In high-temperature industries like metallurgy, ceramics, and refractories, kiln furniture (saggers, setters, columns, pushers, rollers, and setters) serves as core consumables for supporting and carrying workpieces.
These materials endure extreme temperature fluctuations (1200–1600°C), mechanical alternating loads, and corrosive/oxidative atmospheres.They face stringent demands for thermal shock resistance, high-temperature load capacity, chemical corrosion resistance, and longevity.
Mullite-cordierite composite ceramics overcome limitations of single-phase ceramic kiln furniture through material complementarity.
This composite combines high-temperature resistance, mechanical strength, and outstanding low thermal expansion coefficient.
Its exceptional thermal shock resistance makes it a widely adopted high-end kiln material.
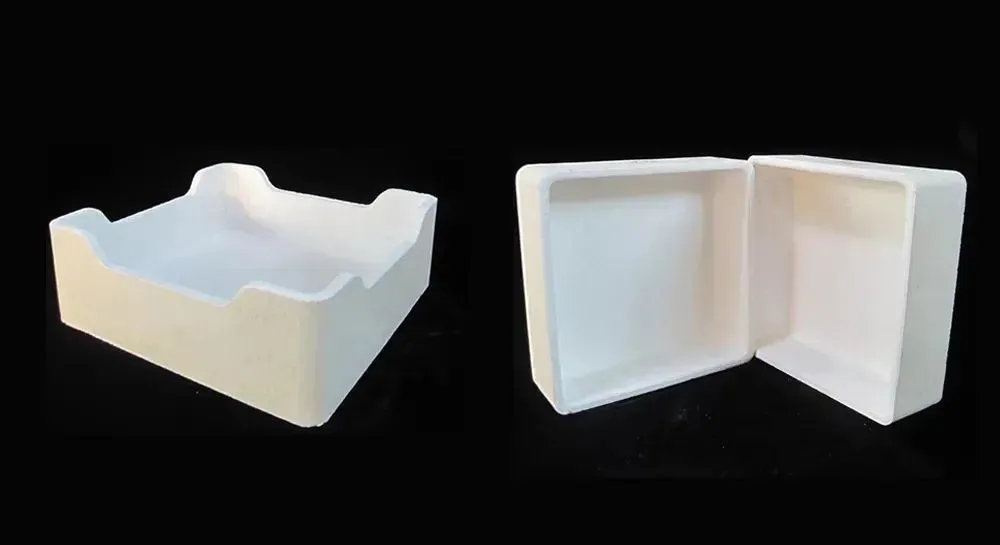
Advantages of mullite and cordierite composite
Mullite (MA) is the sole stable binary compound in the Al₂O₃-SiO₂ system.
Its chemical formula is 3Al₂O₃·2SiO₂, featuring crystal structures of silica-aluminum tetrahedrons arranged along the C-axis.
Aluminum-oxygen octahedrons bridge dual chains, forming a skeletal framework that ensures high mechanical strength. With a Mohs hardness of 6.7, it maintains structural stability at high temperatures due to strong Al-O bonds.
The material’s high Al₂O₃ content (~72-78%) supports a melting point near 1900°C.
This enables resistance to melting, softening, and creep in high-temperature furnace environments.
However, its high thermal expansion coefficient (5×10⁻⁶/K) induces stress cracks during rapid cooling.
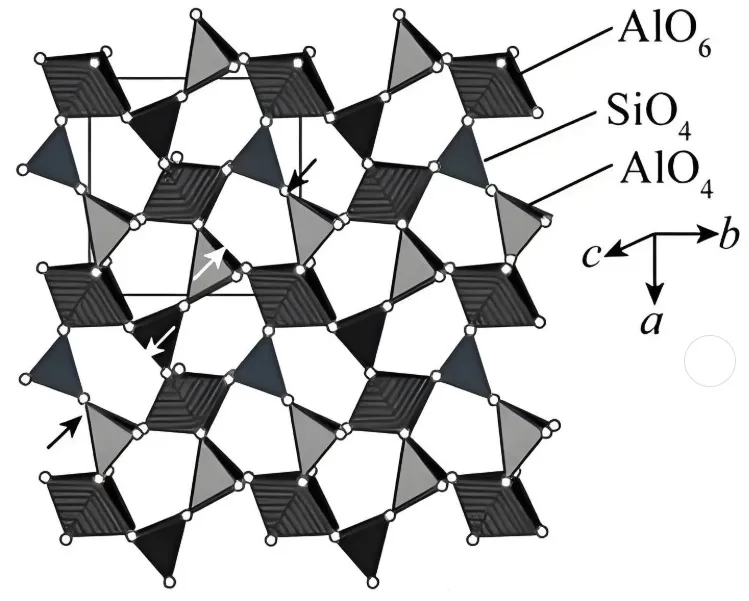
Cordierite’s chemical composition is 2MgO·2Al₂O₃·5SiO₂, existing in α, β, and μ crystalline forms.
The α-phase (high-temperature form) contains hexagonal rings of [SiO₄] and [AlO₄] tetrahedra aligned along the c-axis.
Inter-ring connections form via edge-sharing [AlO₄] tetrahedra and [MgO₆] octahedra, creating anisotropic thermal expansion.
Radial contraction occurs in hexagonal rings due to transverse oxygen vibrations under heating, offsetting axial expansion.
This unique structure achieves ultralow thermal expansion coefficients (<2×10⁻⁶/°C), ideal for thermal shock resistance.
However, weak Mg-O ionic bonds between rings result in inferior mechanical strength compared to covalent ceramics. In the MgO-Al₂O₃-SiO₂ system, low eutectic phases form, reducing its practical melting point to ~1,460°C.
Consequently, cordierite’s service temperature is limited to 900-1,280°C, restricting ultra-high-temperature applications.
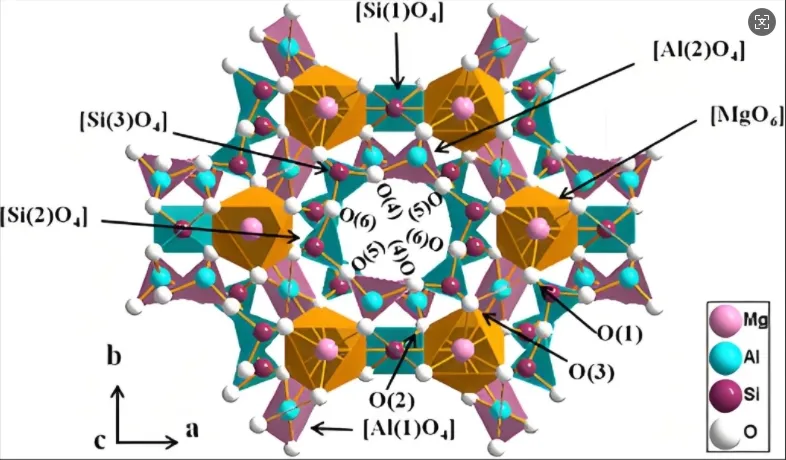
Combining cordierite and mullite creates composites that leverage mullite’s strength to offset cordierite’s mechanical weaknesses.
Embedded mullite grains enhance fracture toughness through grain boundary interlocking and crack deflection mechanisms.
Thermal expansion mismatch between phases generates microcracks at interfaces, reducing thermal stress concentration.
These microcracks absorb energy during rapid temperature changes, significantly improving thermal shock stability.
Disadvantages of Mullite-Cordierite Composite Ceramics and Solutions
Mullite-cordierite composite ceramics use clay, talc, mullite, and cordierite as main raw materials.
After firing, they contain mullite, cordierite, corundum, quartz, and spinel phases.
High porosity and low bulk density reduce durability at high temperatures.
Clay binders react with active elements like Li+ from decomposing battery cathode materials.
This leads to corrosion, shortens sagger lifespan, and may contaminate products.
Although stronger than cordierite, internal stresses from oxidation and decomposition occur during firing.
If these stresses exceed strength limits during use, cracking may happen. In order to improve the service life of cordierite-mullite composite ceramics in a corrosive environment, the following measures can be adopted:
Adding Spinel
Cordierite and mullite both contain silica phases. During cathode material preparation, released Li⁺ reacts with cordierite to form spinel. Subsequent decomposition generates magnesia (MgO), while mullite undergoes complete breakdown. MgO and magnesium-aluminum spinel exhibit superior lithium corrosion resistance compared to silica-rich phases.
Introducing these phases reduces SiO₂ content, enhancing composite anti-corrosion performance in lithium environments.
Structural Composite
Introducing corrosion-resistant materials (e.g., zirconia) as coatings or inserts can reduce active element erosion.
This significantly extends sagger lifespan by protecting the composite layer.
However, over long-term use, lithium compounds may still penetrate and react with the substrate, causing damage.
Kiln furniture structure optimization
To release stress from firing, kiln furniture can be structurally optimized.
Methods include cutting vertical slits, smoothing joints, and adding special channels or holes.
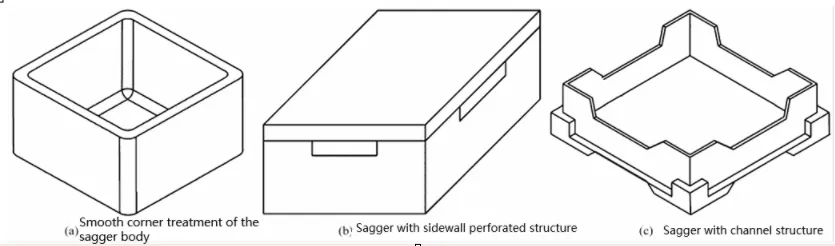
conclusion
Ball milling critically enhances mullite-cordierite composites’ thermal shock resistance by refining particles and homogenizing element distribution.
Optimized milling parameters (e.g., 200-450 rpm, 1-8h duration) ensure strong phase bonding and structural stability.
Enhanced stability enables superior thermal shock resistance through coordinated stress dissipation mechanisms.
In the future, further research on the impact of ball milling on the microstructure and properties of mullite-cordierite composite ceramics is expected. This will provide stronger technical support for the material’s widespread application in more high-temperature and complex thermal environments.
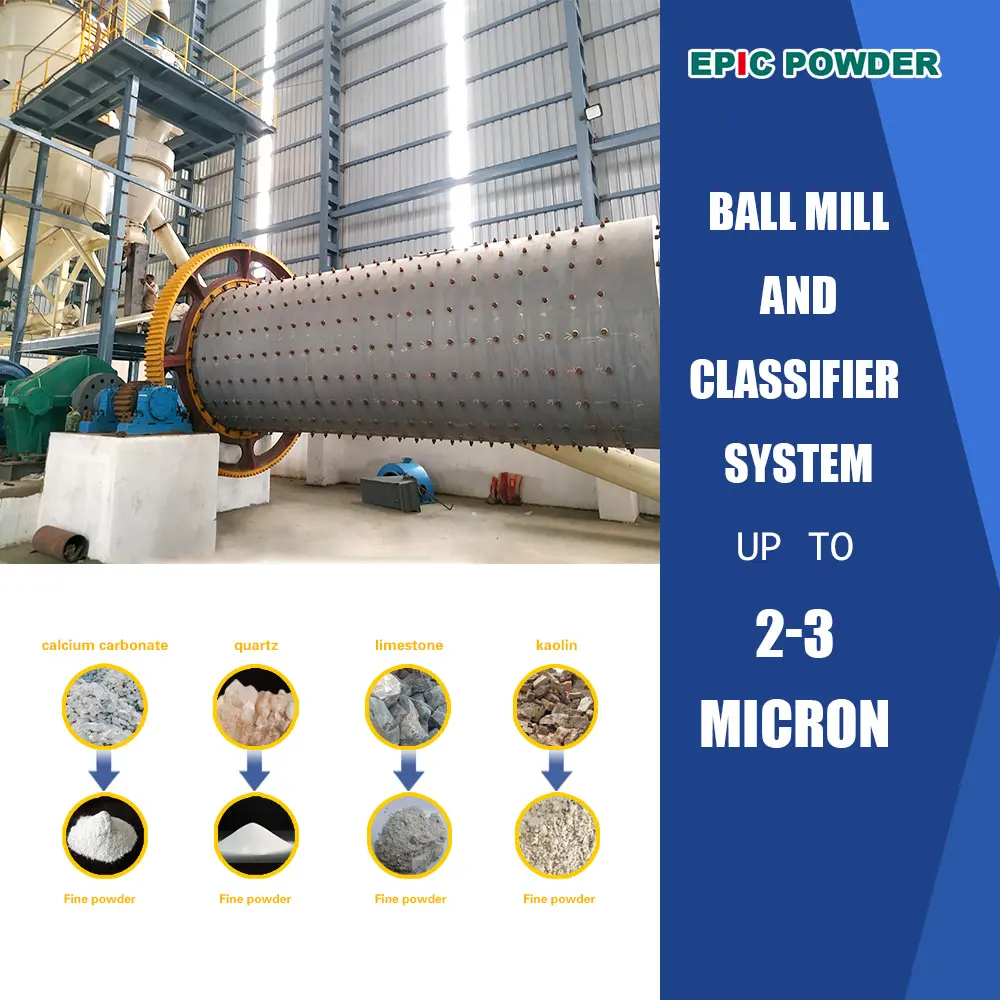