In the rubber industry and many fields of materials science, a substance called white carbon black plays an important role. Many people may know that the white silica powder is commonly referred to as white carbon black. But how did it get this name? To answer that, we need to look at its connection to carbon black.
The understanding of carbon black has a long history. Over 3,000 years ago, people had already mastered the technique of burning smoke to make ink. However, the production technology for carbon black advanced slowly for a long time. It wasn’t until 1872 that the carbon black industry began large-scale production, and the term “Carbon Black” came into use.
In 1912, the reinforcing effect of carbon black on rubber was discovered, particularly its ability to significantly improve the wear resistance of tires. This led to a surge in demand for carbon black, making it an indispensable material in the rubber industry. During World War I, there was a shortage of energy materials for carbon black production.
Germany began using precipitated white silica as a substitute. This white amorphous silica has similar properties and uses to carbon blacks.
That is why it is called white carbon black.
With the rapid development of the automotive and transportation industries, and rising raw material costs for carbon black, the demand for energy conservation and emission reduction grew. As a result, the role of white carbon black as a reinforcing material in the rubber industry has become more important.
Today, white carbon blacks can completely replace carbon black for reinforcement in colored rubber products. It meets the need for white or translucent products, which performs exceptionally well in manufacturing car “green tires” and winter tires. It helps tires achieve lower rolling resistance and better traction, improving fuel efficiency.
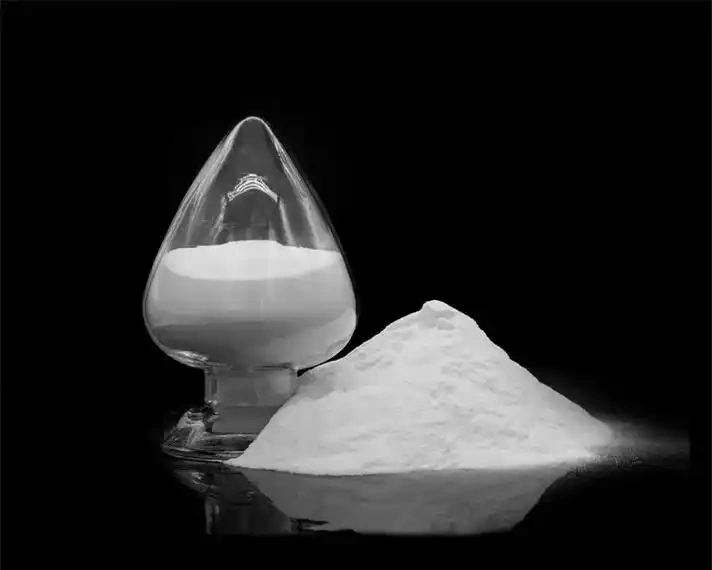
Preparation method of white carbon black
There are many methods for preparing silica, which are mainly divided into precipitation method and gas phase method.
Precipitated white carbon black is commonly produced using a neutralization precipitation reaction between silicates (usually sodium metasilicate) and inorganic acids (typically sulfuric acid) to produce hydrated silica.
Its particle size is about 20-40nm, with lower purity and weaker reinforcing properties compared to fumed silica. The dielectric properties of the rubber compound, especially after moisture exposure, are also poorer. However, it is cheaper and has better processing performance. It can be used alone in general rubbers like NR and SBR, or mixed with carbon black to improve the rubber’s resistance to flex cracking, slowing crack growth. Fumed silica, on the other hand, is produced by the thermal decomposition of polysilicic halides (SiClx) at high temperatures, through a vapor-phase reaction. It is also known as the calcination or dry method of white carbon blacks ssproduction.
Dry method white carbon black has an extremely small particle size, around 15-25nm, with high dispersibility and low impurities. It offers good reinforcement properties, but its preparation is complex and costly. It is mainly used in silicone rubber, producing transparent or translucent products. These products have good physical, mechanical, and dielectric properties, with excellent water resistance.
Structure of white carbon black
Structurally, about 95-99% of white carbon black is composed of SiO₂. The structure of white carbon blacks varies depending on the preparation method. Fumed silica has an internal structure that is almost entirely composed of a tightly packed three-dimensional silicate network. This structure results in low moisture absorption, strong surface adsorption, and excellent reinforcement properties. In contrast, precipitated silica, besides forming a three-dimensional silicate structure, also retains a significant amount of two-dimensional silicate structures. This makes the structure more porous, with many capillary structures, making it more prone to moisture absorption, thus reducing its reinforcing activity.
The basic particles of white carbon blacks are spherical. During production, these particles collide at high temperatures to form chain-like structures connected by chemical bonds. The chain-like structures are further bonded by hydrogen bonds to form secondary aggregates. These aggregates are easily broken during the mixing process.
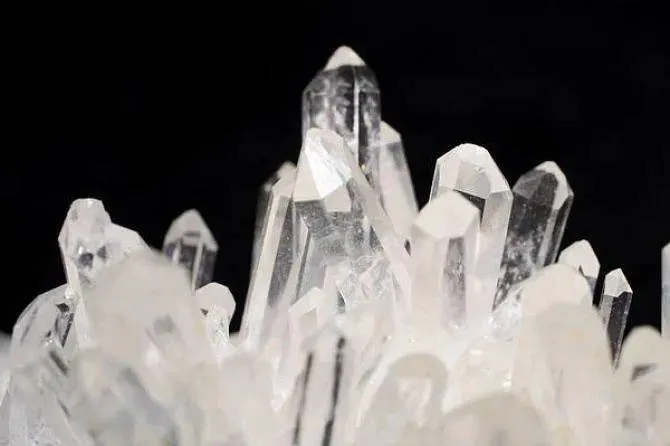
Surface chemical properties of silica
Its surface contains adjacent hydroxyl groups, isolated hydroxyl groups, and dihydroxyl groups. Fumed silica has more surface hydroxyl groups than precipitated silica, which are difficult to remove at higher temperatures. These surface groups are reactive, including dehydration and hydrolysis reactions, reactions with acyl chlorides, reactions with active hydrogen, and hydrogen bond formation. The surface of white carbon black has strong chemical adsorption activity, which is related to its surface hydroxyl groups.
It can bond with water through hydrogen bonds, forming a multilayer adsorption. In addition, it can adsorb many organic small molecules. Amines or alcohols with multiple functional groups have higher adsorption than single-functional groups. Therefore, in SiO₂ compounds, multi-functional agents like ethanolamine, ethylene glycol, and triethanolamine are often used as activators. When white carbon black is heated, moisture is released. The most moisture is released between 150-200°C.
After 200°C, the release rate slows down, with a clear turning point. Before the turning point, adsorbed water is desorbed. After the turning point, surface hydroxyl groups undergo condensation reactions. There are two ways to prevent structuring. One is to add substances during mixing that can react with the surface hydroxyl groups of white carbon black, such as hydroxyl siloxane, diphenylsilane glycol, or silazane. The other way is to pre-modify the surface of white carbon black by removing some of the surface hydroxyl groups.
Reinforcement effect on silicone rubber
White carbon black is a white reinforcing agent with reinforcement properties second only to furnace black. Vulcanized rubber with a certain amount of white carbon black has higher strength. It also has greater elongation, higher tear strength, higher hardness, and better insulation.
Typically, carbon black and white carbon black are used together for better overall performance. However, white carbon black still has issues with processing, static electricity, and cost. Its development direction focuses on higher dispersibility, refinement, granulation, and surface modification. These improvements aim to enhance its role in material fields.
conclusion
White carbon black, with its unique advantages, has deeply integrated into the rubber industry. From improving product performance to driving technological innovation and expanding application boundaries, its value is immeasurable.
It is not only a key additive for enhancing rubber performance but also an important driver of industry development and innovation.
It occupies an indispensable core position in the rubber industry, continuously injecting strong momentum into the industry.
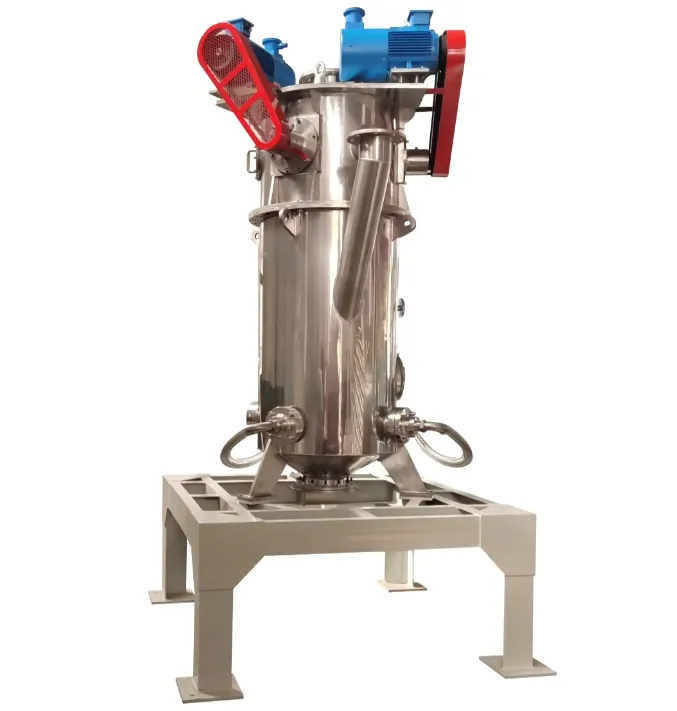
epic powder
Epic Powder, 20+ years of work experience in the ultrafine powder industry. Actively promote the future development of ultra-fine powder, focusing on crushing,grinding,classifying and modification process of ultra-fine powder. Contact us for a free consultation and customized solutions! Our expert team is dedicated to providing high-quality products and services to maximize the value of your powder processing. Epic Powder—Your Trusted Powder Processing Expert !