In the preparation process of lithium battery negative electrode materials, grinding is one of the most critical steps. The negative electrode materials are responsible for storing and releasing energy, greatly impacting core indicators like first-cycle efficiency and cycle performance. As the initial step in preparing high-quality negative electrode materials, grinding fundamentally establishes the material’s performance.
Generally, grinding reduces the size of solid particles using mechanical equipment. Large materials are broken into smaller pieces, which are further ground into finer powders. Mechanical mills and air jet mills can be used to grind graphite materials.
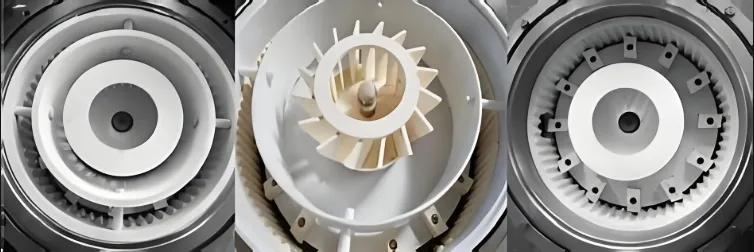
Carbon materials and their products are composed of particles of different sizes. The size, quantity, physical and chemical properties, shape, and surface condition of graphite particles significantly impact the battery production process and its performance. The following image is a typical particle size distribution chart for graphite. The distribution follows a normal distribution, and the chart shows a “peak” shape.
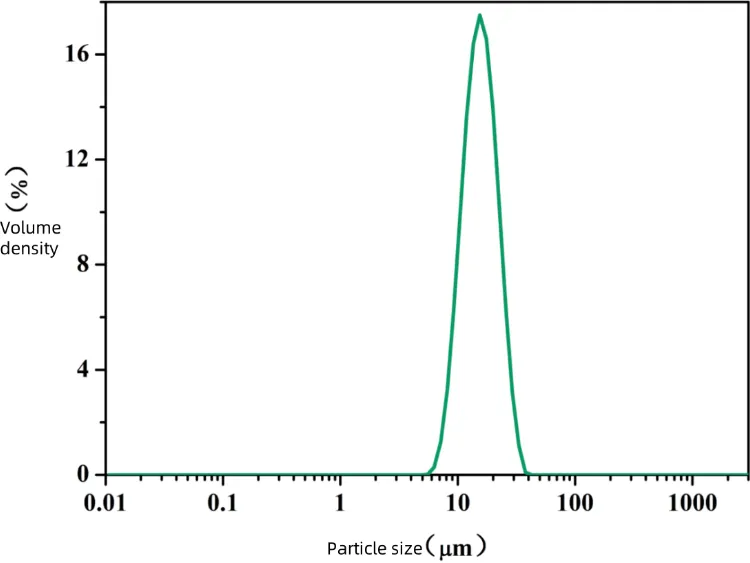
Artificial graphite
For artificial graphite particles, the ideal particle size distribution follows a normal distribution.
In the particle size chart, the normal distribution appears as a symmetric structure. When the “peak” structure is narrow, it indicates uniform particle size, with consistent gaps between graphite particles. This improves the contact area between active materials and the electrolyte, thereby enhancing the lithium-ion diffusion coefficient.
At the same time, the particle size distribution of graphite particles directly affects the battery slurry process and volumetric energy density. An appropriate particle size can increase solid content, reduce coating difficulty, and allow smaller particles to fill gaps between larger ones. This helps increase the electrode’s compaction density and improves the battery’s volumetric energy density.
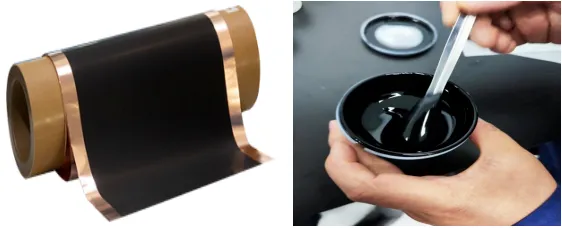
When preparing artificial graphite for negative electrodes, selecting the appropriate crushing equipment is crucial. We choose the right equipment based on process requirements and material characteristics. For calcined coke, we typically use mechanical grinding methods. As asphalt is soft and highly viscous, using mechanical mills can easily cause blockages and damage the equipment. Therefore, we usually opt for air jet mills for grinding asphalt.
Generally, among the particle size data of artificial graphite (D10, D50, D90), we focus most on the D50 value. The relationship between D10, D50, and D90 can provide valuable insights. While particle size indicators offer a reference, they should not be the sole performance criterion. We also need to analyze and evaluate additional data, such as SEM, XRD, electrochemical testing, and tapped density. This helps guide process improvements and optimization.
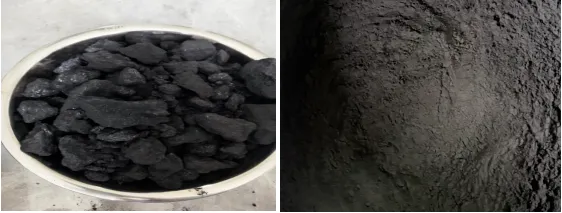
Natural graphite
Natural graphite, as a key source of lithium-ion battery negative materials, is widely used in power batteries and energy storage due to its abundant reserves, low cost, and stable layered structure. However, the flake structure, impurity content, and particle morphology of natural graphite significantly affect its electrochemical performance. Therefore, its crushing process must strike a balance between particle size control, structural preservation, and purity enhancement.
After mining, natural graphite ore typically comes in block or coarse particle form, requiring crushing to produce micron-sized (10-25 μm) negative electrode materials.
The core process goals include:
- Delaminating the Layered Structure: Using mechanical force to separate the graphite layers, exposing more active surface and improving lithium-ion insertion/extraction efficiency.
- Controlling Particle Size Distribution: Optimizing the D50 (median particle size) and D90 (upper limit of 90% particle size) to reduce volumetric expansion stress during charge and discharge cycles.
- Removing Impurities: Natural graphite often contains mineral impurities like quartz and clay, which must be reduced through sorting and crushing processes to lower metal ion content (e.g., Fe < 50 ppm).
- Structural Protection: Avoiding excessive crushing that could damage the graphite crystal structure, preventing a reduction in conductivity.
Natural graphite crushing process
Pre-treatment and Purification
- Coarse Crushing and Flotation: The raw ore is first crushed to 5-10 mm using a jaw crusher, followed by flotation to remove impurities like quartz and mica, increasing the carbon content to ≥99%.
- High-Temperature Purification: Some high-sulfur natural graphite requires treatment at temperatures above 2800°C to remove volatile impurities (such as sulfur and oxygen), achieving carbon purity of over 99.95%.
Primary crushing:
After pre-treatment, natural graphite enters coarse crushing equipment, such as a jaw crusher or hammer crusher. During the coarse crushing process, strict control of the equipment’s operating parameters is essential. Typically, natural graphite is crushed to a particle size range of 10-50 mm.
Fine grinding and classification:
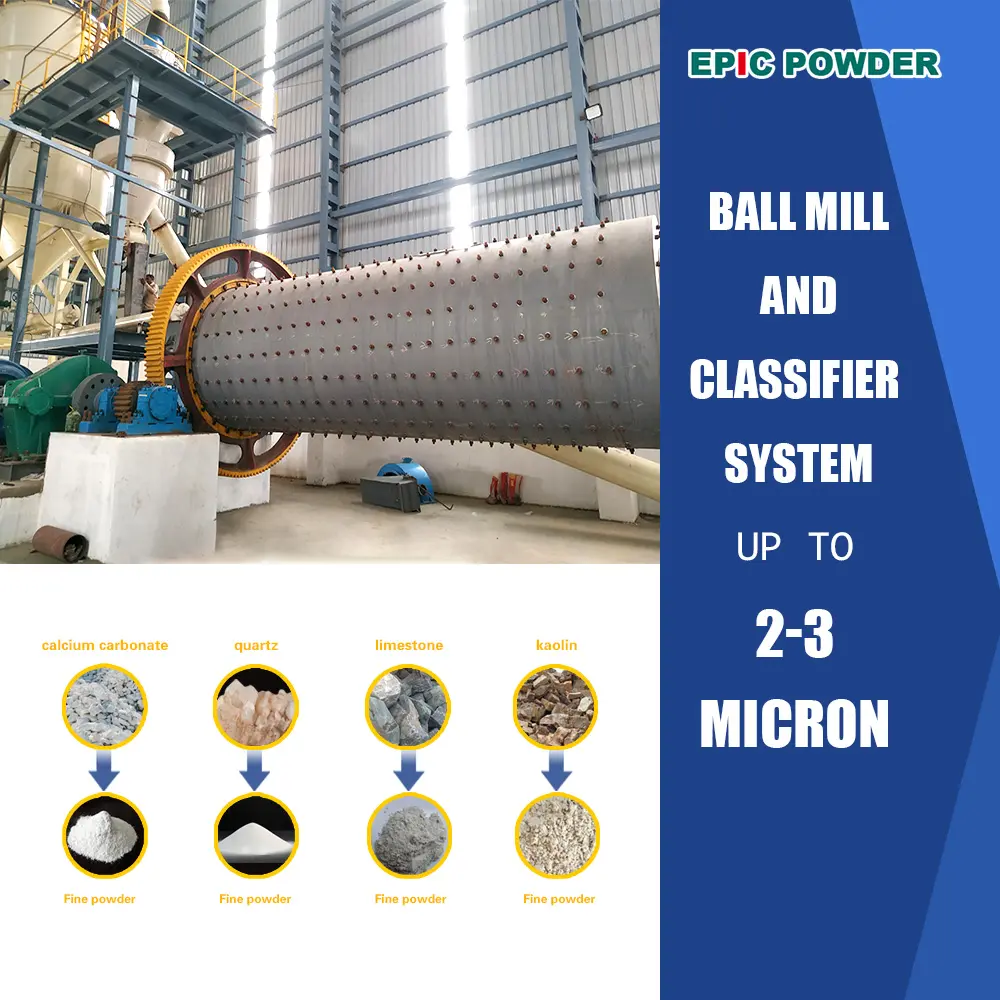
If a ball mill is used, the type and size ratio of the grinding media, ball-to-material ratio, and parameters such as the mill speed and grinding time must be precisely adjusted based on the raw material characteristics and target particle size.
If an air jet mill is used, it is important to control parameters such as air pressure, flow rate, and feeding speed to ensure that natural graphite is evenly crushed to the desired particle size under the action of the airflow.
After grinding, the natural graphite particles are classified using classification equipment. Common classification equipment includes cyclone separators and air classifiers. These devices use the movement characteristics of particles in the airflow to sort the natural graphite particles into different grades based on particle size, collecting products that meet the target particle size range.
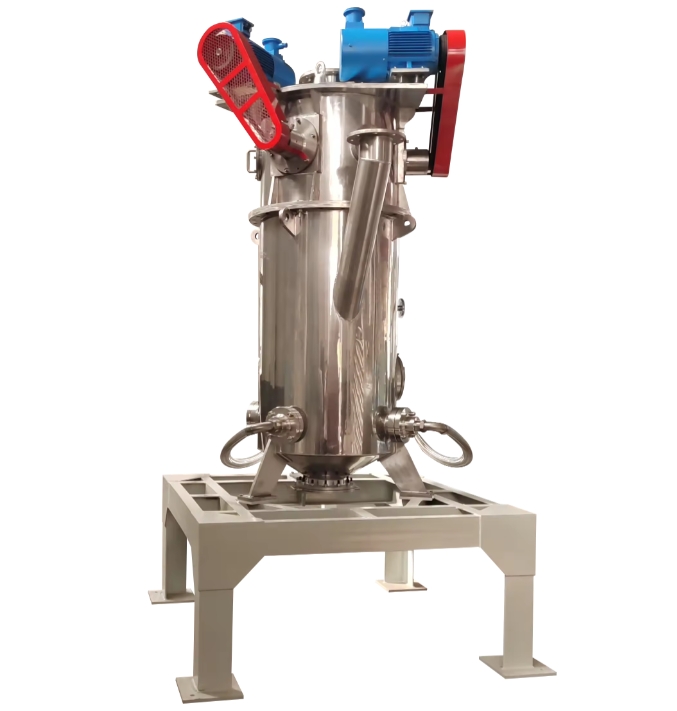
Conclusion
The quality of the negative electrode grinding process affects battery capacity, lifespan, and safety. A quality process ensures uniform distribution of negative materials, matching well with other components. Fine grinding and strict particle size control enable better lithium-ion storage, improving energy density and increasing range. A reasonable process reduces capacity degradation during battery cycles, extending service life. Avoiding impurities and ensuring consistent particle size can reduce safety risks, such as short circuits and overheating.
In conclusion, the negative electrode grinding process is crucial in lithium battery production.
From raw material analysis, equipment selection, to process control and product performance, every step is interconnected. Continuously optimizing this process lays the foundation for high-performance, long-lifetime, and safe lithium batteries. This drives the development of the new energy battery industry.
epic powder
Epic Powder, 20+ years of work experience in the ultrafine powder industry. Actively promote the future development of ultra-fine powder, focusing on crushing,grinding,classifying and modification process of ultra-fine powder. Contact us for a free consultation and customized solutions! Our expert team is dedicated to providing high-quality products and services to maximize the value of your powder processing. Epic Powder—Your Trusted Powder Processing Expert !