Anode materials for lithium batteries are divided into carbon-based and non-carbon-based types. Carbon-based materials include natural graphite anodes and artificial graphite anodes. Also include mesocarbon microbeads (MCMB), soft carbon (e.g., coke) anodes. Hard carbon anodes, carbon nanotubes, graphene, and carbon fibers are also included. Non-carbon-based materials mainly include silicon-based anode and composite materials. They also include nitride anodes, tin-based materials, and lithium titanate. Alloy materials are also part of non-carbon-based anodes.
Currently, commercial anode materials are mainly graphite. Graphite anodes have a theoretical capacity of 372 mAh/g. High-end commercial graphite reaches 360–365 mAh/g capacity.
It is already close to the theoretical limit. Improving graphite anodes brings limited energy density gains.
Silicon is a promising lithium battery anode material. Elemental silicon has a theoretical capacity of 3579 mAh/g. It offers much higher capacity than graphite anodes.
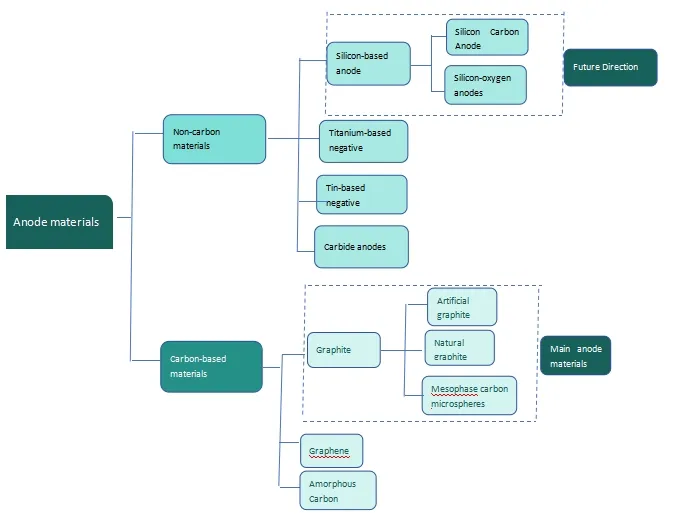
Structure and Performance Characteristics of Silicon-Based Anode Materials
Silicon-based anodes mainly consist of silicon and graphite. Silicon has outstanding advantages as an anode material.
- First, silicon alloys with lithium at room temperature. Its theoretical capacity reaches 4200 mAh/g. That’s over ten times graphite’s theoretical capacity.
- Second, silicon is abundant in Earth’s crust. It makes up 25.8% of the crust’s mass, which is the second most abundant crustal element.
- Third, silicon has a higher voltage platform (~0.4 V). It avoids lithium plating risks and improves safety.
- Fourth, silicon performs better than graphite at low temperatures.
- Fifth, it offers multi-directional lithium-ion transport paths. This gives silicon excellent fast-charging capability. Silicon anodes may replace graphite as the ideal choice.
However, using silicon as a lithium battery anode faces major challenges:
- Silicon anodes expand and shrink during lithium insertion/extraction. Volume change can exceed 300%, causing high mechanical stress. After many cycles, silicon particles crack and pulverize. This severely hinders lithium-ion transport within the anode. It results in low initial efficiency and poor cycle life.
- During charge/discharge, silicon particles fracture. Active particles lose contact with the current collector. This creates an “island effect” with poor conductivity. Fracture surfaces repeatedly form new SEI layers. This causes irreversible capacity loss and low Coulombic efficiency.
- Silicon is a semiconductor with low electrical conductivity (10⁻⁵–10⁻³ S·cm⁻¹). It also has a low lithium-ion diffusion coefficient (10⁻¹⁴–10⁻¹³ cm²·s⁻¹). These factors reduce lithium-ion diffusion kinetics and performance.
- The nanostructure effect will cause problems such as large specific surface area and low tap density
- It is necessary to develop new electrolyte systems and bonding systems to meet the application process requirements of the materials.
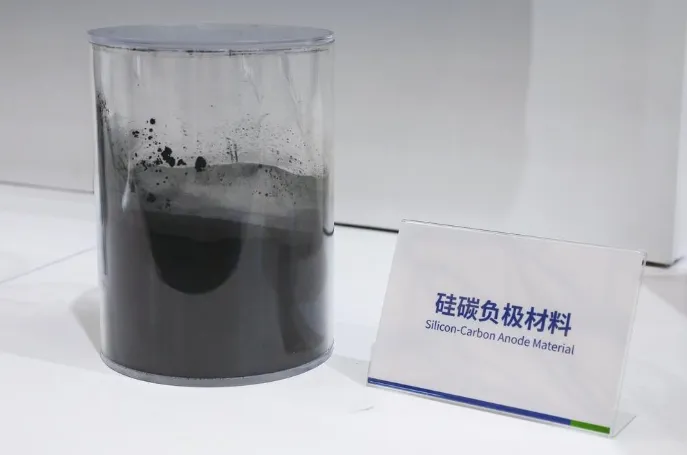
Solutions to the Problems of Silicon-Based Anodes
Due to silicon’s inherent defects, nanostructuring and carbon coating are required. These treatments are complex and technically demanding. Currently, only a few companies have mastered the process. Each company uses different, proprietary processing methods. There is no standardized industrial process at present.
From the process route, silicon-based anodes include silicon-carbon and silicon-oxygen types. Silicon-carbon anodes have a commercial capacity below 450 mAh/g. They are mainly used in 3C digital products. Silicon-oxygen anodes offer 450–500 mAh/g in commercial use. They are mainly applied in power battery systems.
Silicon-Carbon Anode Solutions:
Both silicon-carbon and silicon-oxygen still face industrialization challenges. For silicon-carbon, expansion is a key issue. It is usually addressed by carbon-coating nano-silicon particles. This reduces volume change and improves stability. Silicon-oxygen anodes improve first-cycle efficiency differently. They typically use pre-magnesium or pre-lithiation techniques. These methods enhance initial Coulombic efficiency and performance.
Commercialization Progress of Silicon-Based Anodes
Currently commercialized silicon-based anode materials materials include carbon-coated silicon oxide and nano silicon-carbon. Also includes silicon nanowires and amorphous silicon alloys. Carbon-coated silicon oxide and nano silicon-carbon are most commercialized. They are typically blended into graphite at 5–10%.
These are mainly used in EVs and power tools. Recently, usage is expanding to wearables and consumer electronics. Panasonic, Samsung, and CATL already use such products. Suppliers include BTR and Shanshan Corporation. Tesla has adopted silicon anodes in some models. With 4680 battery mass production, market space will grow.
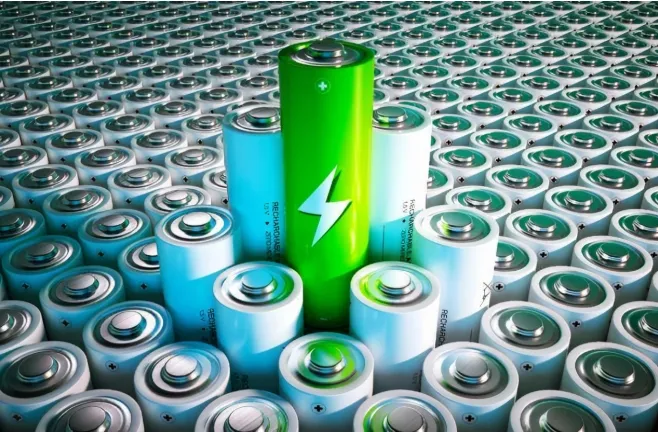
epic powder
Epic Powder, 20+ years of work experience in the ultrafine powder industry. Actively promote the future development of ultra-fine powder, focusing on crushing,grinding,classifying and modification process of ultra-fine powder. Contact us for a free consultation and customized solutions! Our expert team is dedicated to providing high-quality products and services to maximize the value of your powder processing. Epic Powder—Your Trusted Powder Processing Expert !