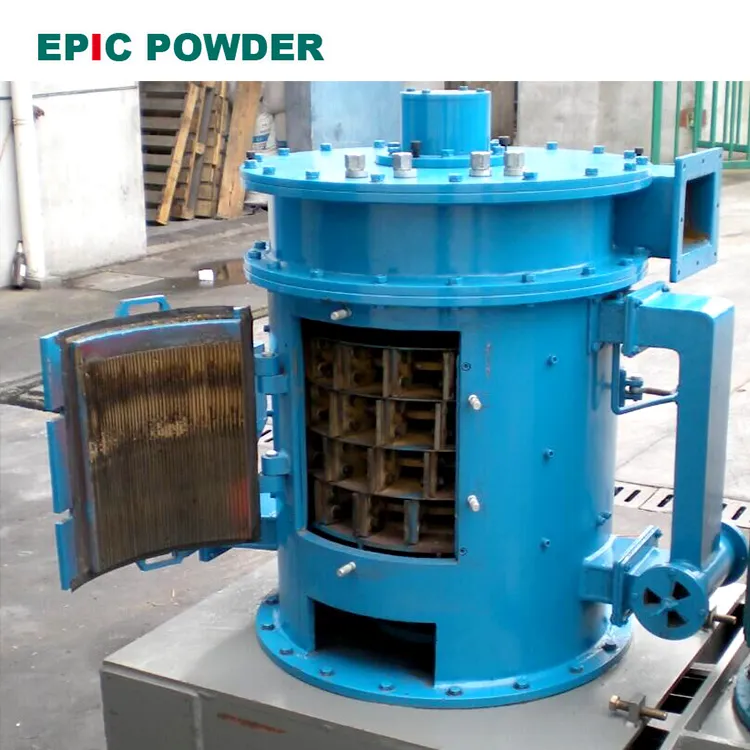
- Honeycomb mill is a mechanical grinding machine that advocates the practical process of first depolymerization and then drying, and synchronous surface treatment. It is specifically designed for the production of ultrafine powders with strict requirements for particle size distribution.
- Simultaneously achieve grinding, drying, sorting, and surface chemical treatment with powder, while drying and depolymerizing wet grinding filter cake and slurry.
- The minimum processing capacity is 0.05 tons/hour, the maximum is 15 tons/hour, and the maximum water evaporation capacity is 3 tons/hour.
- According to the diversity of materials, different materials can be used inside the equipment, which have the advantages of retaining the color and purity of the materials. The coating rate can reach 99.2%, and the activation rate can reach 99.8%.
pin mill coating machine
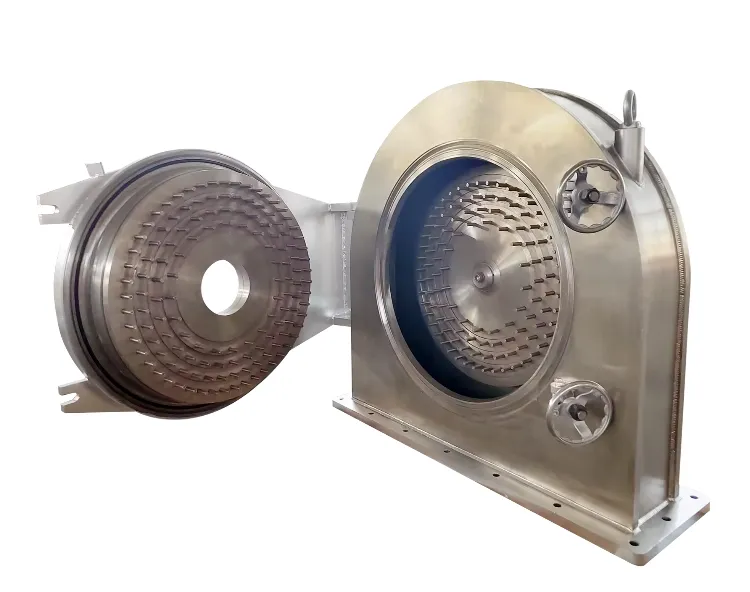
The EPIC’s proprietary injector design achieves a high degree of atomization of the coating fluid, while the high tip speeds produced by the counter-rotating pin disks provide the high shear forces required for proper dispersion and uniform coating. Each coating system is custom designed for the application and includes all auxiliary equipment. Because of its unmatched efficiency, the Pin mill for the Calcium carbonate coating system consumes less power and fluid than any other method in use today.
- This machine provides continuous coating process.
- This type of machine is very popular in European and American markets.
- Two motors run in opposite direction. The linear speed can be up to 240m/s.
- High speed impact, shear and friction leads to full dispersion of materials and due to it, temperature of the material rises resulting in powder modification completely.
turbo mill coating machine
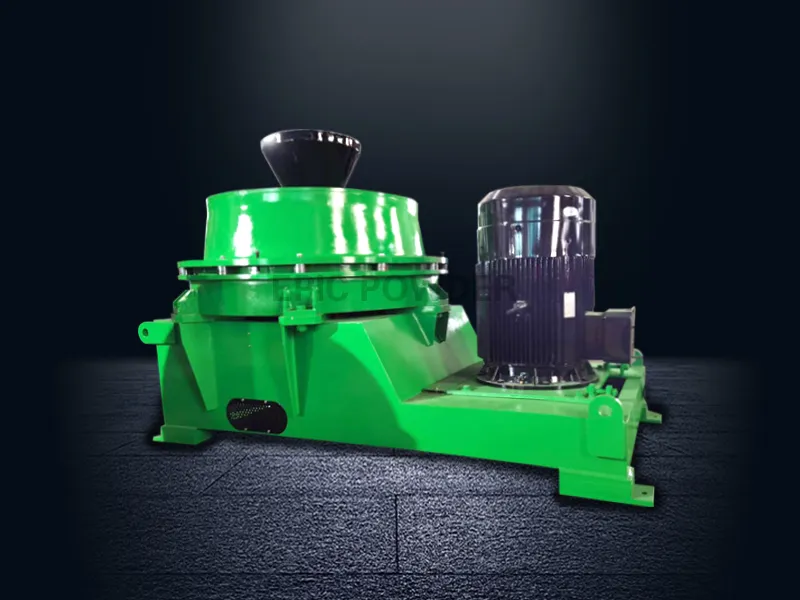
EPIC Powder combines advanced powder modification technology at home and abroad, and independently developed UCOAT series continuous modification equipment. The modification rate of vortex mill coating machine is up to 99%, and the product quality is stable.
- Turbo mill coating machine is composed of frame, body, stator, rotor, filling hopper, bearing seat and motor. The Turbo mill coating machine has the features of high rotational speed, long service life, convenient maintenance and high crushing efficiency.
- Heavy calcium carbonate is a kind of energy-saving, green and environmental protection mineral material. Due to its special physical and chemical properties, as well as its low price and wide sources, it has become one of the main modified powders of Turbo mill coating machine.
conclusion
For many years, significant investment in funds and manpower has been made in the surface modification of ultrafine inorganic powders to drive technological innovation. What are the recent innovations in powder surface modification equipment? How should one choose suitable modification equipment? And what are the applications of modified powders?
Epic Powder, 20+ years of work experience in the ultrafine powder industry. Actively promote the future development of ultra-fine powder, focusing on crushing,grinding,classifying and modification process of ultra-fine powder. Contact us for a free consultation and customized solutions! Our expert team is dedicated to providing high-quality products and services to maximize the value of your powder processing. Epic Powder—Your Trusted Powder Processing Expert !